A Weld Apart: Aerospace Welding
It is common knowledge that putting technology into space is expensive, so it is no surprise that materials are often chosen for their ability to satisfy the needs of designers (strength, thermal conduction, or survivability in space) without adding too much weight to the overall architecture. But it is not just material selection that is affected by the unique constraints of working in the space industry. Manufacturing techniques—such as welding—also face extra scrutiny before being qualified for spaceflight.
Aerospace welding is the joining of two metals with a focus on the final product being used in or during aeronautics, both within Earth’s atmosphere and beyond. Applications that require aerospace-certified welding can range from the more terrestrial products—such as unmanned aerial vehicles (UAVs), gliders, and passenger aircraft—to space-bound satellites, rockets, rovers, and any other items that may be traveling out of Earth’s atmosphere.
What types of welding are approved for the Aerospace industry?
There are many methods that are approved, including gas tungsten arc welding (GTAW), friction stir welding (FSW), laser beam welding (LBW), electron beam welding (EBW), plasma arc welding (PAW), fusion welding, and so forth.
What makes Aerospace welding different from traditional welding?
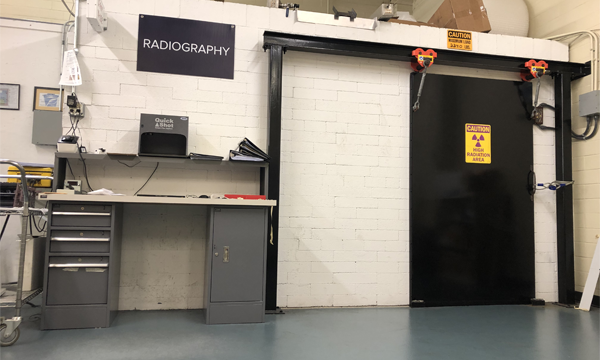
Aerospace welding differs from traditional welding in a few key areas that ensure the cleanliness of the end product, the survivability of the weld, and the verifiability of the weld’s success.
- All aerospace welding must be performed in a cleanroom. This verifies that the metals are not subject to any outside elements that may impact the weld or end product. Outside elements could cause catastrophic failure in the joint or system if stress corrosion cracking (SCC) occurs. Welding quality comes in many different levels of accuracy depending on the application. For terrestrial applications, there may be times when a quick, simple—and, possibly, not very clean—weld would be appropriate and provide a solution that meets expectations. For hardware that is being sent into outer space, the weld must be pristine on account of the inability, or impossibility, of repairing or replacing malfunctioning space-bound equipment.
- Compared to traditional welding, aerospace welding has a comparatively narrow range of allowable imperfections. Ideally, an aerospace weld will have no imperfections at all.
- Radiography is normally required of every component. Aerospace hardware undergoes radiography scans to check for inclusions, porosity, and lack of fusion in the welds; this also ensures the quality of the full assembly.
What types of imperfections should be avoided in welds for the aerospace industry?
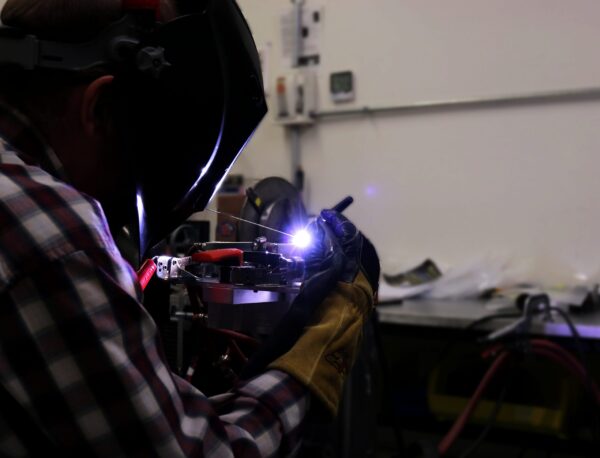
Imperfections can include the shape and size of the weld based upon the base material thickness, the number of inclusions (e.g., porosity, tungsten, other trapped alloys) that may be visible during the x-ray, any undercut or underfill of the weld joint, surface craters or cracks, lack of penetration within the entire joint, etc.
This leads to the third major difference for Aerospace Welding, which is that the requirements for aerospace hardware qualification are much more stringent and often require the radiography of every component. Aerospace hardware undergoes radiography scans to check for inclusions, porosity, and lack of fusion in the welds; this also ensures quality of the full assembly. To avoid complications, ACT has a dedicated climate-controlled clean room for aerospace welding. In addition to customer and industry requirements, some states’ Department of Transportation laws (including ACT’s home state of Pennsylvania) require pressure-filled vessels to be x-rayed before transport.
Many years ago, ACT realized that performing all work in-house for aerospace products would be vital to shortening lead times and lowering costs for our customers. This is especially important considering the need to verify quality throughout the manufacturing stages of aerospace systems, as well as the requirements to x-ray parts that are transported outside of the facility. This realization spurred immense amounts of internal research, training, and capital equipment purchases to set up the necessary in-house radiography and clean room with welding areas and machines; it also necessitated the training and certifying of skilled welders to provide aerospace-certified welds. This decade-long project resulted in ACT being able to perform aerospace welds internally, and ACT employees who are certified in inspecting D17.1 weld specification sign off on each weld. ACT is continually assessing our aerospace procedures with an eye toward continuous improvement (or expansion!) and to ensure the best quality of our aerospace products.
To give an idea of the rigorous certification process it takes to become an aerospace-certified welder, ACT welders follow an outlined work procedure to weld samples in different hold positions as part of their training. These samples are then sent out to 3rd party welding inspection and certification institutions. Destructive and non-destructive tests are completed in accordance with the AWS specs. Through this training process, an ACT employee can become certified once they have met all certification criteria and can produce the needed quality of the specified weld joint in various hold positions.
An interesting note about the certification process is that each type of weld will have slightly different criteria to meet for certification. In addition, the alloy chosen for certification can also slightly change the approach in how it is welded. For example, 6061 aluminum has difficulties being fusion-welded, while 316 stainless steel can easily be joined using that method. So being certified in one technique does not mean that a welder is certified for all types of aerospace welding.
ACT is honored to have built some amazing relationships over the years through the development of a variety of aerospace programs. These relationships have fostered the growth and innovations of such programs as ACT’s elite aerospace welding. As a testament to this innovative application and collaboration, ACT’s aerospace welding team was recently asked by NASA JPL personnel to consult on some very complex welding needs in support of the Europa Clipper mission. We are excited to be able to use this and other experiences to further our innovation within the industry.