Decrease the Testing Cycle with Finite Element Analysis (FEA)
In product development, quick innovation while maintaining high-quality standards is key. Traditional product testing, though essential, can often be time-consuming and costly. This is where integrating Finite Element Analysis (FEA) into the development process can shorten the testing cycle, saving time and resources while enhancing product performance.
Understanding Finite Element Analysis (FEA)
Finite Element Analysis (FEA) is a computational technique used in structural analysis to predict how products will react to real-world forces such as, vibration, heat, fluid flow, and other physical effects. It involves breaking down a complex structure into smaller, manageable elements and analyzing each element’s behavior under various conditions. By solving these equations, FEA provides a detailed simulation of how the entire system will perform.
Adding analysis into the design process can improve the quality of the design by providing insights early on, reducing the need for extensive physical prototypes or an overly conservative design.
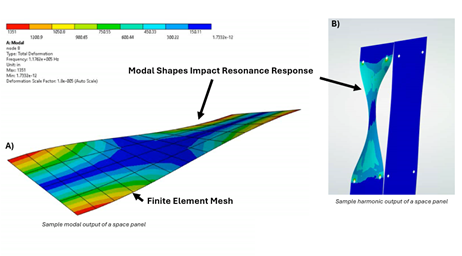
Figure 1. Example Dynamic Analysis of a Space Panel using FEA. A) Modal Output B) Harmonic Response
Figure 1 is an example of one of the many types of analyses we conduct for our customers. The modal output is the basis for a harmonic response because it provides the natural frequencies and mode shapes of the structure, which are used to decouple the equations of motion and efficiently compute the system’s steady-state response to sinusoidal (harmonic) excitation. By expressing the response as a combination of these mode shapes, the harmonic analysis becomes more computationally efficient and captures the resonance behavior accurately. This is important for ACT engineers to understand because a harmonic response can promote fatigue of the component leading to a shorter life span. Knowing this information before testing allows ACT engineers to include these considerations early in the design, ensuring the intended life span of the product.
FEA Empowers Engineers to Anticipate Failure Points
By simulating real-world conditions and complex loading scenarios, it uncovers design vulnerabilities early in the development cycle—well before costly prototyping or physical testing. This proactive insight allows teams to refine designs quickly and efficiently, minimizing the risk of expensive redesigns or delayed timelines.
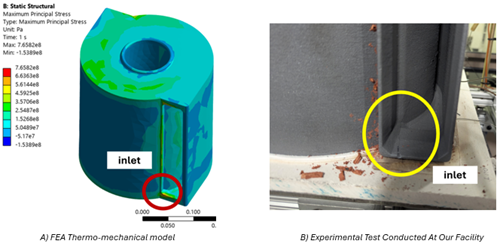
Figure 2. FEA Thermo-mechanical model (A) of cracking verified by experimental testing (B).
A great example from our own work: ACT’s FEA predicted cracking in a 3D-printed material subjected to combustion loading. Because we identified the failure mode early, we avoided more than six months of costly iteration between long-lead manufacturing and physical testing.
Optimization and Trade Studies Utilizing FEA for design trade studies can optimize the final product by reducing weight yet meeting stringent load requirements. Varying the structural configurations leads to the most efficient and effective design. We can evaluate a range of design and geometry variables to improve mechanical stiffness, mounting configurations and find the best balance between durability and weight. In Figure 3 we conducted a material stiffness trade study, an engineering analysis used to evaluate how varying the stiffness, typically represented by Young’s modulus, of a material changed the modal performance.
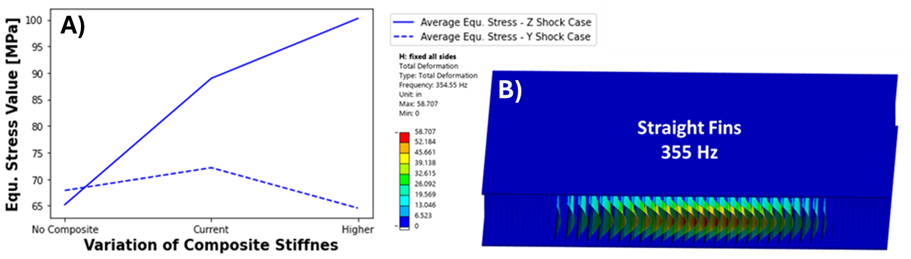
Figure 3. Trade study evaluation of equivalent stress value (A) and first modal response (B).
Types of Finite Element Analysis (FEA)
Type | Function | Benefits |
Structural (static) Analysis | Evaluates stresses, strains, and deformations under static loads. | Aerospace/Defense: Ensures rugged components survive launch or combat environments. Medical: Validates structural integrity of devices like surgical tools or enclosures. Energy: Confirms components (e.g., heat exchangers) withstand pressure/weight loads. |
Thermal Analysis | Models heat distribution, conduction, convection, and radiation in steady or transient states. | Electronics/Data Centers: Prevents overheating and improves thermal reliability. Aerospace: Validates spacecraft thermal designs under harsh environments. Industrial HVAC/ECU: Optimizes cooling strategies for enclosures or field-deployed units. |
Thermo-Structural (Coupled) Analysis | Evaluates the effect of thermal loads on mechanical behavior. | Defense/Aerospace: Essential for high-performance components exposed to thermal gradients. Energy: Ensures thermal expansion doesn’t degrade system performance or cause fatigue. |
Modal Analysis | Identifies natural frequencies and vibration modes. | Aerospace/Defense: Prevents resonance in structures, protecting payloads. Medical Devices: Ensures sensitive equipment avoids unwanted vibrations. |
Harmonic/Vibration Analysis | Assesses system response to dynamic, oscillating forces. | Automotive/Aerospace: Validates fatigue resistance under real-world vibrations. Data Centers: Ensures frame or board-level hardware isn’t vulnerable to vibration-induced failure. |
Transient Dynamic Analysis | Simulates how structures respond to time-varying forces (e.g., shock, impact). | Military Systems: Assures survivability during impacts, drops, or blasts. Spacecraft: Models deployment sequences and launch shock events. |
Fatigue and Life Prediction | Predicts failure due to cyclic loading over time. | Energy/Aerospace: Supports long-life designs with fewer maintenance interventions. Medical/Defense: Confirms product reliability under repeatable stress cycles. |
Nonlinear Analysis | Handles large deformations, material nonlinearity, or contact problems. | Defense/Aerospace: Simulates real-world behavior of flexible or composite structures. Industrial: Validates gasket sealing, clamping, or press-fit scenarios. |
Buckling Analysis | Determines critical load at which structural instability occurs. | Space Structures: Ensures lightweight panels don’t collapse under compression. Data Center Infrastructure: Validates thin sheet metal or support frames. |
CFD-Coupled Thermal/Structural Analysis (when integrated with Computational Fluid Dynamics) | Solves fluid-thermal-structural interactions in complex systems. | Data Centers & Electronics: Optimizes airflow and heat sink design. HVAC/ECUs: Predicts thermal-mechanical performance across temperature extremes. |
Finite Element Analysis (FEA) is not just a tool; it’s a strategic advantage in modern product development. By integrating FEA into the design and testing phases, companies can detect and address design flaws early, optimize performance, reduce prototyping costs, and accelerate time-to-market. In an era where speed and efficiency are crucial, leveraging FEA can make all the difference in staying ahead of the competition and delivering innovative, high-quality products.