- HiK Plates/ Heat Pipe Assemblies
- Heat Pipes 101
- Different Types of Heat Pipes
- Heat Pipe Design Guide
- Pulsating Heat Pipes
- Vapor Chambers
- High Temperature Heat Pipes
High-temperature heat pipes (also known as alkali metal heat pipes) are typically defined as heat pipes that operate between 400 and 1100°C. They are often used to provide precise temperature uniformity or provide high-temperature heat transfer. In these temperature ranges, many traditional heat transport methods and materials are not suitable for practical operations; whereas alkali-metal heat pipes provide robust, high power transport.
Fluid Options for High-Temperature Heat Pipes
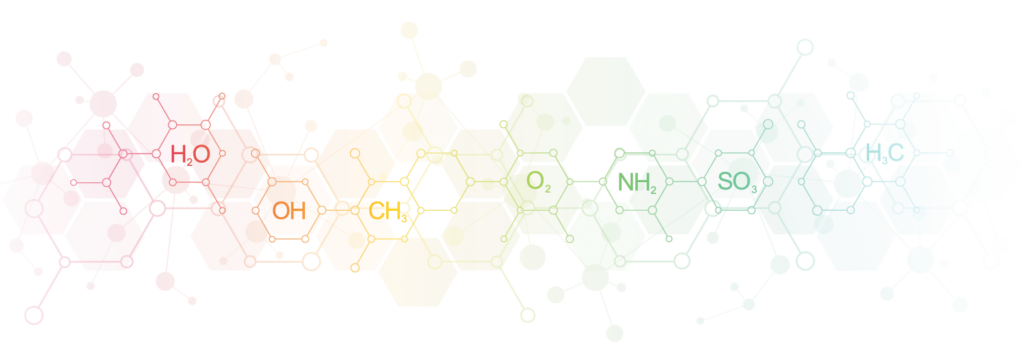
- Potassium 400 to 1000°C (752 to 1,832°F)
- NaK 500 to 800°C (932 to 1472°F)
- Sodium 500 to 1100°C (932 to 2,012°F)
Envelope Material Options for Alkali Heat Pipes
ACT has experience with a variety of traditional and superalloys to withstand the high internal pressure associated with multi-phase metals. Some common envelope materials include Stainless Steel, Inconel Alloy 600, and Haynes. ACT will select the appropriate envelope for the working fluid and operating conditions in partnership with the customer.
Alkali Metal Heat Pipes Examples
Applications for Alkali Metal Heat Pipes
- Temperature Calibration & Control; Isothermalizing furnace elements
- Nuclear Power
- Solar Thermal
- Heat Engine Receivers (Steam, Stirling, Brayton, Rankine)
- Heat Exchangers
- Hypersonic Wing Leading Edges
- Waste Heat Recovery
- Thermoelectric Generators
HOW ARE HIGH-TEMPERATURE HEAT PIPES USED?
High-temperature heat pipes can be used to build custom heat transfer devices for both high power throughput and precise temperature uniformity. Power throughput in the 1 to 100 kW range is typical. Precision heat treating and materials processing furnaces are capable of extraordinarily precise temperature set points and isothermality. Setpoint accuracy, stability, and isothermality of ± 0.1°C is common with a single heated zone, using an off-the-shelf temperature controller.
Because of the inherent temperature uniformity and stability of high temp heat pipes, they are an integral component in nearly all of the most precise temperature calibration instruments in the primary calibration laboratories around the world. This technology can also be applied to research, commercial, and industrial applications for processes such as annealing, sintering, crystal growing, brazing, and controlled diffusion.
Everything You Need To Know About Heat Pipes
ACT CAN MEET YOUR HIGH-TEMPERATURE HEAT PIPE REQUIREMENTS
ACT designs and manufactures cesium, potassium, and sodium heat pipe products for a wide range of high-temperature applications. As a leading provider of thermal management solutions since 2003 with a solid foundation built on research and development. ACT custom engineers high-temperature heat pipe products to meet unique requirements and temperature ranges. As an AS9100:2009-certified manufacturer, you can be sure your high-temperature heat pipe system will meet the highest quality standards in the industry.
Which industries use high-temperature heat pipes?
- Material processing
- Energy
- Temperature calibration and control
Why choose ACT for your high-temperature heat pipes?
The alkali metals used in high-temperature heat pipes are extremely reactive to water or air, so achieving purity and containment is of the utmost importance. The ACT facility is one of the few commercial facilities set up to safely handle the construction of these unique heat pipes. ACT has a dedicated lab space, trusted safety measures, and experienced personnel to make and deliver properly sealed vessels that will safely operate and have a long life.
ACT engineers and technicians are able to draw on the experience gained from the company’s work with NASA on the Kilopower project starting in 2015, to deliver both alkali metal and titanium-water heat pipes to support NASA’s investigation into using small fission reactors for future space transportation and surface power applications.
Furnace Liners and Blackbody Cavities
ACT’s Isothermal Furnace Liners provide Precise and Repeatable Temperature Environments.
In most applications, temperature uniformity is within 0.1°C over the liner length. Energy can be saved and productivity increased because usable reaction zone length in a given furnace becomes larger than the active heater length. Two or more liners may be used in series to create multiple, individually controlled zones for special effects such as step changes in the temperature profile.
Thousands of IFLs are currently in use in many critically controlled processes. Standard IFLs for operation from -60°C to 1,100°C are available in a range of sizes to fit conventional furnace bores for horizontal or vertical applications.
In a Heat Pipe Blackbody Cavity, the annular heat pipe along with the typical hemispherical end cap forms the isothermal blackbody cavity. The temperature uniformity is typically within 0.1°C. See the plot at below for a measured temperature profile of an Ammonia HPBC that has a temperature uniformity of within 0.05°C. Also included is the measured temperature stability of this Ammonia HPBC that is within 0.06°C over a 25-minute period.
Materials of construction are typically Aluminum, Stainless Steel, Monel, Inconel or Haynes, but other materials or coatings are possible. The heat pipe’s inner and outer surfaces are typically oxidized to provide high emissivity. The working fluid used depends on the desired operating temperature range.
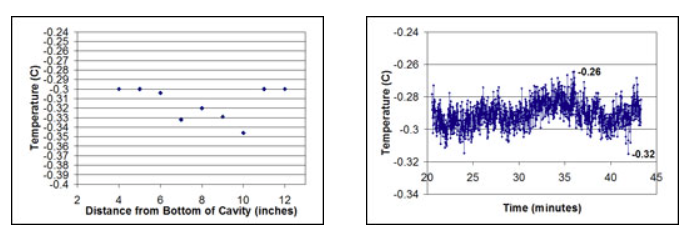
Left Chart: Measured Temperature Uniformity inside Heat Pipe Blackbody Cavity
Right Chart: Measured Temperature Stability inside Heat Pipe Blackbody Cavity
Custom Isothermal Furnace Liner Designs and Options Include:
- Flanged ends
- Extended inner pipe
- IFL with support rods
- IFL with thermo well (external, internal or within the heat pipe)
- Vacuum retort
- Hemispherical dome end
- Small diameter cavity
- Calibration wells
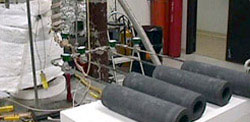
ACT’s product has behaved perfectly, both mechanically and thermally. The fact that I can obtain our specification is a testament to the quality of the product which is still working perfecty after 2-3 years of regular use.
IFL Customer
Ultra High-Temperature IFLs
Inconel 600/601 has been the envelope material of choice since the introduction of high-temperature IFLs nearly 30 years ago. Inconel 600/601 is a widely available high-temperature material, which is compatible with Cesium, Potassium and Sodium and has adequate oxidation resistance and reasonable high-temperature creep strength.
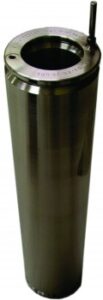
ACT’s Inconel/Sodium IFLs are rated to 1,100°C for up to 1,000 hours of operation (based on creep strength). It should be noted that Inconel is limited to 1000°C. Haynes allows for setpoints up to 100°C beyond that.
Experience gained from operating IFLs in a variety of applications, coupled with a growing desire to operate IFLs for longer than 1,000 hours at 1,100°C, has indicated a need for more robust, longer-life IFLs specifically for use in the range of 1,000 to 1,100°C.
ACT recently introduced a new line of Haynes/Sodium IFLs that can meet this demanding application requirement. The stresses in typical IFLs are in the range of 0.3 to 0.6ksi at 1,100°C (depending on the diameter).
The figure and table below show Haynes 230 has significantly greater creep resistance than Inconel 600/601. While life expectancy is dependent on each application, the data indicates that life expectancy at 982°C based on the table below is 5x or more compared to Inconel 600/601.
ACT’s UHT-IFLs are available in all the standard IFL sizes. Custom sizes are also available upon request.
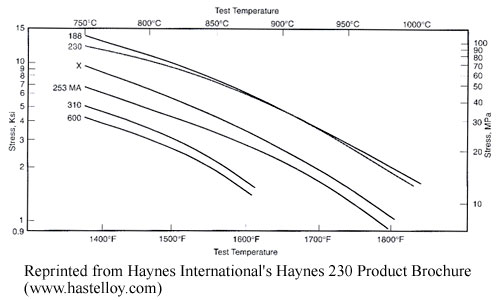
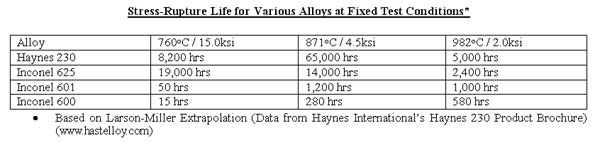
Pressure Controlled Heat Pipe Furnace
A typical PCHP furnace (as illustrated in the sketch below) consists of four major components that can be physically detached from each other:
- Annular heat pipe
- Tube furnace
- Control cabinet with electronics and pressure monitoring system (not shown)
- Computer (not shown)
Unlike a conventional heat pipe that is hermetically sealed, the vapor space of the annular heat pipe in the PCHP furnace is connected to a helium gas reservoir. The control system for the helium pressure consists of a pressure transducer, a helium supply and a vacuum pump. The pressure is maintained constant by admitting or removing helium. A series of pressure transducers and solenoid valves are typically used. The power input to the furnace is controlled by a temperature controller whose set point is coupled to the pressure control system.
Data collection and commands are performed by a computer equipped with special software. Constant helium pressure translates into constant vapor pressure and temperature inside the heat pipe. The precision of the temperature control can be an order of magnitude better than that of the pressure control. Spatial temperature uniformity of better than 10mK has been measured.
Specifications
- Temperature range: 300 – 1,100°C
- Set point stability: ±0.01°C
- Temperature uniformity: ±0.01°C/30 cm
- Orientation: horizontal and vertical
- Heat pipe fluid: Cs, K, Na
- Control gas: helium
Advantages Include:
- Precision temperature control to 1100°C
- High product yield
- Turnkey computer controls
- Programmable temperature history
- Precise materials processing
- Fluid Options for High-Temperature Heat Pipes
- Envelope Material Options for Alkali Heat Pipes
- Alkali Metal Heat Pipes Examples
- HOW ARE HIGH-TEMPERATURE HEAT PIPES USED?
- ACT CAN MEET YOUR HIGH-TEMPERATURE HEAT PIPE REQUIREMENTS
- Furnace Liners and Blackbody Cavities
- Ultra High-Temperature IFLs
- Pressure Controlled Heat Pipe Furnace