- Constant Conductance Heat Pipes
- Variable Conductance Heat Pipes
- Space Copper-Water Heat Pipes
- Loop Heat Pipes
- Space VPX
- Liquid Cooling
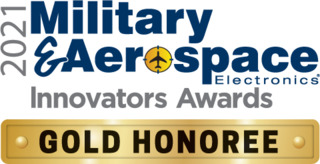
Satellites traditionally have been used for performing data collection, transmitting, and receiving roles, leaving the data processing/computing to ground stations. As the data volume continues to increase, in-situ computing is increasingly required to minimize latency and maximize reaction speed. However, adding computing onboard satellites creates new thermal management challenges.
Copper-water heat pipes are often used for electronics cooling on Earth and offer excellent performance for short-distance, high heat flux heat transport, but they had limited flight heritage in space. Copper-water heat pipes operate in a slightly higher temperature range than aluminum-ammonia heat pipes or CCHPs; which makes them ideal for operation closer to the electronics in the satellite thermal network. The water working fluid combined with a sintered wick structure allows them to handle the higher heat fluxes from for example ASIC or FPGA used for on-orbit computing or Digital Signal Processing (DSP) that are often too high to be handled by conventional ammonia CCHPs. Additionally, water is non-toxic, which combined with the sintered wick is a benefit for ground testing and shipping concerns. In summary, copper-water heat pipes can transport more power, delivered at much higher power densities, and at higher temperatures than aluminum-ammonia heat pipes traditionally used for satellite thermal control.
Technical Benefits and Performance Capabilities of Space Copper-Water Heat Pipes
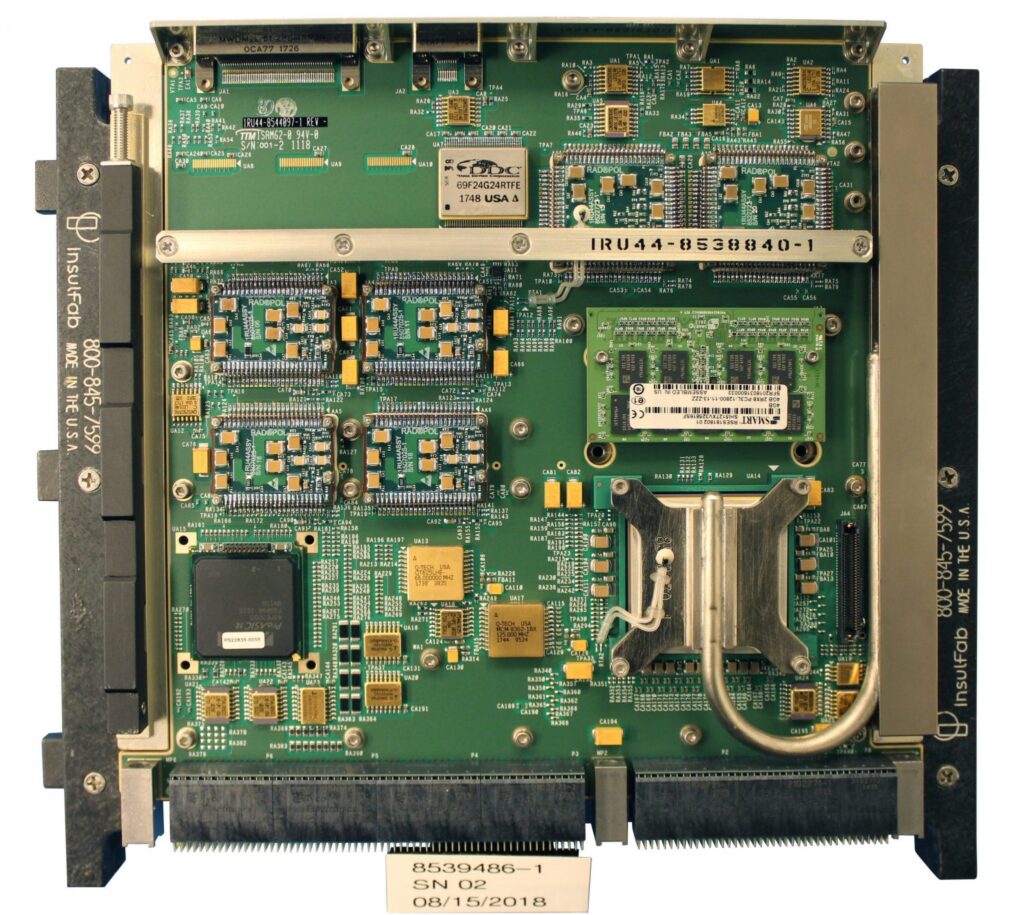
The demonstrated performance of space copper-water heat pipes (SCWHP) is uncompromised from that found in terrestrial copper-water heat pipes. The primary thermal characteristics and benefits include:
- High Heat Flux Capability:
Up to 50 W/cm2 - Low-Temperature Gradient:
2-5°C ∆T with typical heat loads - Wicking Capability:
Up to 10” against gravity - Geometry / Routing:
3x OD Bend Radius
While the thermal performance (heat transport with a low-temperature gradient) is the primary reason SCWHPs are chosen for space avionics, the wicking and routing capabilities offer significant benefits to integrators. The wicking is important for ground testing at any orientation and cannot be achieved with any other working fluid for a typical electronics operating temperature range. The geometry and routing are also critically important for point-to-point heat transport to reduce the heat transport distance and to accommodate for any orientation difficulties of the source and sink.
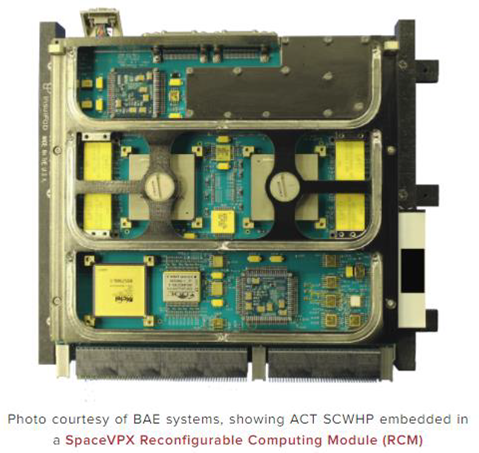
So, What’s Different?
The two primary differences between SCWHPs and terrestrial copper-water heat pipes are the manufacturing protocols required to produce critical spaceflight hardware and the qualification testing required to validate that the design will survive the harsh operating environment.
In any environment, management of the fluid inventory and a rugged, robust heat pipe design are key to maintaining long-term operation. In the space environment, it is especially important there is only enough working fluid (water) in the heat pipe to saturate the wick; any excess fluid will create a puddle (droplet or large meniscus) in the pipe. When a puddle exists, it can bridge the inside diameter of the heat pipe and expand outward upon freezing, potentially resulting in mechanical deformation. The mechanical deformation will continue to occur with each freeze/thaw cycle. Damage is cumulative and will eventually result in the rupture of the heat pipe wall. Therefore, it is critical that SCWHPs, at most, have a fully saturated wick – but no excess resulting in a puddle.
ACT has developed a manufacturing approach that reliably produces high-quality and flight-ready SCWHPs; providing state-of-the-art technology for cooling electronics on-board spacecraft. This process includes a variety of manufacturing innovations and routine inspections to assure proper quality is maintained. After three (3) generations of manufacturing process improvements, ACT has developed the GEN III process that has yielded many rounds of flight-qualified hardware. Flight qualification requires a significant amount of testing, as detailed in the “Testing Considerations” section below. While cycle counts and processes may vary based on the mission, all flight SCWHPs delivered to our customers have passed a series of rigorous tests.
Space Heritage and Adoption
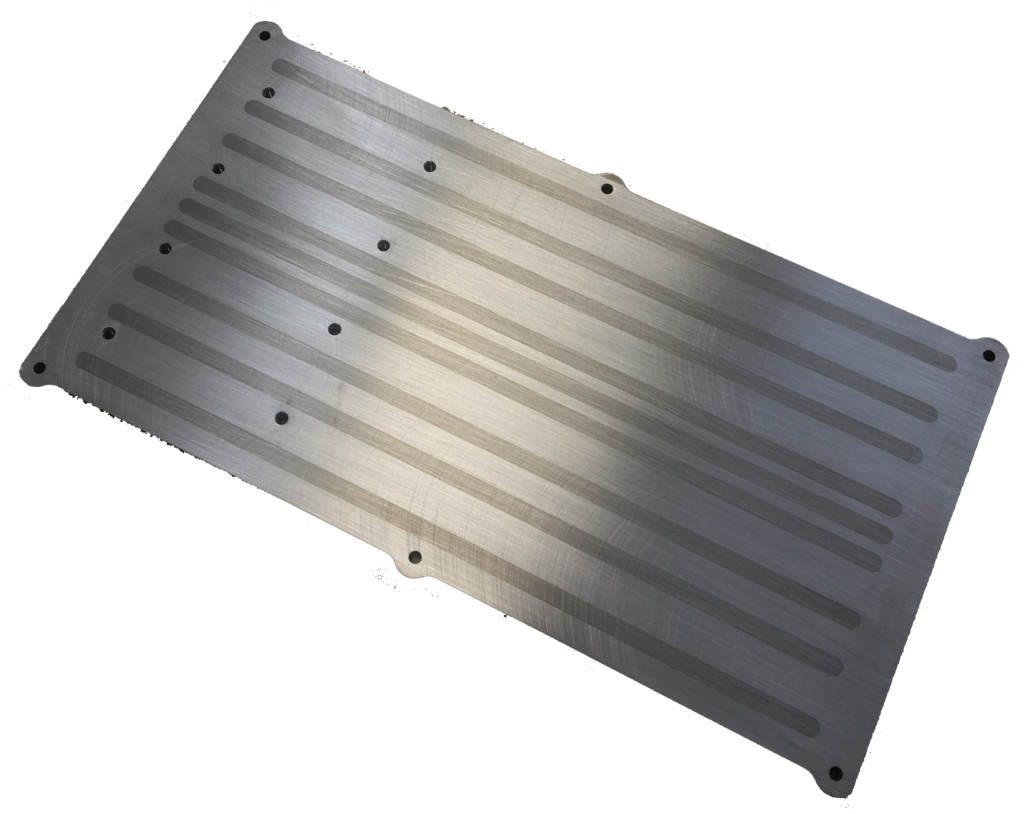
ACT flew its first SCWHPs in 2017 together with NASA Marshall Space Flight Center and NASA Johnson Space Center, under the Advanced Passive Thermal experiment (APTx) project. The SCWHPs were embedded in aluminum HiKTM plates for validation testing on the International Space Station (ISS). The objective of testing the hardware on the ISS was to demonstrate the operation and flight worthiness of the SCWHP-embedded HiK™ plate. The program was successful and provided SCWHPs with TRL 8. Since then, SCWHPs have been delivered for multiple spaceflight missions. ACT continues to work with numerous industry leaders and has delivered hundreds of SCWHPs that have passed severe qualification and acceptance testing protocols.
Testing Considerations
On-orbit, freeze/thaw events can occur in three primary modes of operation as follows: unpowered freeze/thaw, frozen start-up (cold start), and powered freeze/thaw. SCWHPs must be carefully designed and verified to ensure the design is tolerant of these types of freeze/thaw cycles. One means to increase design tolerance during freeze/thaw is to oversize the heat pipe and starve the wick of fluid inventory reducing the amount of water available to form a puddle.
Careful selection of heat pipe geometry, wick structure, and fluid charge is necessary to assure a freeze-tolerant SCWHP solution. The Venn diagram shown in Figure 1 shows the representative region of acceptable fluid charge required to simultaneously meet thermal performance requirements and achieve freeze/thaw cycling tolerance. The area of overlap between these regions results in a heat pipe that meets both thermal performance and freeze/thaw requirements and can be influenced by the diameter of the heat pipe selected.
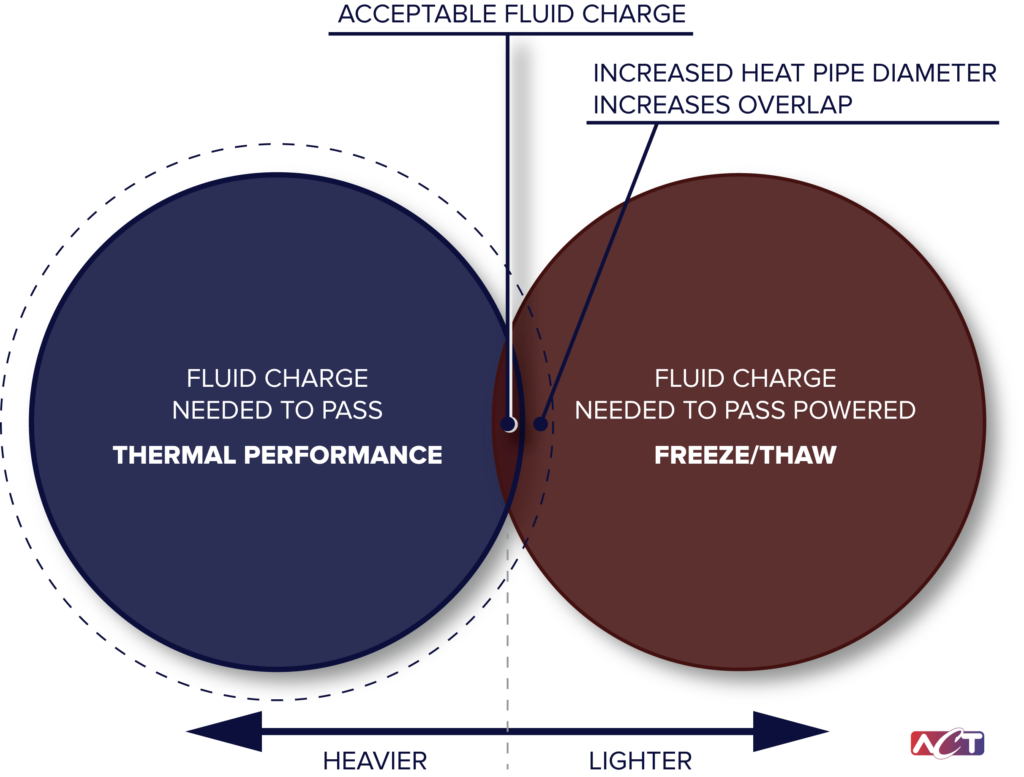
Unpowered Freeze/Thaw
After launch before powering up the satellite or when a satellite is in standby mode, it is possible for the heat pipes to experience freezing and thawing when the heat pipe is not operating as a two-phase heat transfer device. In this case, the pipe is at thermal equilibrium and is isothermal as it freezes and thaws. The wick structure within the SCWHP has a high yield limit, which means it has the ability to deform significantly and elastically recover. As the water freezes, it expands and grows toward the inside diameter of the heat pipe. As it thaws, the water turns to liquid and the wick returns to its original state.
Frozen Start-up (Cold Start)
This mode is often referred to as frozen start-up or cold start freeze/thaw. In this case, the heat pipe freezes as described above in unpowered freeze-thaw. The heat pipe dwells at a low temperature until it is isothermal and all of the fluid inventory is frozen within the wick structure. However, at the beginning of the thaw cycle, power is applied to the evaporator. The evaporator temperature begins to quickly rise as the heat must conduct down the wall of the heat pipe envelope to begin thawing the frozen water. The water in or nearest to the evaporator thaws first, evaporates and travels towards the condenser. As the vapor condenses, it releases the latent heat of vaporization to the frozen adiabatic and condenser sections of the heat pipe resulting in an indeterminate state of heat pipe operation. The actual response of the heat pipe during the thawing is highly dependent on the thermal masses and secondary conduction paths to which the heat pipe is connected. Prediction of actual response is nearly impossible to model and must be determined experimentally with the frozen start-up test.
The test is run to determine whether or not the heat pipe, during the thawing transient condition, will be able to thaw to the extent necessary to startup and recover before the electronics reach their maximum allowable temperature. Alternatively, the evaporator may “dryout” to an unrecoverable state, causing the heat pipe to operate with an excessive temperature gradient that may allow the electronics to exceed their maximum allowable temperature. This testing is highly dependent on the heat pipe’s geometry, the lengths of the evaporator, adiabatic, and condenser sections, the power applied, and the mass of the electronics and heatsinks attached to the heat pipe. The frozen start-up can be a real operational condition on the satellite and the testing should be performed in a manner that most closely represents the actual system (sink and source thermal mass and secondary conduction paths) to verify that the heat pipe can restart under the expected conditions. Repeated testing cycles also prove out whether frozen start-up freeze/thaw cycles will damage the heat pipe.
Powered Freeze/Thaw
During powered freeze/thaw, power is continuously applied to the evaporator while the condenser temperature is forced to vary from maximum to minimum expected temperature extremes and typically include dwells at high and low extremes. This is considered one of the most challenging freeze/thaw tests for SCWHPs because the test, by definition, evaporates water from the evaporator section and transports it to the condenser section while forcing the condenser into a below 0°C condition. This results in a dried-out evaporator section and the potential for working fluid to collect in the condenser section. Should a puddle or meniscus of working fluid occur that spans the diameter of the heat pipe before the working fluid freezes, the resulting expansion of the ice has the potential to damage the heat pipe envelope. Additional cycles have the potential to accumulate damage to the point of failure as can be seen if a heat pipe with excessive fluid charge is freeze/thaw tested.
Many considerations must be taken into account to develop a SCWHP design that will survive freeze/thaw testing. The largest contributor being the balance of fluid charge to thermal performance discussed earlier, but also geometric considerations such as evaporator length, condenser length, overall length, wick design, and heat pipe diameter. Freeze/thaw cycling can cause damage to accumulate; therefore, it is critical that all acceptance and qualification test programs be developed to test the SCWHPs as they will fly to ensure the hardware will survive for its intended life.
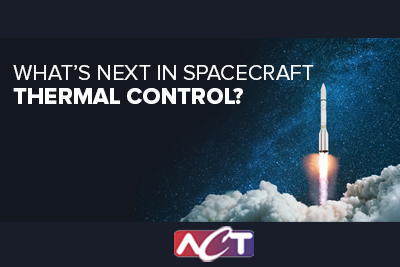