Custom Phase Change Material (PCM) Heat Sink Design, Analysis and Manufacturing
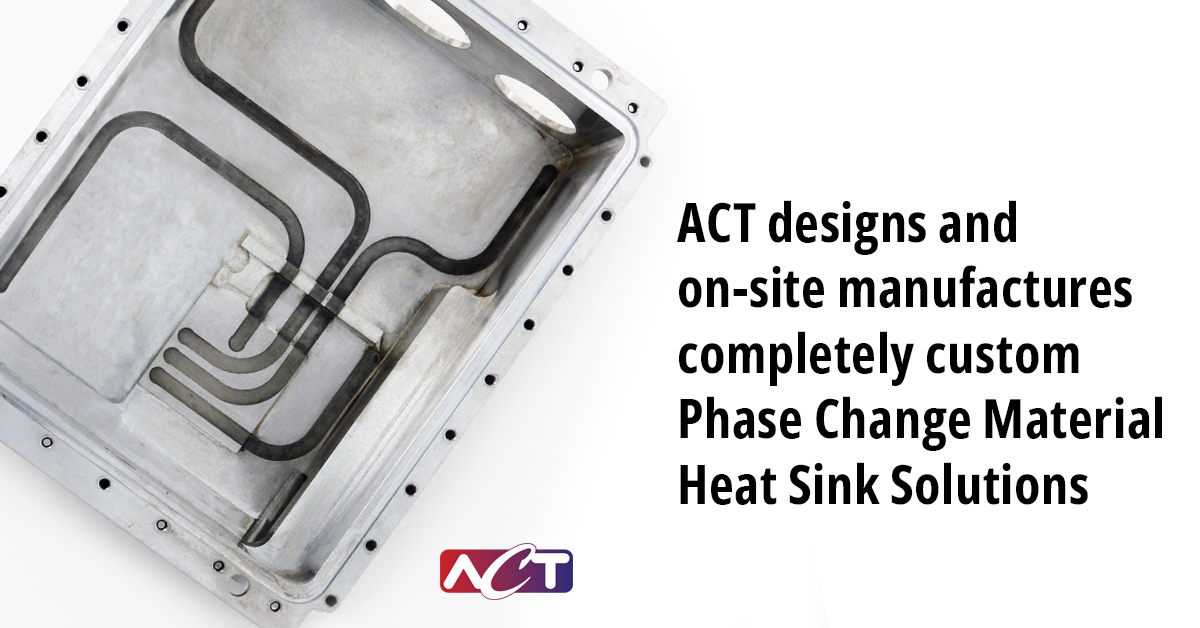
The concept of phase change material (PCM) is simple: they are substances that absorb and release large amounts of heat during the process of changing their phase (e.g., solid to liquid or vice versa).These substances melt and solidify at specific, defined temperatures, making them suitable for a wide range of thermal management applications. Thermal management with phase change materials can be challenging, as its different forms can have inadequate thermal conductivity on their own. While this seems counterintuitive, using these unique materials combined with expert heat sink engineering, can create incredibly efficient thermal management solutions.
How are Phase Change Material heat sinks used for thermal management?
Phase Change Material heat sinks can be used to even out transient heat loads that can occur during changes in environmental conditions, start-up or shutdown processes, and during intermittent, pulsed operations. By utilizing phase change material, heat sinks can be designed for the average heat load rather than the peak, so a smaller heat sink can be used. Phase change material heat sinks are valuable technology when concerning spacecraft thermal control, as it provides thermal storage for smoothing temperature swings during cyclic operation. When it comes to protecting components against momentary failure, phase change material heat sinks can be employed to absorb and dissipate heat generated during high-stress events or sudden spikes in temperature. These events can include power outages or surges, short circuits, or other transient failures that cause a rapid increase in temperature. The phase change material heat sink works as a short-term thermal storage device during loss of cooling capability, in order to protect delicate electrical components from overheating. Phase Change Material Heat Sinks can also be used in applications with a finite lifespan, like missiles. They provide a passive thermal energy storage solution that can replace complex, active thermal management, resulting in a compact, lightweight heat sink. ACT sets itself apart by offering the design and on-site manufacture of completely custom phase change material Heat Sink solutions. Expertise in vacuum brazing plays a critical role in the manufacturing process. Not only are ACT engineers thoroughly versed in the different types of phase change materials and their capabilities, but they also have expertise in analyzing Phase Change Material Heat Sink systems and predicting transient responses. In-house analytical tools and computational fluid dynamics software are leveraged for phase change material heat sink thermal simulations. In most cases, the end result is a that captures effects during multiple stages; and that can be used as one of several thermal management solutions that make up the larger, system-level solution.

But Why Do We Use Phase Change Materials?
Phase change materials happen to be fairly predictable in their phase change spectrum, proving highly reliable in heat storage and release capabilities. Here are a few reasons why PCM Heat Sinks are considered a reliable thermal management solution.
High Thermal Energy Storage Capacity
PCM Heat Sinks have the ability to store and release a significant amount of thermal energy during phase transition, compared to traditional materials like water or air. This high storage capacity allows them to effectively regulate temperatures and maintain thermal stability.
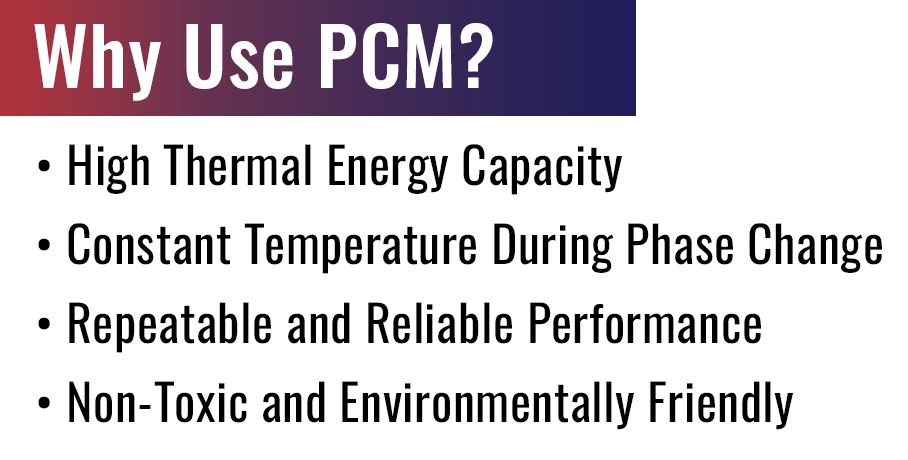
Constant Temperature During Phase Change
PCM Heat Sinks maintain a nearly constant temperature during the phase transition, also known as the phase change temperature or melting/freezing point. This property is advantageous for thermal management applications because it ensures a stable temperature in the surrounding environment. The PCM absorbs or releases heat energy without experiencing a significant temperature change until the phase transition is complete.
Repeatable and Reliable Performance
PCM Heat Sinks can undergo thousands of thermal cycles without significant degradation in their performance. They exhibit excellent thermal cycling stability, making them reliable for long-term thermal management applications. This repeatability is crucial in systems that require consistent and predictable thermal regulation.
Non-Toxic and Environmentally Friendly
Many PCMs are non-toxic, non-flammable, and environmentally friendly. They do not release harmful substances during operation, which is essential for applications near humans or sensitive environments. These properties contribute to the overall safety and reliability of PCM-based thermal management systems.
Why can’t I just have the machine shop fill my heat sink with PCM?
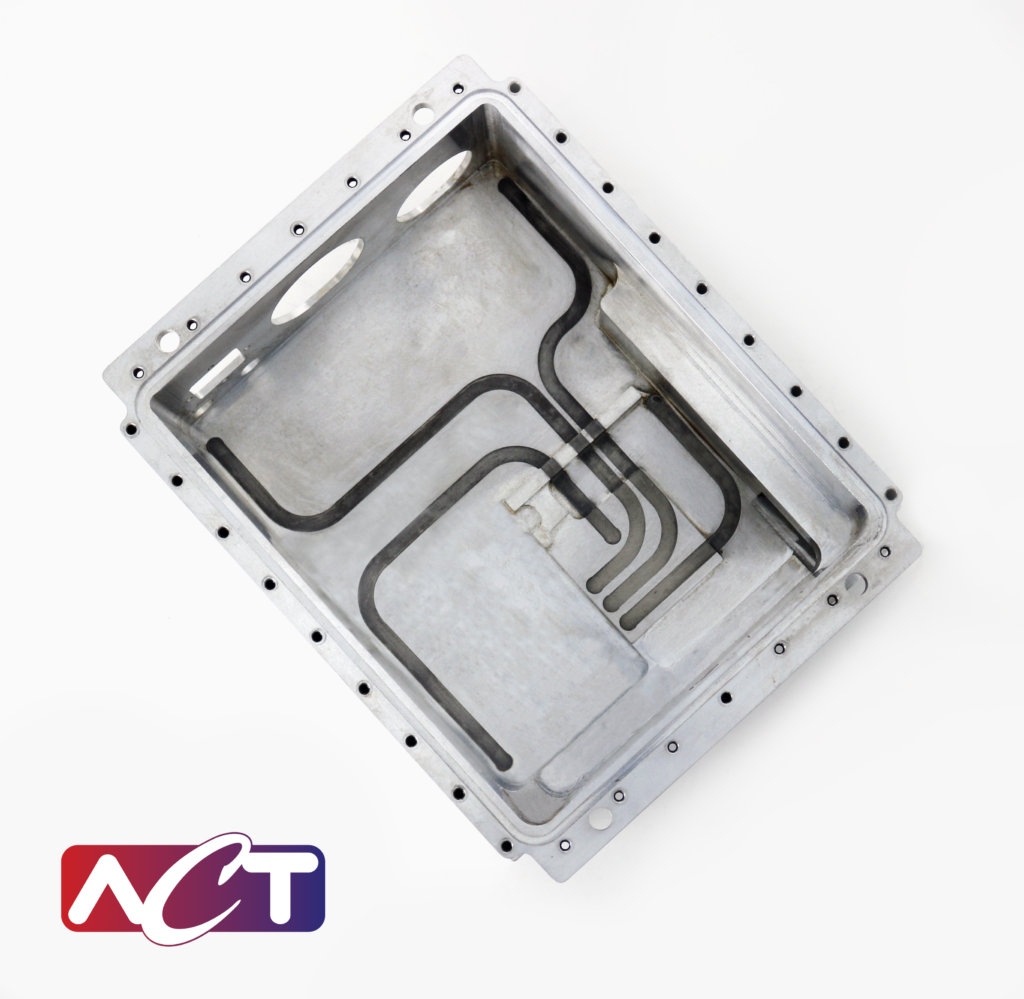
You can. But you’ll likely have no idea if your heat sink is going to actually address your specific thermal problem. The heat sink needs to be designed, modeled, and tested. It is only an effective thermal solution when it is paired with its correct type of thermal problem. In addition to the thorough understanding of how PCM works, engineers at ACT consider the structural needs of the thermal management system, in regard to the poor thermal conductivity. To remedy the issue, internal features are designed into the heat sink to make the most out of the PCM’s capabilities. ACT is experienced with the inclusion of fins, heat pipes and metal foams as options for custom internal structures.
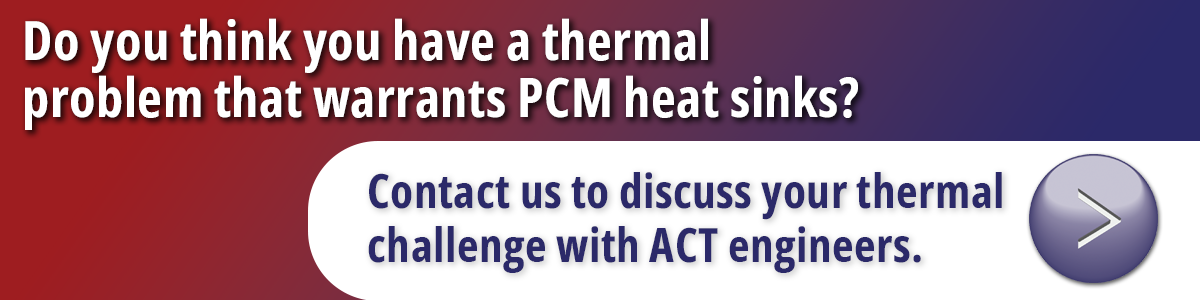