- Constant Conductance Heat Pipes
- Variable Conductance Heat Pipes
- Space Copper-Water Heat Pipes
- Loop Heat Pipes
- Space VPX
- Liquid Cooling
ACT delivers proven Constant Conductance Heat Pipe (CCHP) thermal control products
ACT’s CCHP Space Flight Hours:
Precision-Engineered Constant Conductance Heat Pipes (CCHPs) for Aerospace
ACT manufactures Constant Conductance Heat Pipes (CCHPs) to meet the exacting requirements of the aerospace industry. Our CCHPs are produced under ACT’s ISO 9001:2015 and AS9100D certified Quality System, ensuring the highest standards of performance and reliability.
Every component used in our CCHPs, from aluminum extrusions to working fluids, is certified and qualified to meet rigorous aerospace quality standards. Each extrusion undergoes comprehensive characterization to assess its thermal performance and pressure containment capability across different operating temperatures and fluid charges. Additionally, all welding is performed by AWS D17.1-certified welders, following strict aerospace fusion welding specifications.
State-of-the-Art Manufacturing & Testing
ACT utilizes specialized equipment and processes to ensure aerospace-grade quality in every CCHP we produce:
✔ Multi-stage chemical cleaning baths for raw extrusions
✔ Triple distillation apparatus for ultra-pure working fluids
✔ Advanced helium mass spectrometer leak detection
✔ Dedicated charging, processing, and non-condensable gas venting stations
✔ Specialized thermal testing setups for performance evaluation at various temperatures and elevations
With decades of expertise in two-phase thermal solutions, ACT delivers high-performance, flight-ready CCHPs and other spacecraft thermal management technologies tailored to your mission-critical applications.
After undergoing a rigorous physical and chemical cleaning process, each heat pipe is further cleaned in-situ by operating at elevated temperatures with an initial charge of high-purity working fluid, which is then vented. A second high-purity charge is introduced, and the heat pipe is operated for several days under close monitoring. During this time, multiple checks are performed at extremely low temperatures to detect even the slightest presence of non-condensable gases, ensuring their complete removal before final hermetic sealing.
ACT has proprietary heat pipe models to simulate each design application and these models are used to assist with the selection of the right extrusion for each application. This software calculates the capillary limit and the associated thermal transport capability of the heat pipe taking into account the exact extruded groove geometry. The optimum fluid charge is determined for the specific application and the effect of excess fluid charge is determined for both 0-G and 1-G operations. The figure below compares the model predictions and test data on two specific CCHPs.
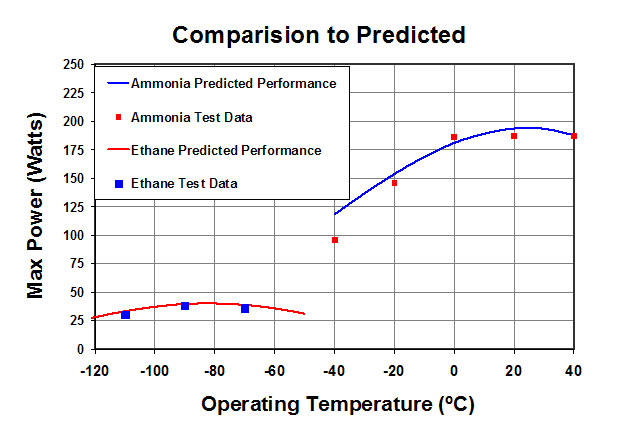
Explore More About CCHPs
Constant Conductance Heat Pipes (CCHPs) play a vital role in spacecraft thermal management, ensuring reliable heat transfer in demanding space environments. Learn more about how ACT’s CCHPs support aerospace missions.
Explore Other Space Heat Pipe Technologies
CCHPs are commonly used alongside other heat pipe technologies in space applications to optimize thermal management.
- Variable Conductance Heat Pipes (VCHPs) – Used alongside CCHPs when temperature control is needed, allowing for adaptive thermal regulation in space environments.
- Loop Heat Pipes (LHPs) – Often paired with CCHPs for high-power, long-distance heat transport, especially when traditional heat pipes are not sufficient.
- Pulsating Heat Pipes (PHPs) – Suitable for applications requiring lightweight and compact thermal solutions alongside CCHPs.