Data Center Thermal Management
Thermal management is crucial for optimal data center performance. Partnering with ACT enables you to design a cutting-edge thermal architecture that delivers unparalleled energy efficiency, high-performance computing, and space-saving cooling solutions. Maximize your data center’s potential with ACT’s innovative data center cooling systems and solutions.
Maximize Cooling Efficiency for Optimal Data Center Performance
Data Center Direct-to-Chip Liquid Cooling Solutions
As CPU and GPU performance continues to push boundaries, power densities are soaring, creating an urgent need for cutting-edge chip-level cooling solutions capable of dissipating extreme heat fluxes and minimizing thermal resistance. Advanced Direct-to-Chip (D2C) liquid cooling is emerging as a critical technology to tame these scorching hot spots. ACT’s innovative D2C solutions employ microchannel cold plates, jet impingement, and other techniques to provide superior heat transfer coefficients. Our thermally-engineered coolants, precision temperature control, and optimized fluid delivery enable ultra-high heat flux dissipation over 1 kW/cm2. D2C cooling unlocks new performance potential while enhancing reliability. ACT offers custom direct-to-chip liquid cooling solutions for moderate (> 10 W/cm^2) to extreme (> 1000 W/cm^2) heat flux applications:
- Direct contact air heat sinks and spreaders
- Optimized micro-channel cold plates
- Data center cabinet cooling
- Immersion cooling
Data Center Rack-Level Cooling Solutions
High power computing (HPC) density demands a holistic rack-level thermal management strategy that optimizes total heat removal and space utilization. ACT custom designs and integrates complete rack cooling solutions to achieve industry-leading power densities while minimizing infrastructure overhead. Our toolkit includes:
- Forced convection, liquid cooling – internal or external
- Heat pipes and loop thermosyphons
- Pumped single-phase and two-phase
- NEMA-rated sealed enclosure coolers
- Precision cooling control, built-in redundancy, and real-time monitoring ensure reliable “lights-out” operation at maximum compute capacity.
As an example (see Figure 1) a Pumped Two-Phase (P2P) system can significantly increase efficiency from direct liquid cooling and can improve heat density capability from air-cooled systems. ACT’s expertise expands throughout the P2P system, with advanced know-how in cold plate design to enable high-heat-flux capabilities required for next generation CPUs and GPUs, as well as modular hot-swappable racks that use quick disconnects for easy replacement and servicing of server blades within the system. A P2P system leverages fractional horsepower pumps, taking advantage of the latent heat of vaporization (not the fluid velocity like single phase system) to increase power density, allowing for higher power applications with a fraction of the energy consumption.
Room and Data Center Level Cooling
As rack densities climb, traditional computer room air handling is not enough. Facility-level cooling strategies have evolved, incorporating energy recovery and localized computer room air handlers (CRAHs) or computer room air conditioners (CRACs). ACT provides comprehensive facility-level thermal solutions incorporating modern free-cooling methods, localized computer room cooling units, and heat distribution infrastructure. Our approach leverages evaporative cooling, airside/waterside economizers, and energy recovery to drastically reduce cooling costs. State-of-the-art cooling distribution units (CDUs), energy recovery heat exchangers, and large-scale passive loop thermosyphons efficiently move heat from high-density equipment to outdoor dry coolers/cooling towers. Intelligent control maximizes free-cooling hours while maintaining temperature and humidity control.
Best-in-class energy efficiency is possible by leveraging hybrid technology; ACT has developed a hybrid vapor compression system with free cooling capabilities, leveraging our P2P technology. This is ideal for applications that require sub-ambient air conditioning during certain periods but can leverage cool outdoor air a portion of the time. Similarly, ACT has developed pump-assisted passive loop thermosyphons to allow for year operation in vertical or large, split distance, energy recovery heat exchanger applications.
Edge Computing Cooling Systems
Edge computing demands low-latency, high-efficiency, and secure data processing closer to the source. The source can be IOT in air-conditioned factory to large scale military satcom systems deployed to some of the harshest environments in the world and everything in between. While traditional computer room cooling works for IT closets, ACT’s rugged Tekgard® and Vaphtek™ solutions enable true “edge” deployments. In these mobile systems, containerized edge computing with dedicated thermal management, including air conditioning solutions and direct rack-level cooling for high power density applications. The Tekgard® brand is synonymous with ruggedization and reliability, being deployed across the globe for over two decades. These harsh-environment cooling solutions, such as environmental control units (ECUs), hybrid environmental control units and chillers, enable reliable edge computing for military, autonomous vehicle, and industrial applications where performance and durability are critical.
ACT has met challenging outdoor and/or transport requirements for mobile edge computing applications, including:
- Shock and vibration (industrial and MIL-STD)
- EMI Protection
- Corrosion Resistance
- Trailer, wall, or skid mounted options
- Smart control systems
- Active Dehumidification
In-House Testing Capabilities
All of ACT’s thermal management solutions undergo rigorous validation testing in our state-of-the-art R&D facilities before release. This ensures optimized real-world performance in your application. We invest heavily in advanced thermal modeling, instrumentation, environmental test chambers, and accelerated life testing to guarantee reliable, energy-efficient cooling that is tailored to your specific requirements. Our integrated NPI process combines multi-physics simulation and experimental validation to rapidly deliver right-the-first-time designs.
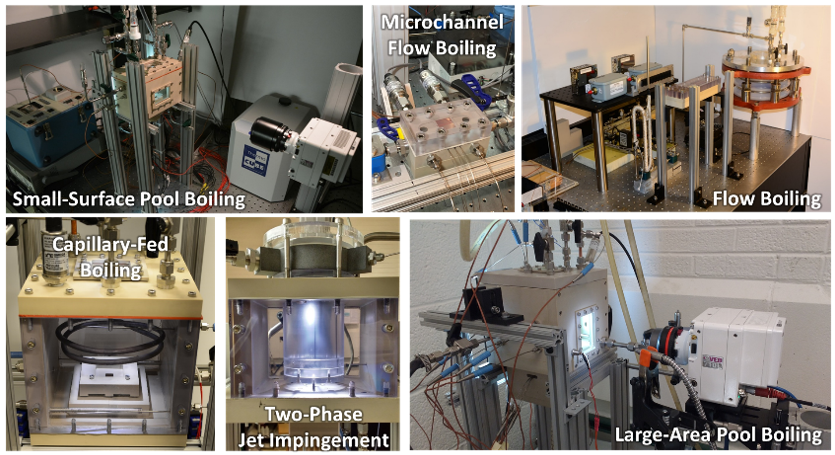

Get expert help on data center cooling from our experts.