- Heat Pipe Learning Center
- Pumped Two-Phase Learning Center
- PCM Learning Center
- HVAC Learning Center
- Videos
- eBooks
- Brochures
- Case Studies
- Webinars
PCM Learning Center
Phase Change Materials (PCMs) are a passive, two-phase, thermal storage technology that utilize the latent heat of fusion to absorb thermal energy. Since energy stored by the latent heat from melting or freezing is at least 1-2 orders of magnitude higher than that by the specific heat, a PCM heat sink is a highly effective thermal management device.
While common PCMs such as paraffin waxes have a high thermal capacity due to the latent heat, they also tend to have a low thermal conductivity, often < 1 W/m-K. This causes a need for additional features, such as extended surfaces and fins to effectively melt the entire PCM with minimal thermal resistance. PCM heat sink and heat exchanger designs are therefore critical in ensuring the optimal SWaP minded solution for the higher-level assembly.
Resources for Phase Change Material Thermal Solutions
Two Main Reasons to Choose a PCM based Thermal Solution | Typical Applications that benefit from leveraging PCM thermal Solutions include: |
1. Smoothing out the thermal energy during pulsed or cyclic operation allowing the heat removal system to be designed for the average heat load rather than the peak load. 2. Short-Term Thermal Storage where a suitable heat sink is not available, which can provide protection from failure during coolant operations | Directed Energy Weapons Pulsed Electronics Missiles Battery Cooling HVAC (Heating, Ventilating, & Air Conditioning) Spacecraft Thermal Control Air Cooled Condensers for Power Plants |
Advanced Thermal Management using PCM
ACT engineers have experience in designing PCM-based thermal management systems, ranging from milli-watts to kilo-watts.
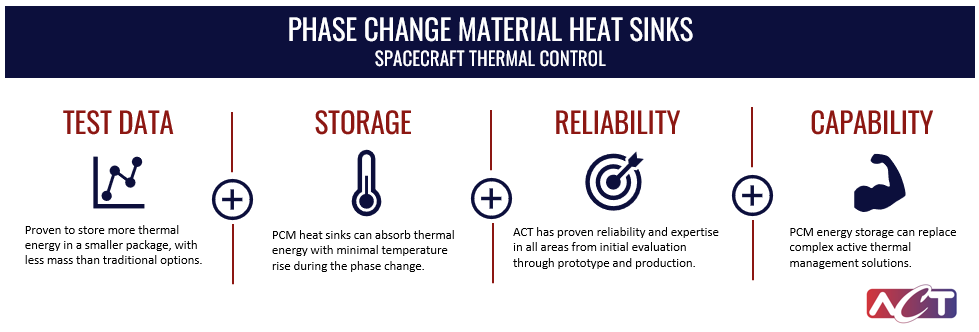
PCM Assemblies for heat storage use a variety of PCMs and wall materials to meet application-specific requirements. Our modeling and manufacturing experience includes paraffin waxes, hydrated salts, and metal-based PCM assemblies for powers ranging from 1 to 100 KW. Due to the dynamic, time-dependent thermal properties of a PCM heat exchanger, advanced modeling capabilities and experience in thermal design are essential to a well-designed system.
ACT Modeling Capabilities & Software packages for PCM Assemblies: | Types of complex PCM packaging in which ACT is experienced: |
In-House Design and Analysis Software Thermal Desktop Autodesk Simulation CFD Differential Scanning Calorimetry (DSC) | VAB (Vacuum Aluminum Brazed) Corrugated surfaces Fins (Folded, Integral, Bonded, etc.) Heat pipe-embedded enclosures Heat Exchangers Additive Manufactured |
PCM Resource Links
Webinars
Videos
R&D Advancements
COMMON QUESTIONS ON PCM HEAT SINK DESIGN
While some answers are specific to your needs and system requirements, these responses to standard questions will give you a better understanding as to how these devices operate.
ACT has developed a PCM heat sink calculator that provides approximate volume, weight, and temperature profile as a function of time for temperatures ranging from -10°C to 85°C.
The Calculator only uses organic PCMs. Please contact ACT if you have an application using hydrated salt or metallic PCMs, or one that is outside of this temperature range.
The operating temperature range depends on the application. Many paraffins are appropriate for electronics applications where the temperature is typically maintained below 100°C; see Table 1 below ( In WHEN SHOULD I USE PARAFFIN WAX, HYDRATED SALTS, OR METALLIC PHASE CHANGE MATERIALS?). For higher temperature applications, such as energy storage for power plants, salts and metals can be used.
The storage temperature of a PCM heat sink will depend on the type of PCM selected. Most PCM heat sinks can be stored at any temperature below its maximum operating temperature. Because most PCMs become less dense, expanding, as their temperature increases, PCM heat sinks are filled in an environment above their maximum operating point. If the heat sink were heated beyond its fill temperature it could become over pressurized and deform or open up a leak path. If a PCM heat sink is designed to keep a source below 90°C, it should not be stored in an environment above 90°C. (Note that in this case, 90°C is the maximum allowable design temperature; it is always above the melting point of the PCM).
A PCM heat sink will operate in any orientation, however, in applications that require tight temperature control, the orientation should be considered to minimize temperature variations.
The PCM heat sink size will be limited by the ability to effectively move the heat into the PCM. If the volume of PCM required is large and/or the heat flux is very large, the manufacturability of the internal fin structure will restrict the PCM heat sink size and storage capabilities. In certain cases heat pipes can be used to spread the heat to multiple PCM modules.
In most cases fins are used to overcome the low thermal conductivity of PCM. Their increased surface area and high conductivity allows the heat to penetrate the PCM, resulting in an even melt front and lower temperature gradient within the PCM. Heat pipes can also be used with or without fins to better distribute heat to the PCM in high heat flux applications.
A variety of materials can be used for the envelope and fins. Aluminum is the most common material used for PCM heat sinks, but ACT has also worked with copper, steel, and magnesium.
There are several factors that need to be considered when selecting a phase change material. An ideal PCM will have high heat of fusion, high thermal conductivity, high specific heat and density, long-term reliability during repeated cycling, and dependable freezing behavior. As shown in Table 1 below, PCM options include paraffin wax, non-paraffin organics, hydrated salts, and metals; green text indicates attractive features of these PCM types, while red indicates challenges. You can also reference our PCM Heat Sink Calculator to find the right material for your application.
- Paraffin wax is ideal for most electronics applications
- There is a large selection of pure hydrocarbon materials and paraffin blends available, with melting temperatures every few degrees, ranging from roughly -20 to 100°C.
- They have a high heat of fusion per unit weight, provide dependable cycling, are non-corrosive, and are chemically inert. meaning they are chemically compatible with most metals.
- Typical Paraffin Wax PCMs used in Electronics Applications
Examples of Paraffins C36H74 C32H66 C30H62 Densitysolid (kg/m3) 857 809 810 Latent Heat (kJ/kg) 223 261 249 Tmelt (°C) 72 to 76 66 to 70 59 to 66 Temperature ranges of 72-76°C, 66-70°C and 59-66°C are good to ensure safe operation of many electronic devices. Many other PCM choices are also available, with melting points differing by a few degrees from -9°C to 90°C.
-
Key design considerations according to our in-house PCM experts when designing with paraffin PCM
- Void management is important due to the volume change from solid to liquid.
- Designing sufficient conduction paths is critical as paraffin PCM’s have a low thermal conductivity
- Hydrated salts are generally used for larger energy storage applications since they are much cheaper
- They have a high heat of fusion per unit weight and volume, have a relatively high thermal conductivity for non-metals, and show small volume changes between solid and liquid phases.
- These are not commonly used for electronics heat sinks, since they are corrosive and long-term reliability (thousands of cycles) is uncertain. The most common application is for very large thermal storage applications (e.g., solar heating), where much lower cost is very attractive.
- Key design note: using hydrated salts must account for both corrosion and the limited number of cycles available.
- Metallic PCMs are generally used for high-temperature applications
- They are generally used where no suitable paraffin wax is available, due to the high temperatures.
- Other PCM materials such as non-paraffin organics, and liquid-to-gas phase change materials are available but are not often used for electronics heat sinks.
Table 1. Properties of Typical Phase Change Materials
PROPERTY OR CHARACTERISTIC |
Paraffin Wax | Non-Paraffin Organics | Hydrated Salts | Metallics |
HEAT OF FUSION |
High | High | High | Med |
THERMAL CONDUCTIVITY |
Very Low | Low | High | Very High |
MELT TEMPERATURE (°C) |
-20 to 100+ | 5 to 120+ | 0 to 100+ | 150 to 800+ |
LATENT HEAT (KJ/KG) |
200 to 280 | 90 to 250 | 60 to 300 | 25 to 100 |
CORROSIVE |
Non-Corrosive | Mildly Corrosive | Corrosive | Varies |
ECONOMICS |
$$ | $$$ to $$$$ | $ | $$ to $$$ |
THERMAL CYCLING |
Stable | Elevated Temperature Can Cause Decomposition | Unstable over Repeated Cycles | Stable |
WEIGHT |
Medium | Medium | Light | Heavy |
Differential Scanning Calorimetry (DSC) is a thermoanalytical instrument in which the difference for heat required to increase temperatures of a sample and a reference is measured as a function of temperature, which is usually programmed to change linearly as a function of time. It is frequently used to measure the latent heat of Phase Change Materials (PCM). In operation, an empty pair of aluminum or copper pan and lid is used as the reference and the sample is placed in another pair of pan and lid with the same material and weight as the reference. The result of a DSC experiment is a curve of heat flux versus temperature or time, and the integration of phase transition peak area on the curve indicates the latent heat of the sample. ACT owns and operates a DSC-600 with the following specifications.
Specifications | Capabilities |
|
|