Phase Change Based Solutions
ACT is a leading provider of high performance, system critical PCM heat sinks and heat exchangers. PCM is an ideal solution to store energy for single use or low duty-cycle transient applications. PCMs have high latent heat of fusion, allowing them to store a lot of energy with low temperature rise. This can lead to simplistic thermal management when designed and integrated properly.
Introduction to Phase Change Material Heat Sinks
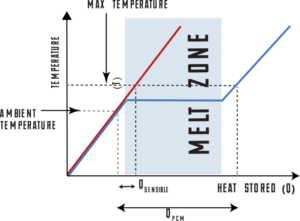
PCM Heat Sinks can absorb thermal energy (heat) with minimal temperature rise during the solid-to-liquid phase transition. During this phase transition, the latent heat (J/kg) is at least one (1) to two (2) orders of magnitude higher than the sensible energy that can be stored by the specific heat of a material in its solid or liquid phase. Figure 1 illustrates this phenomenon by plotting the temperature rise of a PCM over time with steady-state energy input. In practice, PCM is contained in a hermetically sealed enclosure and used to maintain the temperatures of critical heat-generating components over a given period of time.
Applications
- Single Use: Missiles
- Duty Cycle: Directed Energy, LEO Satellites, Pulsed Electronics, Aircraft electronics or photonics used for takeoff/landing
- Protection Against Failure: Use PCM to store energy while your system safely shuts down to protect against pump or fan failure.
Benefits
- Mass, weight, and packaging: Size downstream cooling for average instead of peak heat load
- Proven: Fielded in some of the most demanding harsh environment applications
- Simplicity: While there are numerous design and manufacturing considerations, properly designed PCM modules are inherently simple and low risk.
Phase Change Material Heat Sinks
PCM Heatsinks are typically stand-alone devices typically mechanically coupled to the heat source, allowing heat to directly conduct into the PCM. For single use applications, that is often the only connection point, while transient duty-cycled applications may also couple to the ultimate heat sink. PCM can have flexible geometry, especially if 3D printing is an acceptable manufacturing approach for a given application. Internally, PCM heatsinks have enhanced conduction paths, designed specifically for the given source locations to properly melt the wax and not overheat due to the PCM’s low thermal conductivity.
Phase Change Material Heat Exchangers
PCM Heat Exchangers are often integrated into other thermal control loops. For instance, many are integrated with single and two-phase liquid loops. In these types of applications, the primary liquid cooling solution takes heat from duty-cycled electronics and exchanges heat with a secondary loop that ultimately transports and rejects the heat. The PCM is integrated into a compact packaged heat exchanger to dampen the pulse load between the primary and secondary loop so that the secondary loop can be sized for average power. For very high power applications (i.e. 30+ kW directed energy systems), the mass and volume saving can be extreme.
Phase Change Material Design Considerations
The challenge when designing with PCM, is the inherent poor thermal conductivity of the material itself. For example, paraffin waxes typically have thermal conductivities of less than 1 W/m-K. This is remedied by adding internal features to increase the overall effective thermal conductivity of the enclosure. ACT is experienced with fins, heat pipes and metal foams as options for these internal structures.
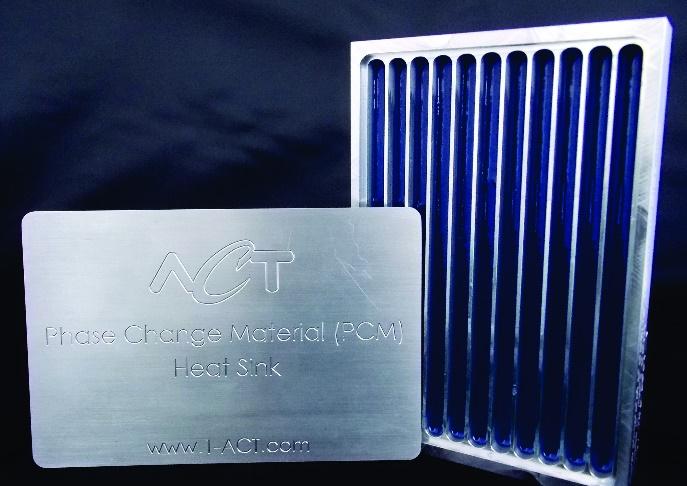
Phase Change Material (PCM) Heat Sink Sample
ACT has expertise in analyzing PCM systems and accurately predicting transient responses. In-house analytical tools in combination with computational fluid dynamics (CFD) software are leveraged for thermal simulations involving PCM.
In most cases, a dynamic specific heat is created to capture effects during multiple stages.
ACT has also developed a PCM heat sink calculator that provides a temperature profile as a function of time for up to three Phase Change Materials. It also estimates the mass and volume and volume for the PCM heat sink.
*Note that this calculator assumes a general fin thickness. ACT develops custom solutions with the optimal fin thickness for each application’s unique requirements.
Manufacturing of Phase Change Material Heat Sinks
Since 2015, ACT has been designing and manufacturing PCM solutions for some customers from the most high-profile defense suppliers to innovative high-profile disrupters in the commercial sector (customers and project details confidential). Our depth of experience in not only the design but also the manufacturing of custom PCM Heat Sink solutions positions us to be your trusted partner of choice for PCM Heat Sinks.
ACT has developed the necessary manufacturing technologies required to produce high-quality, high-reliability PCM heat sinks. Some of these manufacturing technologies include:
- PCM project evaluation and thermal design
- PCM heat sink prototyping and production
- Aluminum vacuum brazing
- Precision charging of PCM
- Safe and reliable sealing of the PCM assembly
- Pressure, leak, and thermal testing
- Cycling and Calibration of PCM
- Integrated multi-technology PCM
- Thermal Chambers, Qualification and Acceptance Testing