QUALITY CONTROL FOR SPACE PRODUCTS
In the Space market, understanding that thermal management, weight, size, and structural integrity are all critical aspects of system performance is paramount in providing solutions that meet program requirements and function properly in harsh environments seen in space. ACT’s aerospace products are designed and manufactured under strict AS9100:D certified quality systems and stringent manufacturing and quality control processes.
Our aerospace products group offers high-performance heat pipe and loop heat pipe products, thermal storage, and spacecraft accumulators for pumped systems, as well as providing Cold Plates for Thermal Vacuum Testing (TVAC) and Space-qualified titanium struts.
EXAMPLES OF THE STEPS IN ACT’S SPACE PRODUCTS QUALITY PROCESSES INCLUDE:
- Aerospace (AWS D17.1) certified welders
- In-house X-ray
- Extensive extrusion options optimized for performance, weight and mounting considerations
- In-house machining
- Material certification
- Multi-stage cleaning process with bath monitoring
- Working fluid triple distillation and processing
- Helium mass spectrometry leak detection
- Proof and burst pressure verification
- Accelerated aging and thermal cycling
ACT’s Space Flight Heritage Timeline
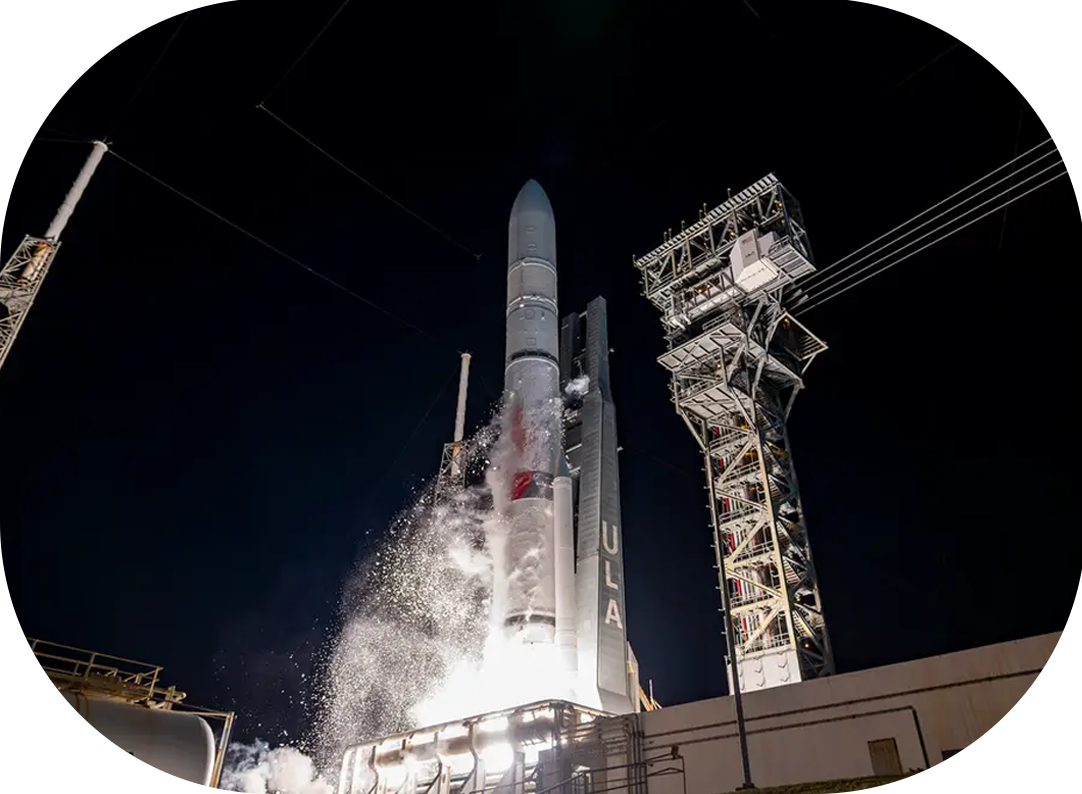
January 2024
ACT thermal management space flight hardware on-board Peregrine
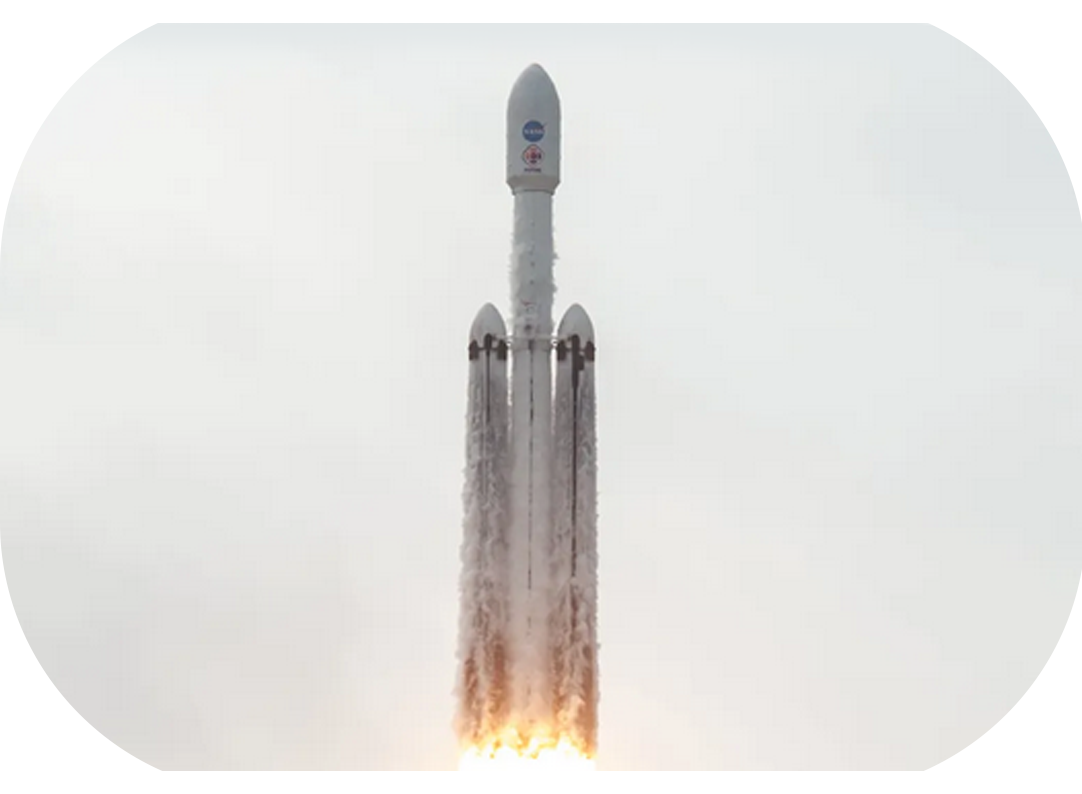
October 2023
ACT thermal management space flight hardware on-board Psyche
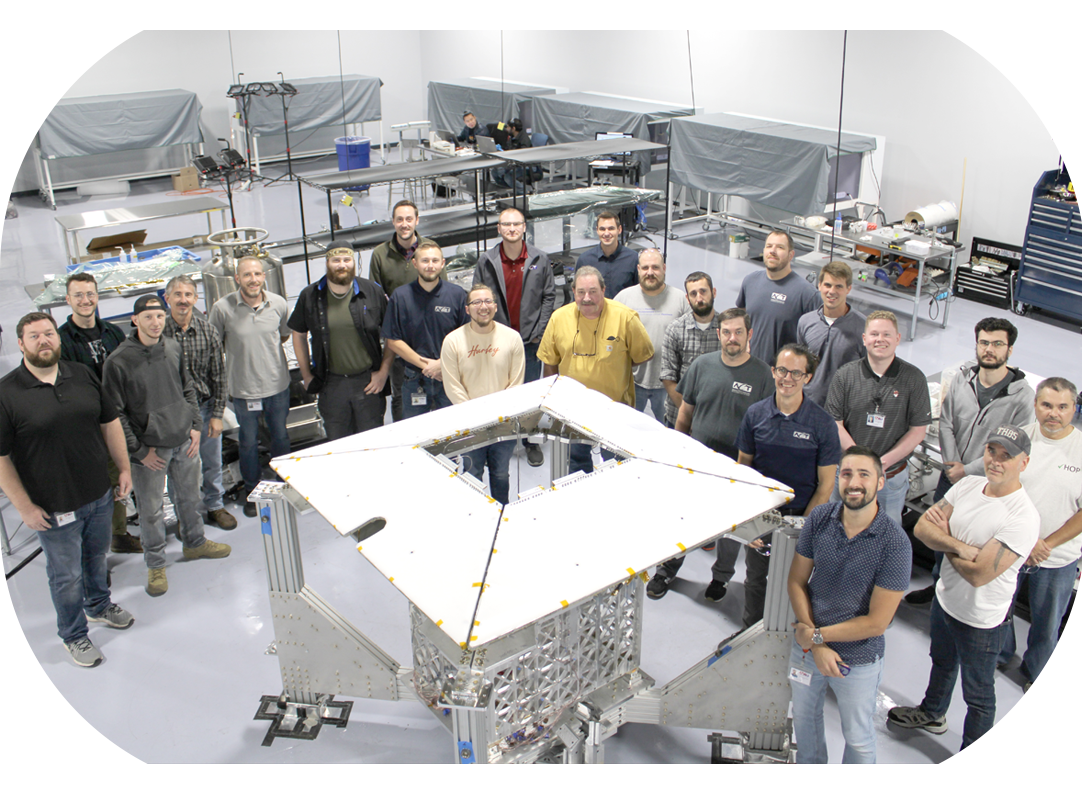
October 2023
ACT ships VIPER lunar rover hardware
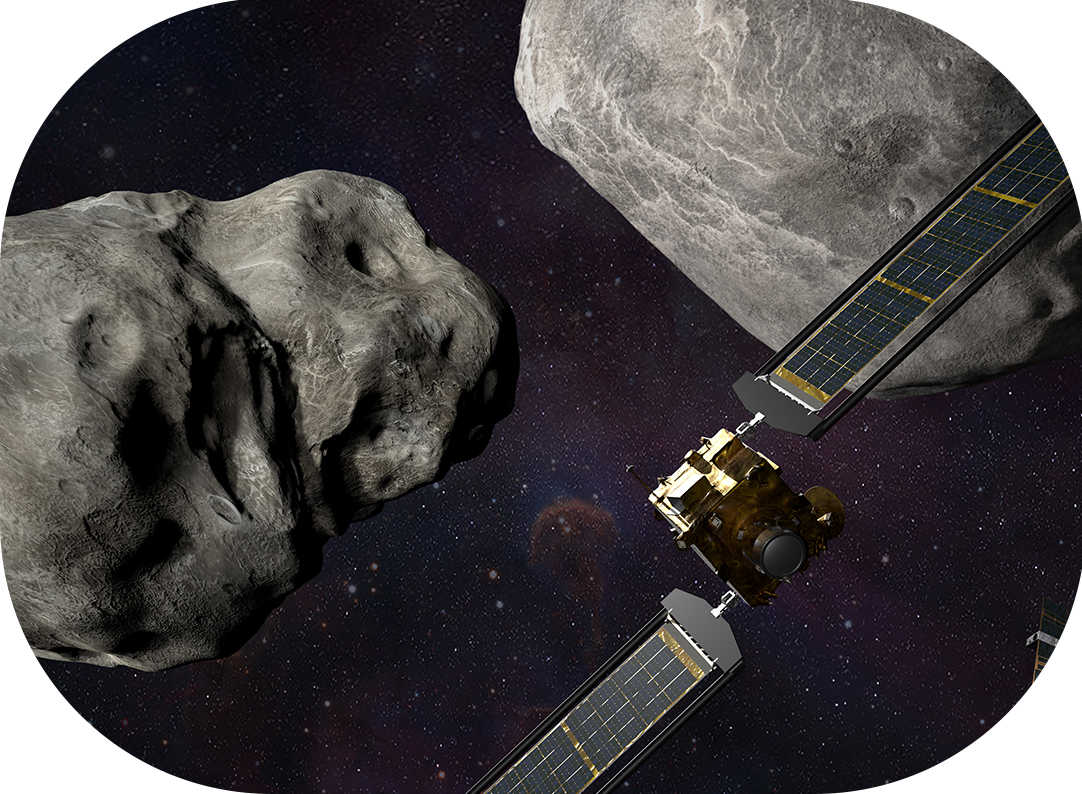
November 2021
ACT supplies flight hardware in support of the Double Asteroid Redirection Test (DART) mission.
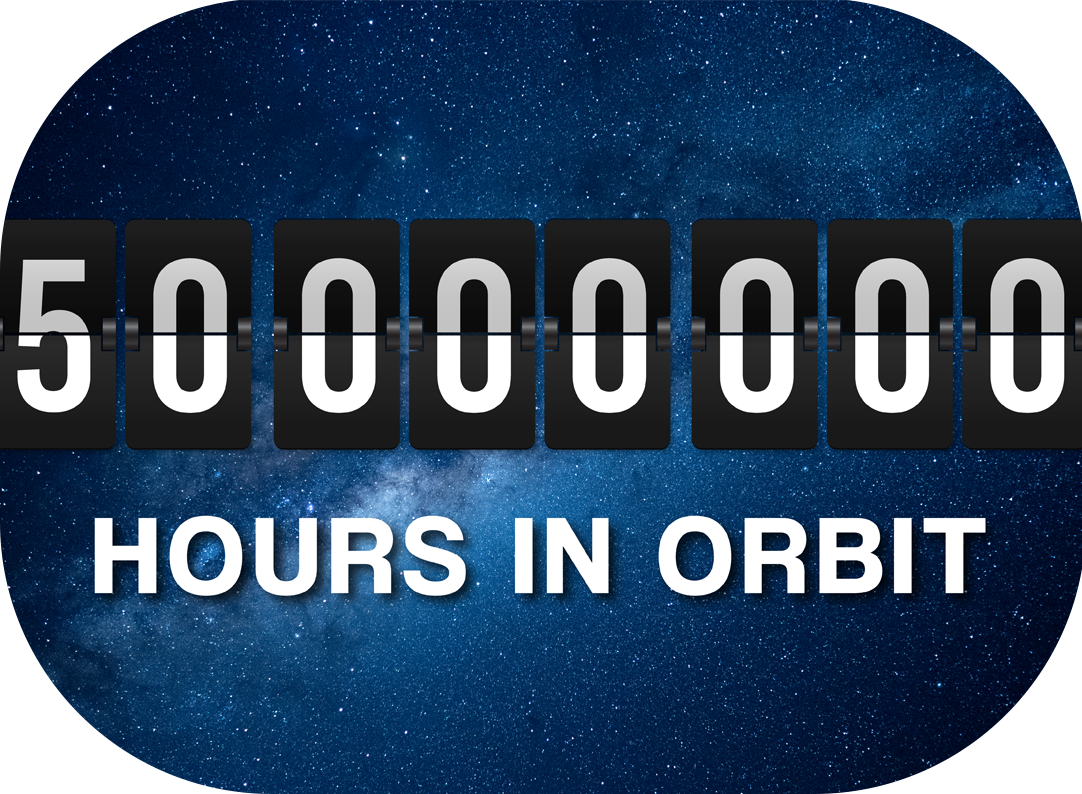
January 2021
ACT’s CCHPs reach 50 million hours on-orbit milestone
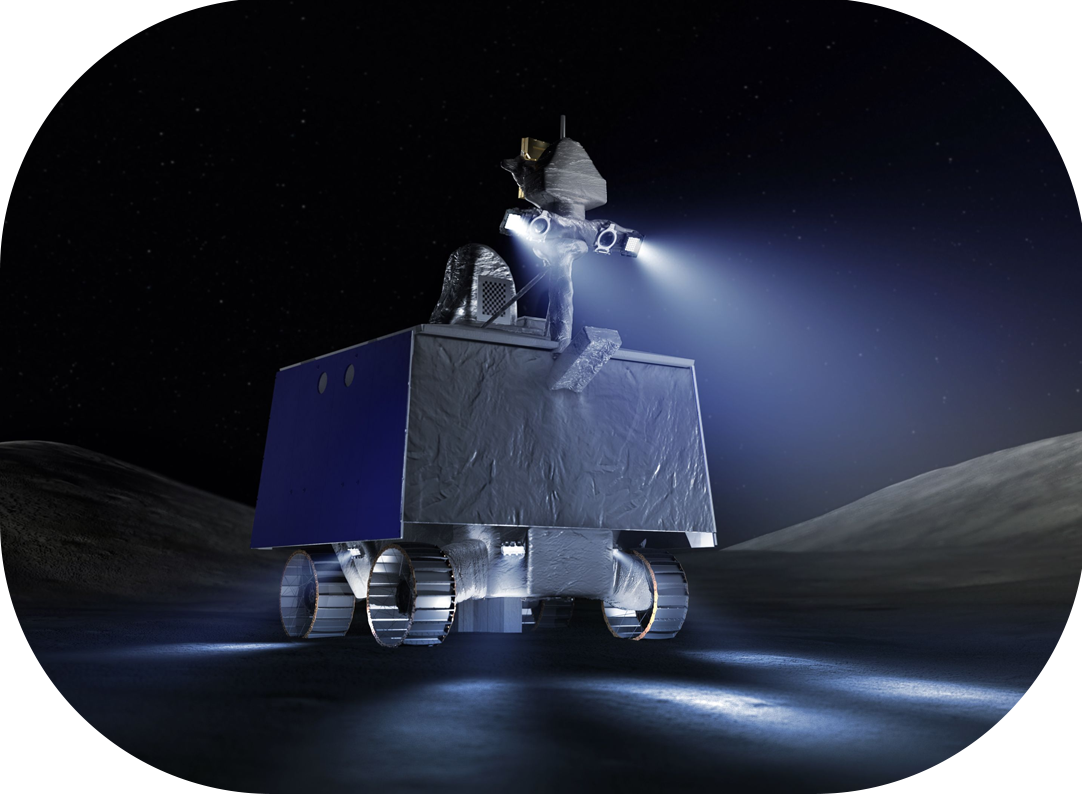
December 2019
ACT receives a Phase II STTR contract from NASA to develop Advanced hot reservoir variable conductance heat pipes (VCHPs) for planetary landers
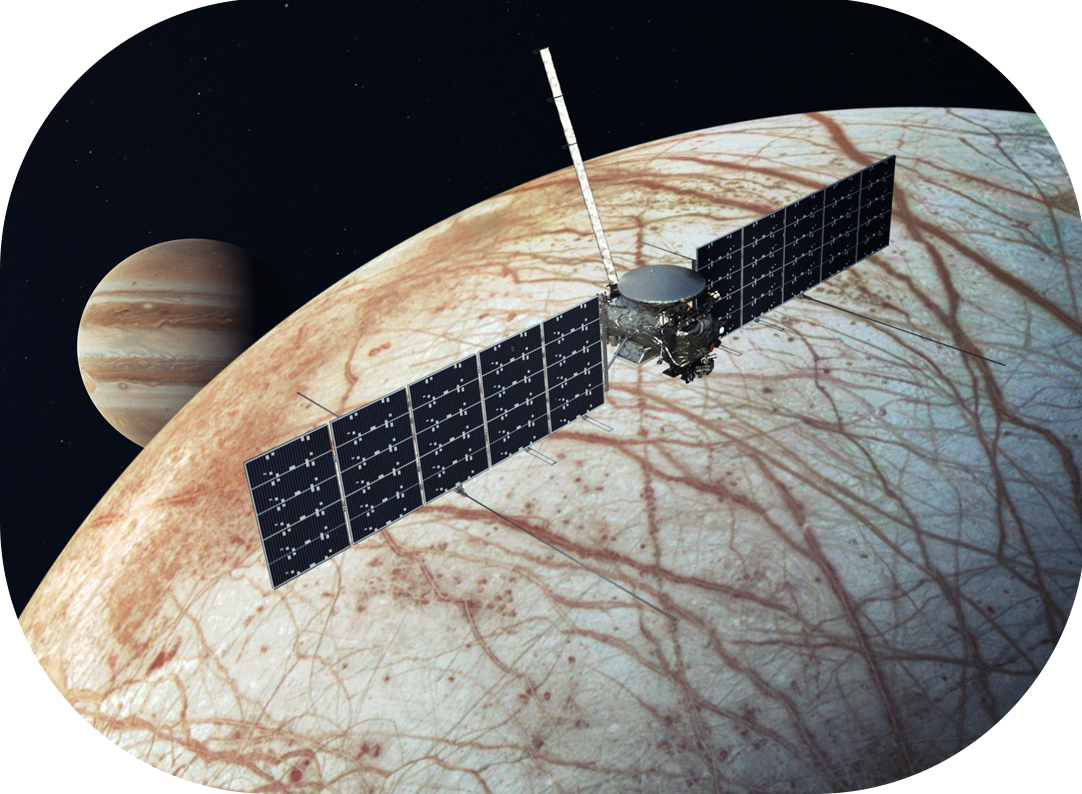
July 2019
ACT supplies flight hardware for heat redistrubution system, a single-phase pumped fluid loop, in support of Europa Clipper Mission
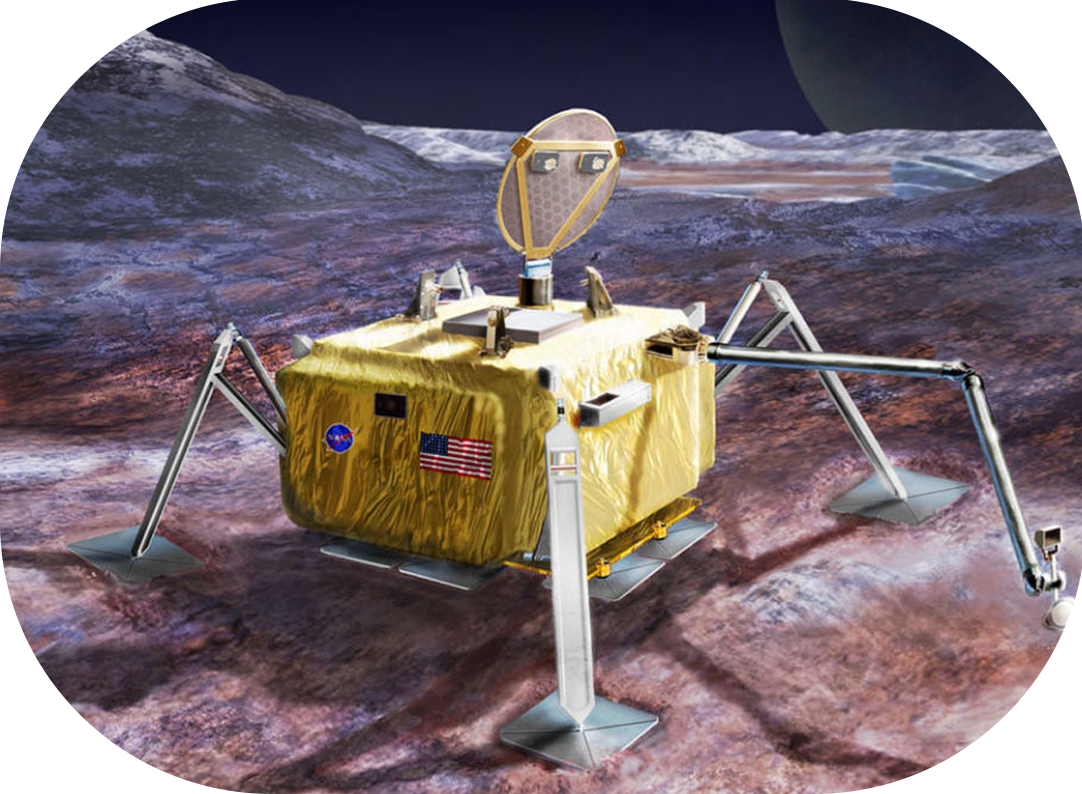
June 2019
ACT receives a Phase I R&D contract from NASA to develop a variable conductance cold plate for spatial and temporal temperature uniformity
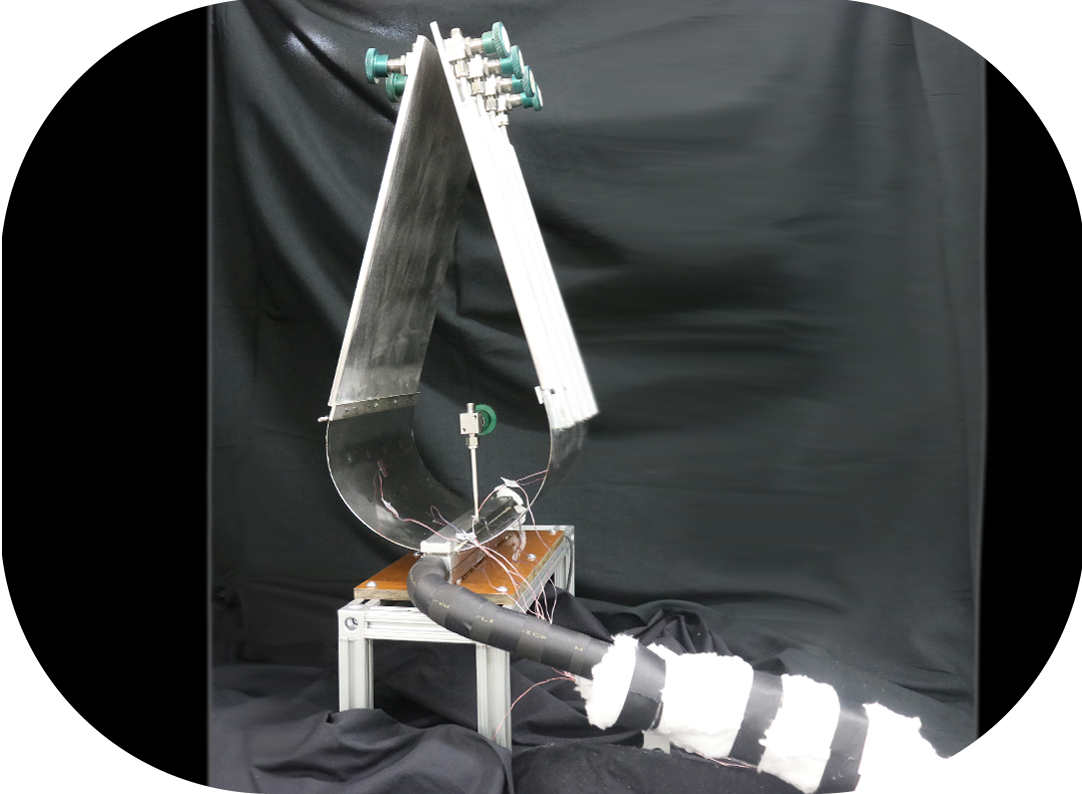
May 2019
ACT receives a Phase II R&D contract from NASA to develop a fully passive variable-view-factor radiator panel
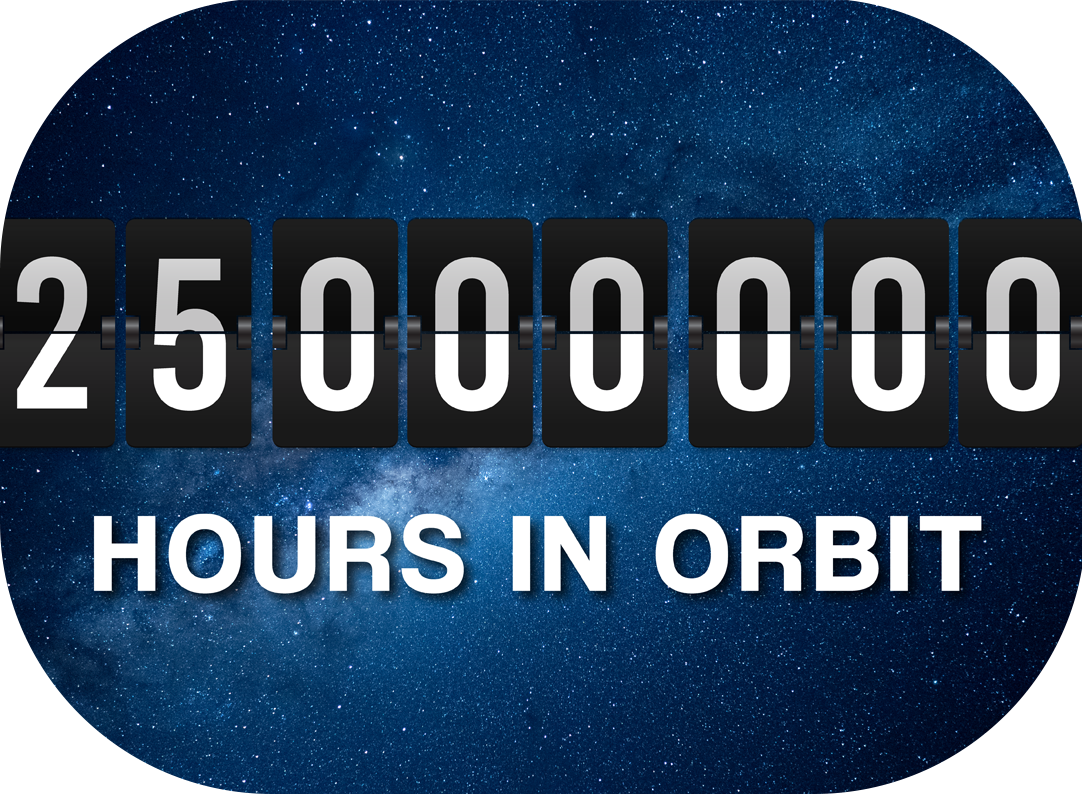
June 2018
ACT’s CCHPs reach 25 million hours on-orbit milestone
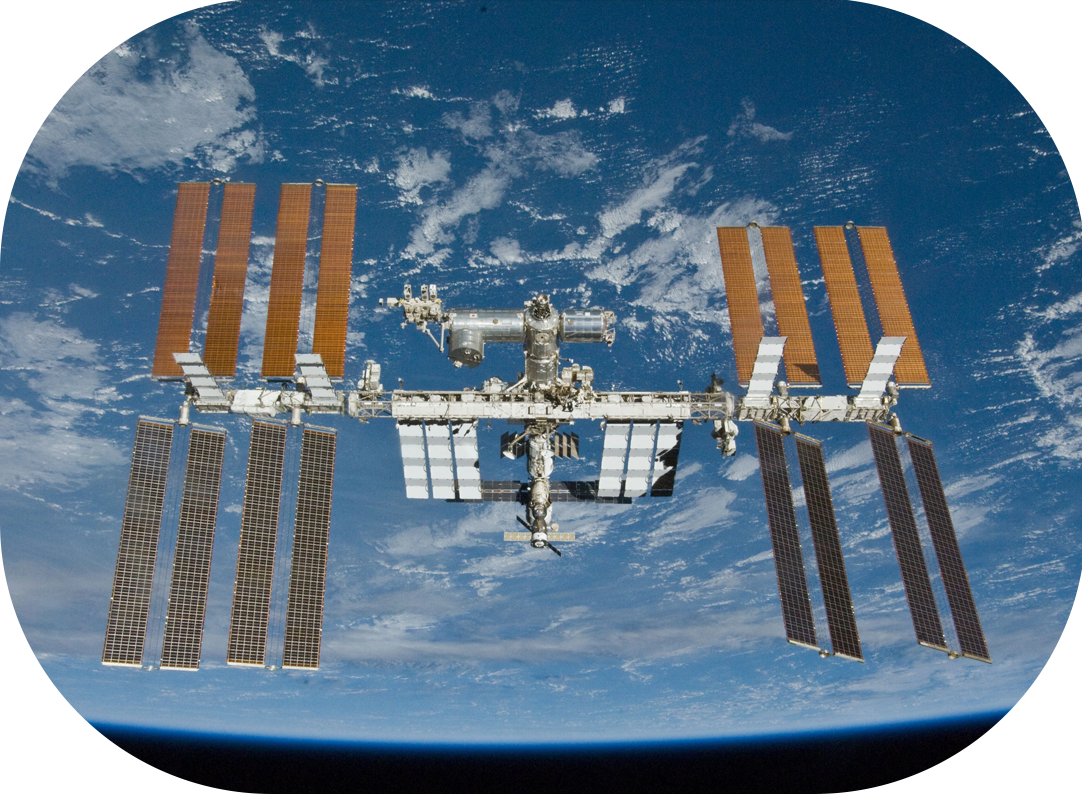
June 2017
ACT’s first Copper/Water Heat Pipe products onboard the International Space Station
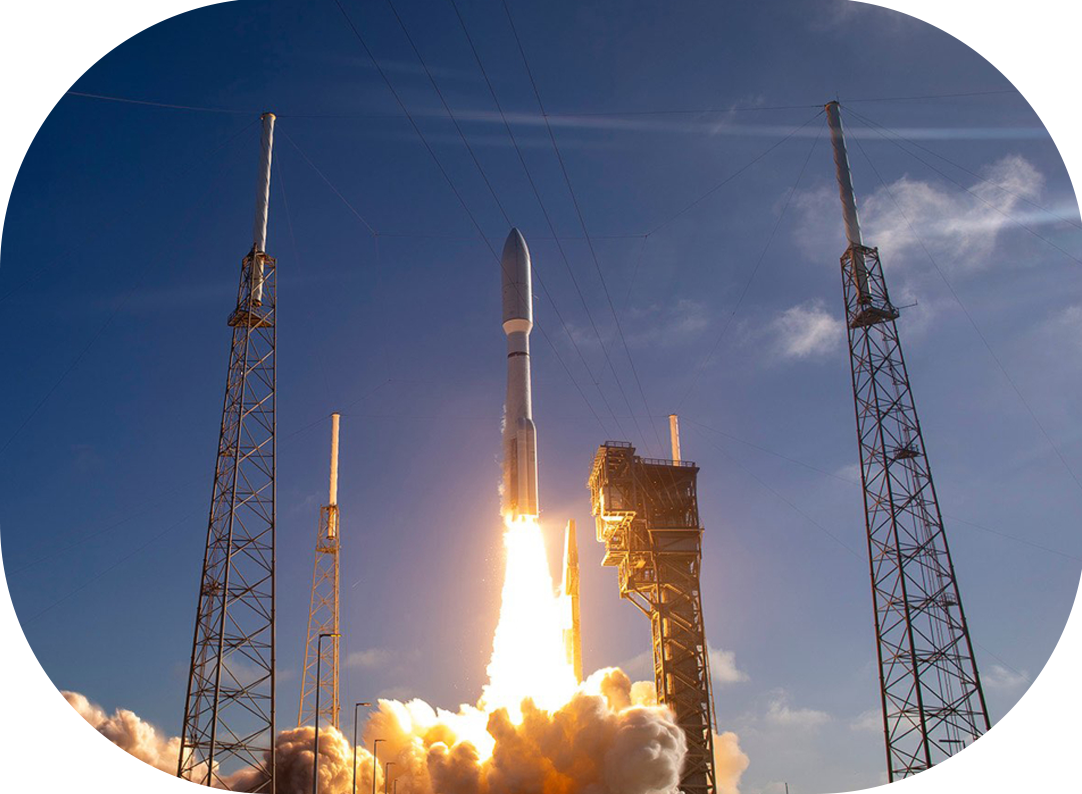
December 2016
ACT named a critical supplier for Next Generation NOAA / NASA Weather satellite GOES-R
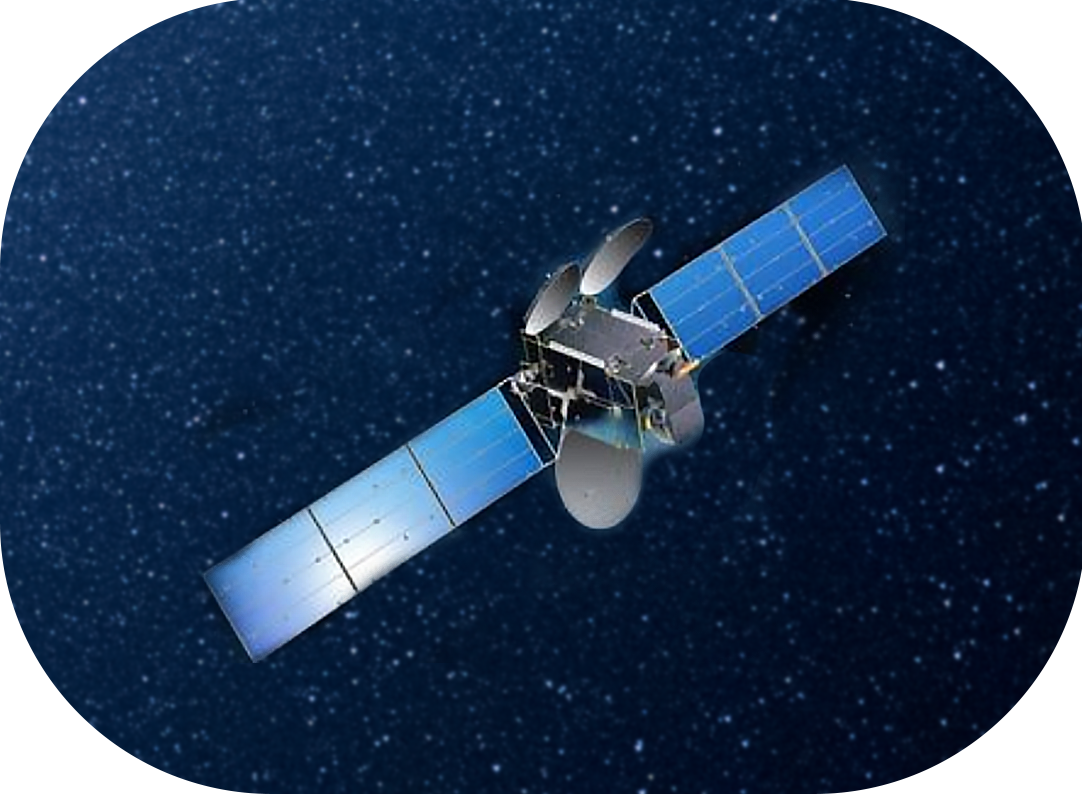
August 2016
ACT reaches 25th CCHP launch, on-board Boeing’s IS-33
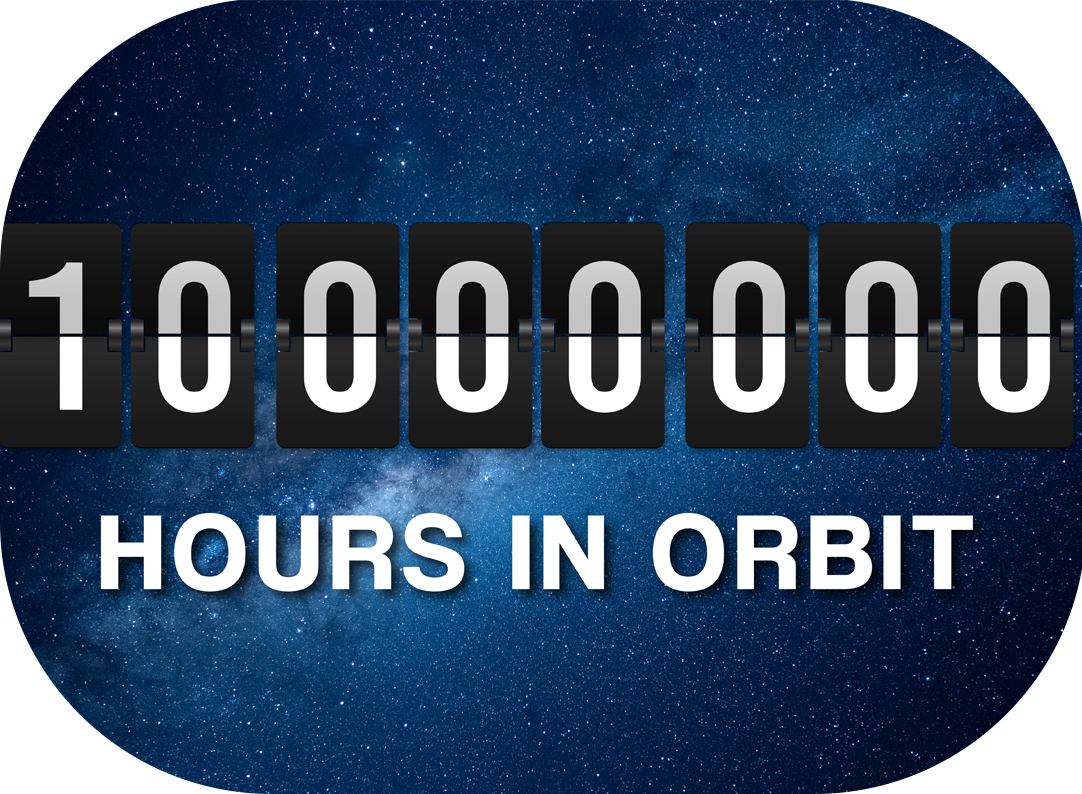
March 2016
ACT’s CCHPs reach 10 million hours on-orbit

January 2015
ACT’s first Fluid Accumulator products onboard the International Space Station
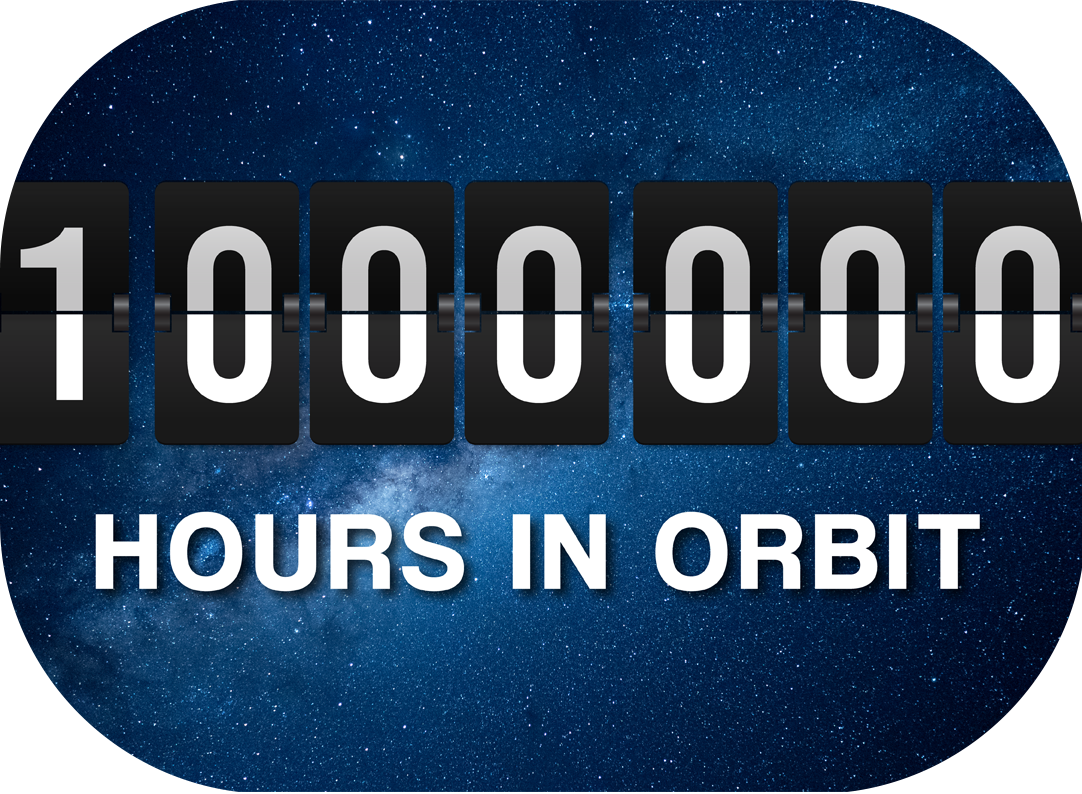
April 2013
ACT’s CCHPs reach 1 million hours on-orbit
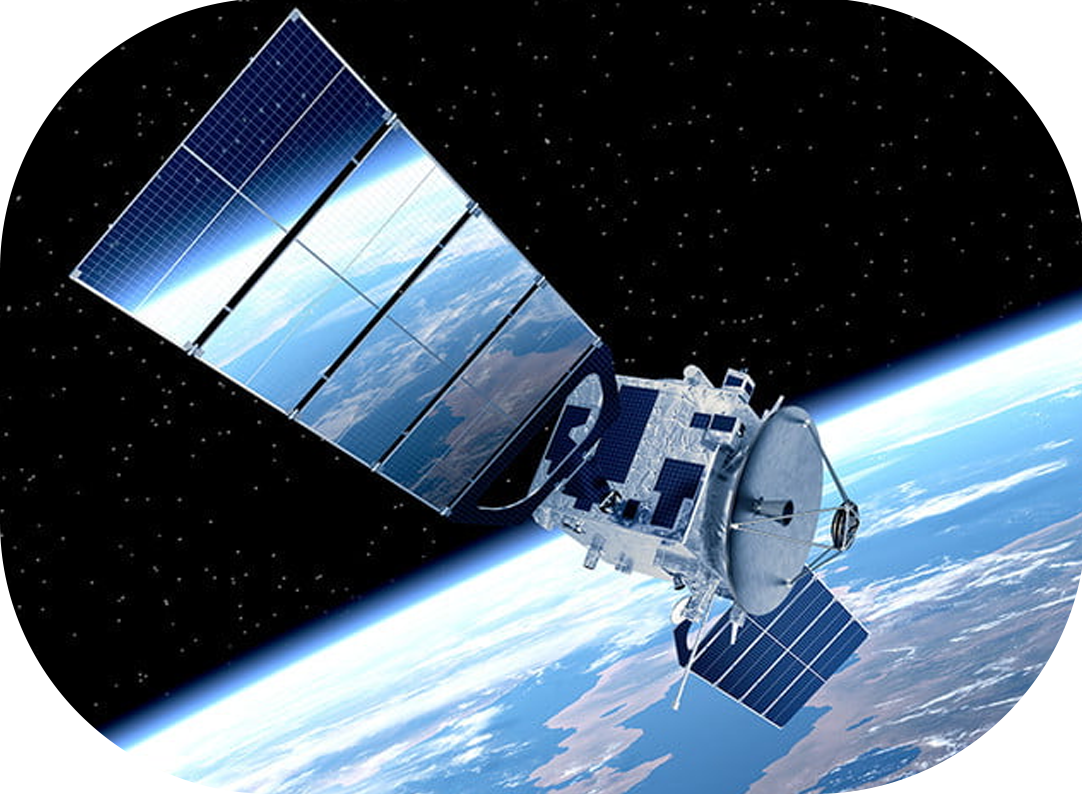
November 2012
ACT reaches its 10th CCHP launch, onboard STAR ONE C3
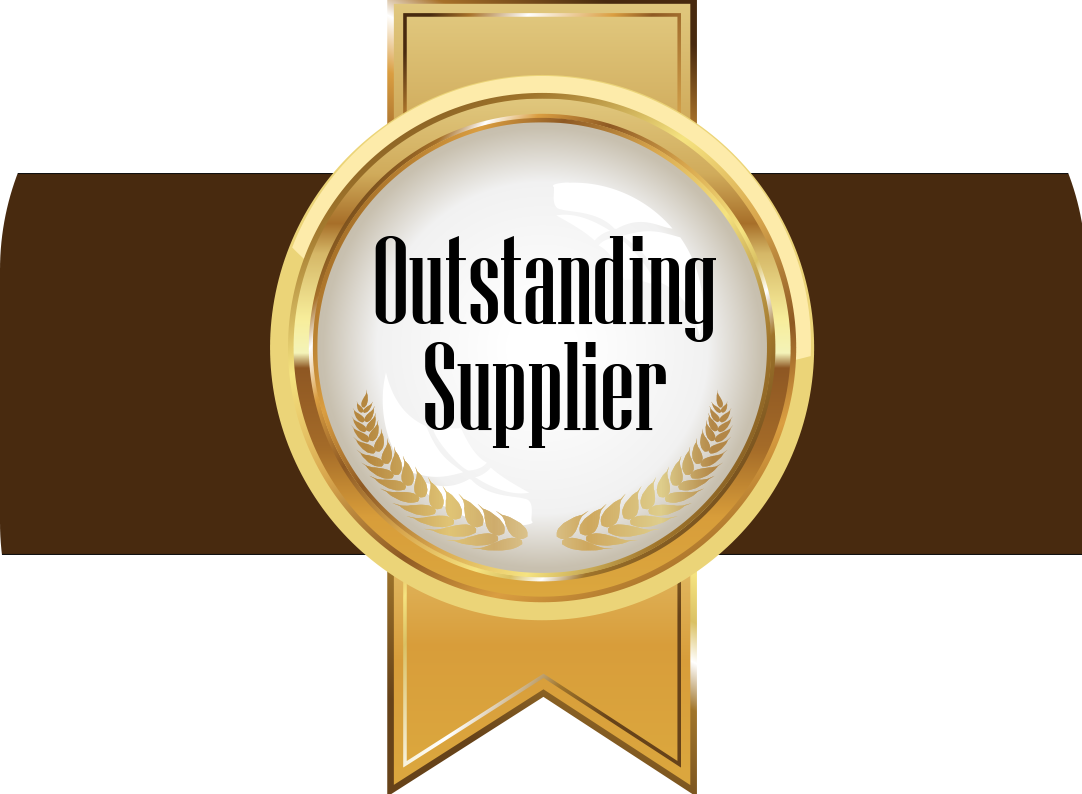
October 2010
ACT named Outstanding Supplier by ITT/Geospatial Systems Group for their contribution on ITT’s ABI and Himawari programs
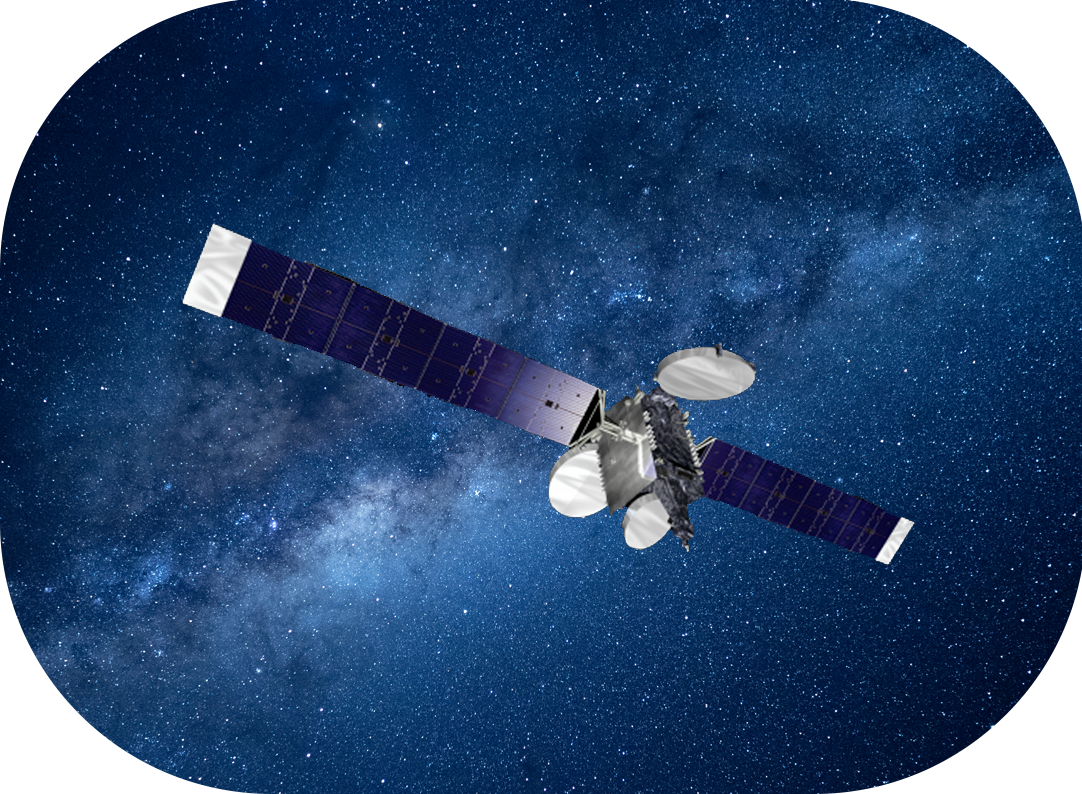
November 2009
ACT’s first CCHP launch, on Orbital IS-15
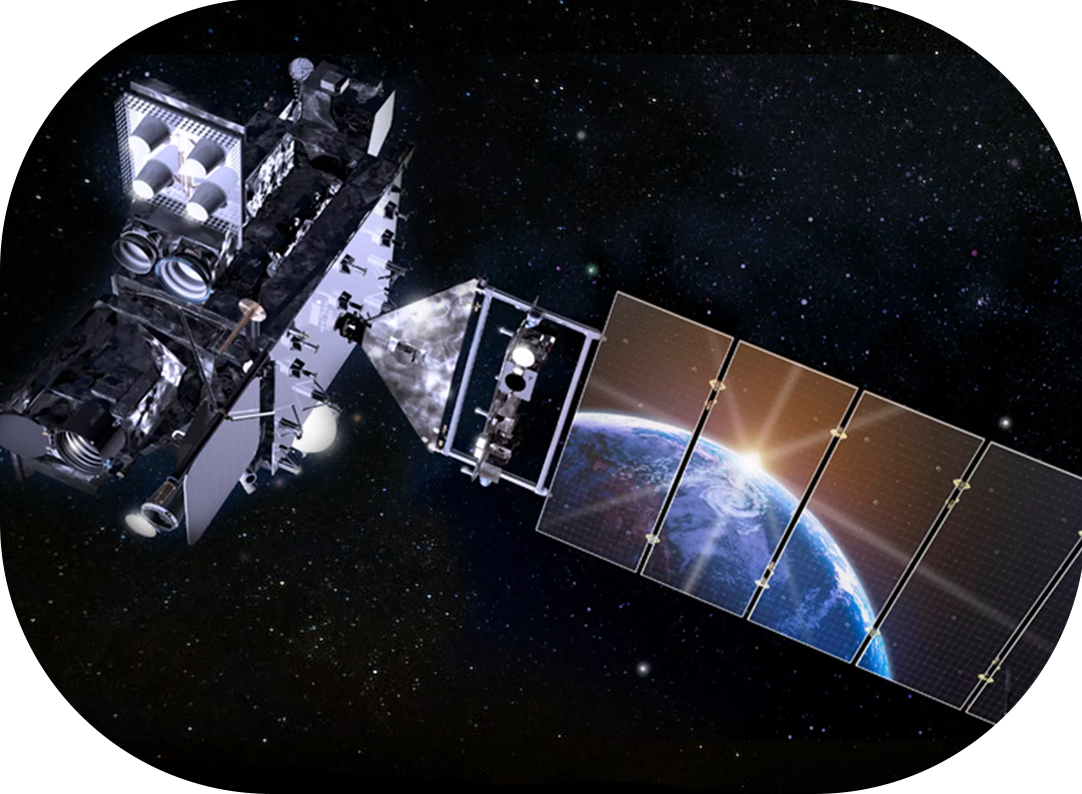
July 2007
ACT ships first production CCHPs to ITT for GOES-R, opening up other opportunities for ACT
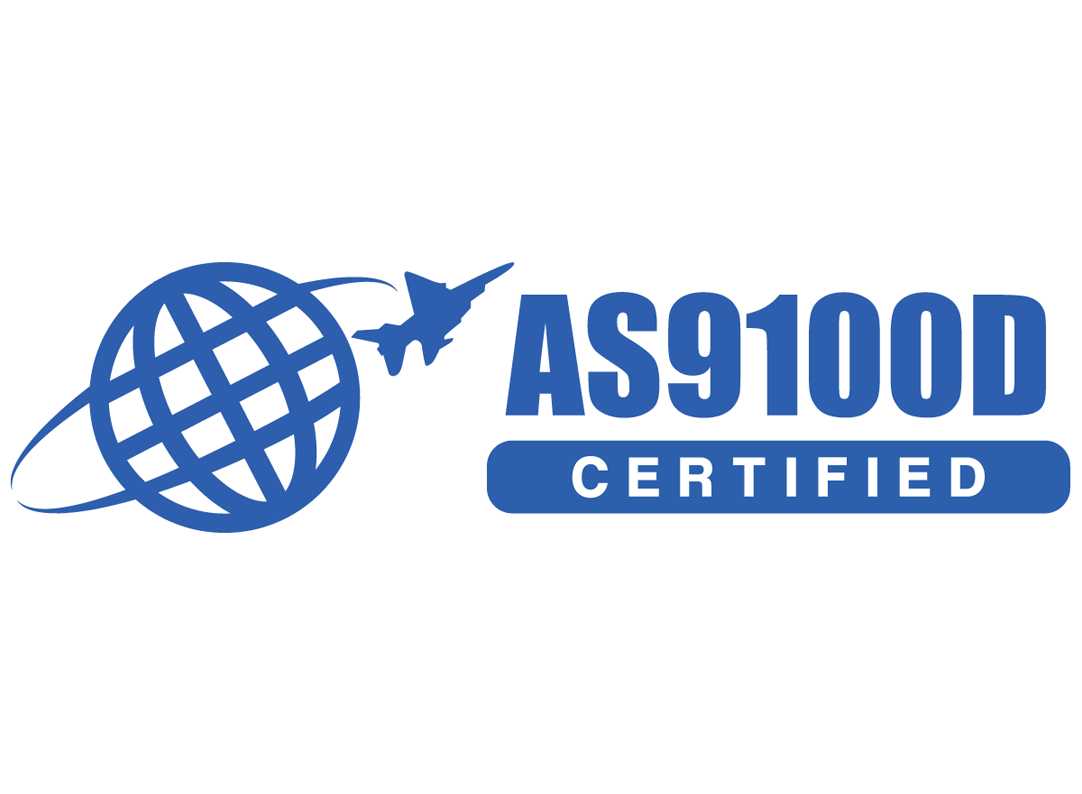
December 2006
ACT becomes certified to AS9100 quality standard and receives first CCHP production order
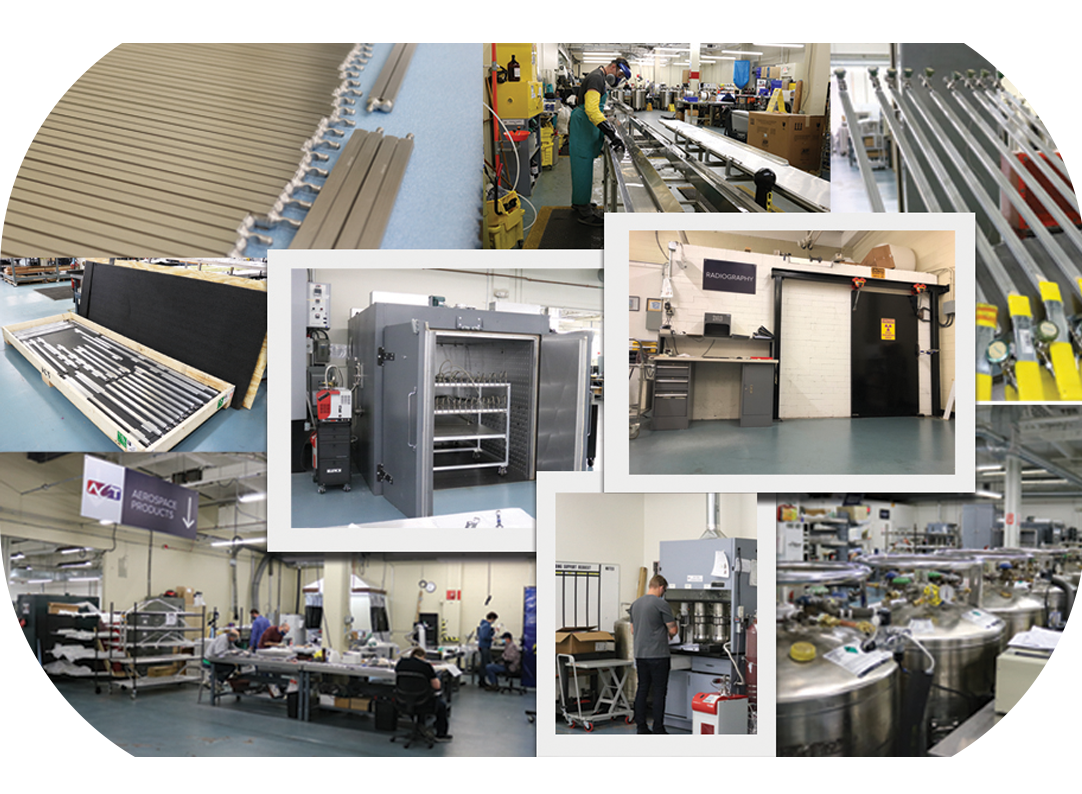
January 2006
ACT starts internally funded efforts to establish flight grade CCHP manufacturing infrastructure
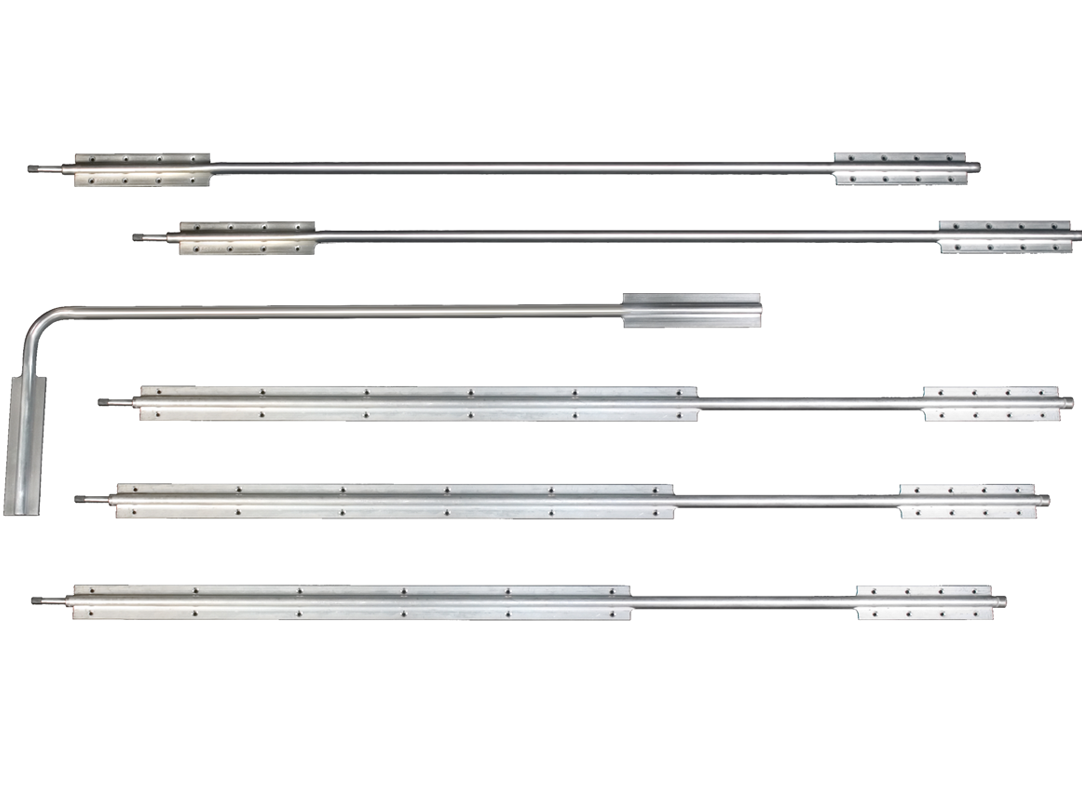
January 2005
ACT received an R&D contract from NASA Johnson Space Center to develop a spacecraft heat exchanger with Constant Conductance Heat Pipes (CCHPs)
Heat pipe reliability is of paramount importance for all aerospace heat pipes and loop heat pipes (LHPs). Many satellite applications require these products to operate without any degradation for more than ten years. ACT combines state-of-the-art facilities with world-class engineering to meet or exceed these requirements while paying strict attention to cost and delivery requirements. Contact a member of our team to discuss how we can become your partner in aerospace thermal management, or continue reading below to find out more about our best-in-class aerospace thermal management solutions.
ACT’S SPACE-RELATED PRODUCTS & Services
Thermal & Structural Design Analysis
ACT provides integrated thermal and structural design solutions for spacecraft, ensuring reliability during mission-critical operations. With expertise in thermal simulations, structural analysis, and manufacturability, ACT optimizes size, weight, and power (SWaP) while meeting cost and schedule constraints. Their capabilities include detailed thermal control assessments, shock and vibration analysis, and the development of advanced thermal technologies. ACT’s holistic approach minimizes complexity, resulting in robust and efficient spacecraft systems.
Constant Conductance Heat Pipes (CCHPs)
Among the most popular and reliable heat pipe products, ACT’s constant conductance heat pipes (CCHPs) transport heat from a heat source to a heat sink with a very small temperature difference. Axial groove capillary wick structures are utilized because of the relative ease of manufacturing (aluminum extrusions) and their demonstrated reliability in spacecraft and instrument thermal control applications. CCHPs can transport heat in either direction and are typically used to transfer heat from specific thermal loads to a radiator panel or as part of an integrated heat pipe radiator panel.
The team at ACT has extensive experience developing and manufacturing aerospace-grade CCHPs in our facilities and can offer a wealth of practical application knowledge for any project gleaned from our proprietary models and years of in-depth experience. Contact us to speak with a representative, or click the link below to learn more.
Typical Applications:
- Payload thermal management
- Heat transport
- Isothermalization
- Radiator panel thermal enhancement
Space Copper Water Heat Pipes (SCWHPS)
Copper-water heat pipes are the most commonly used heat pipe for military and consumer electronics, including almost all laptops and can be used in space applications as well. The SCWHPs we create for space applications have finely tuned-liquid calculations. The benefits of copper-water heat pipes in space applications include:
- Operate at temperatures up to about 150°C versus 60°C for ammonia (Titanium and Monel envelopes can be used to increase the temperature to 270°C)
- Accommodate high heat fluxes, up to ~75W/cm2
- Operate against adverse elevations of up to 25cm during ground testing
- Extremely easy to bend around components
- Survive thousands of freeze/thaw cycles
ACT originally worked with NASA Marshall Space Flight Center and Johnson Space Flight Center to demonstrate flight heritage for copper-water heat pipes through microgravity testing on the International Space Station (ISS). More recently, ACT authored a white paper that delves into the testing consideration for the Gen 3 Space Copper Water Heat Pipes (SCWHPs).
Typical Applications:
- Electronics thermal management
- Electronics Chassis
- Higher Temperature Cooling
- Spot Cooling
- Heat transport to Constant Conductance Heat Pipes (CCHPs) or Loop Heat Pipes (LHPs)
- High Evaporator Heat Fluxes, up to 75W/cm2
High Conductivity (HiK™) Plates
HiK™ plates use copper heat pipes that are flattened and embedded in an aluminum plate to increase the effective thermal conductivity. The heat pipe layout is tailored to most efficiently conduct heat from the electronics to the area where the plate is cooled. They are most commonly used as spreader plates and card guides. The benefits of HiK™ plates include:
- High Effective Thermal Conductivities, 500 to 1200 W/m K versus 200 W/m K for aluminum
- Operate at temperatures up to about 150°C versus 60°C for ammonia
- Much lower cost than encapsulated conduction cards
- Conduct heat around corners
- Available in lower mass Magnesium plates as well as AlSiC plates suitable for direct bonding
- Operate against adverse elevations of up to 25cm during ground testing
- Survive thousands of freeze/thaw cycles
ACT worked with NASA Marshall Space Flight Center and Johnson Space Flight Center to demonstrate flight heritage for HiK™ plates through microgravity testing on the International Space Station (ISS).
Typical Applications:
- Electronics thermal management
- Heat Spreaders in electronics chassis to move heat from electronics to box level
- Higher Temperature Cooling
- Heat transport to Constant Conductance Heat Pipes (CCHPs) or Loop Heat Pipes (LHPs)
Variable Conductance Heat Pipes (VCHPS)
Variable conductance heat pipes (VCHPs) are devices manufactured by ACT to achieve active temperature control. This is accomplished by blocking a fraction of the condenser with a small amount of non-condensable gas. When the heat load or the condenser temperature increases, the heat pipe temperature tends to rise. The increased vapor pressure compresses the non-condensable gas, exposing more condenser area and as a result, increases the heat pipe conductance. The opposite happens when the heat load or the condenser temperature decreases. The variation of the conductance keeps the heat pipe operating temperature nearly constant over a wide range of heat inputs and condenser thermal environments.
A modest level of control is achieved with an uncontrolled, passive reservoir. Precision control is achievable with a temperature-controlled reservoir. Axial groove capillary wick structures are often utilized because of the relative ease of manufacturing and their demonstrated reliability in spacecraft and instrument thermal control applications.
ACT manufactures our aerospace-quality VCHPs in-house using proprietary models and under strict AS9100:2015 quality guidelines.
Typical Applications:
- Passive thermal control of spacecraft electronics
- Over varying sink conditions
- Over a wide range of thermal loads
- Minimizing power requirements for survival heaters
Loop Heat Pipes (LHPS)
Loop Heat Pipes (LHPs) made by ACT can transport larger amounts of heat over longer distances than heat pipes. LHPs are often used in conjunction with CCHPs and VCHPs to transfer waste heat from spacecraft payloads to radiators. Ammonia is the most commonly used working fluid for temperatures between -40 and 70°C. Propylene and ethane are used for lower temperatures. ACT has also developed titanium/water LHPs for temperatures between 70 and 250°C.
Unlike some of our competitors, all of our Loop Heat Pipe parts, including the primary and secondary wicks, are quality-made in the United States at ACT’s facility under strict AS9100 quality controls. When you contact us about LHPs, you’ll be speaking to the people who engineer and manufacture them.
Typical Applications:
- Payload thermal management
- Heat transport
- Radiator panel enhancement
- Avionics cooling
- Aircraft anti-icing
Phase Change Material Heat Sinks (PCM) Heat Sinks
ACT is a leading provider of Phase Change Material (PCM) heat sinks for military, aerospace, and industrial thermal management applications. When heat storage is required, the heat sinks use the latent heat absorbed by melting the phase change material (PCM).
Spacecraft Applications:
- Smooth out temperature swings during cyclic operation allowing thermal solutions to be designed for the average heat load rather than the peak load
- Protection from failure during cooling interruptions, when the cooling system is temporarily unavailable (e.g, pumped single and two-phase cooling on satellites)
Accumulators for Pumped Fluid Systems
Accumulators are used to accommodate changes in the volume of a pumped loop across the broad temperature range experienced in spacecraft applications, from -40°C to +55°C. ACT introduced the accumulators in response to multiple requests for a rapid design and development supplier for custom, flight-qualified, fluid compensation systems.
ACT also has designed and fabricated custom Fluid Control Units (FCUs) to validate the overall pumped single-phase thermal control system with accumulators during ground testing.
ICE-Lok® (WEDGE LOCK)
The patented Isothermal Card Edge ICE-Lok® is designed to enhance thermal performance for conduction-cooled embedded computing systems. Compared to conventional wedge locks, the ICE-Lok creates additional heat transfer paths from card to chassis, thereby reducing the thermal resistance. In space, more than anywhere else, conduction is going to be the primary heat transfer path, therefore reducing resistance from the component to the radiator is of utmost importance. Enhancing the card-to-chassis link can provide several degrees of improvement on the overall system.
SpaceVPX- Payload Level Cooling
Through years of development, ACT has qualified and flown SCWHPs (space copper-water heat pipes) that feature more robust manufacturing techniques compared to that of terrestrial copper-water heat pipes– to survive the severities of space. Embedded computing systems are leveraged across many mission-critical platforms, but few with more challenging requirements than space vehicles. The power requirements for onboard processing, optoelectronics and other high heat flux components are very similar to terrestrial embedded computing applications; however, the space environment adds temperature extremes and other operational conditions that make the thermal design a major factor in system architecture.
Typical Applications:
- Board and chip-level cooling with high heat flux at the electronics and conduction being the primary bottleneck
