Heat Pipes in Space: CCHPs used at the System-Level
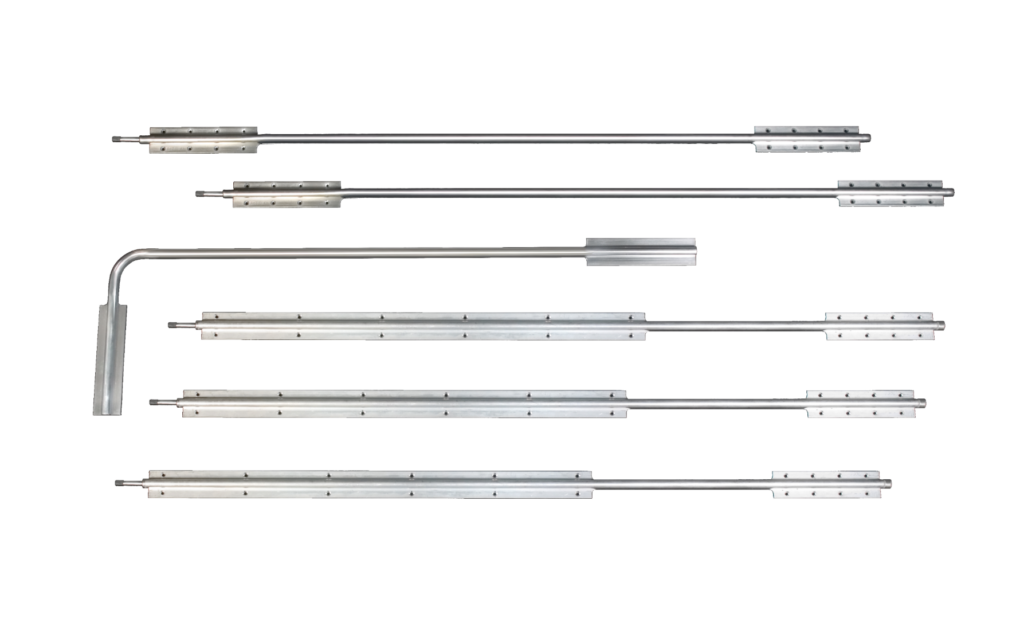
CCHPs are well known to the experienced Satellite Designer, and the term generally refers to the use of aluminum-ammonia heat pipes in satellites to transfer heat from the electronics payloads to radiator panels. These products have been used as thermal links on satellites for decades; to demonstrate their widespread use, ACT’s CCHP product line recently reached a milestone of 50 million spaceflight hours, with zero failures. Additionally, ACT CCHPs will be used as a key thermal component aboard the Nancy Grace Roman Space Telescope, which is the successor to the renowned Hubble Telescope.
ACT has been celebrating this project and its honoree (NASA’s first Chief of Astronomy and its first female executive, among many other accomplishments) throughout Spring 2021, with Women’s History Month in March and looking towards May 16th, Nancy Grace Roman’s birth date. One of ACT’s female engineers noted that “Nancy Grace Roman has played such a significant role in pushing the careers of females in STEM forward for generations and I’m excited that we [ACT] have the opportunity to embrace her legacy and employ females in both aerospace and engineering programs!” Kristen provided information for this review of Constant Conductance Heat Pipe (CCHP) technology and during discussions enthused that, “It’s such a fun time to be part of the aerospace innovation that is happening around the globe and we couldn’t be happier to have the opportunity to work on the NGR project!”
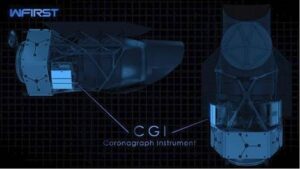
Let’s turn back to our focus on system-level thermal management to answer the following:
- What is a Constant Conductance Heat Pipe (CCHP) and how are they used?
- How are Constant Conductance Heat Pipes (CCHP) different from traditional heat pipes?
- Why are Constant Conductance Heat Pipes (CCHP) important to spacecraft thermal control?
- How do Constant Conductance Heat Pipes (CCHP) mount and what are the size ranges?
- Real examples of Constant Conductance Heat Pipes (CCHPs)
What is a Constant Conductance Heat Pipe (CCHP)?
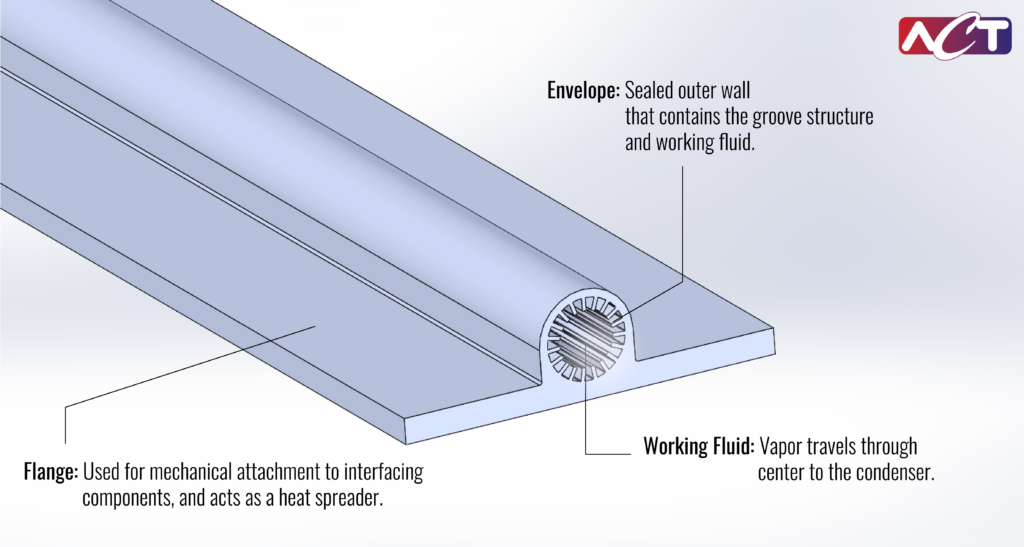
A Constant Conductance Heat Pipe is a vessel that provides efficient heat transfer by evaporating and condensing a working fluid. Through this process, heat can be carried from source electronics to another location where it can be radiated from the vehicle. CCHPs are designed to a specified length and diameter that are sized to meet the most challenging operating case – highest power, worst-case temperature – of the spacecraft. They are constructed using high-quality (or aerospace-grade) aluminum and ultra-pure ammonia. CCHPs have a unique extrusion that defines a proprietary internal core that combines a large open space for the vapor to travel through, and a wick structure that helps return the liquid to the hot spot to repeat the cycle.
How are Constant Conductance Heat Pipes (CCHPs) different from traditional copper-water heat pipes?
CCHPs are not vastly different from terrestrial heat pipes that have been used for decades with regularity for electronics cooling in a variety of applications. The physics and functional purpose are the same, but there are a few important differences.
Some differences include:
- Typical working fluid and envelope material: The average temperature range is quite different for terrestrial applications and space condition
- Typical copper water heat pipes are constructed of – you guessed it – copper envelopes with a water fluid charge. These systems support standard electronics packages where typical operation coincides with where water likes to exist: between 60-80°C.
- Spacecraft, depending on size, orbit, and wherein the system the CCHPs resides, can see a much wider (and colder) temperature range. It’s common for applications to require CCHP operation down to -40°C. Ammonia is selected because 1) it can survive and even operate in these temperature ranges, and 2) it is compatible with aluminum. These combine within a passive system that can operate over a broad temperature range in a low-mass package.
- Groove structure: Internal axial grooves for CCHPs and internal sintered metal wick for terrestrial heat pipes
- The internal groove structures are optimized for the application. Terrestrial heat pipes need a small pore radius to generate enough capillary pressure to work against gravity, but sacrifice permeability. CCHPs, on the other hand, do not have to work against gravity during operation in space. The system, therefore, can use axially grooved extrusions that are optimized to carry a high amount of power (high permeability) without needing to operate against the influence of gravity.
- This difference drives two main considerations for CCHPs. First, any testing to be performed on the CCHP cannot be done against gravity – 0.1” against gravity is typical; special attention needs to be placed on the anticipated test configuration. Additionally, the axial grooves have a lower boiling limit than a traditional sintered wick; the former is about 5-10 W/cm², while the latter is around 50W/cm².
- Manufacturing protocols required to produce critical spaceflight hardware
- When a satellite is launched, there are no space equipment repair specialists available to fix the problem. As such, any heat pipe slated for spaceflight must have all fabrication processes well understood, defined, and controlled. These processes have been established and refined each year ACT has produced spaceflight CCHP hardware, and >50 million hours without a single failure is a testament to the process controls in place. Space-grade copper water heat pipes are made to a higher standard than terrestrial copper water heat pipes since the working fluid (water) inventory and envelope play such a large role in the pipe freeze/thaw tolerance and long-term reliability (more info below).
- Qualification testing is required to validate that the design will survive the harsh operating environment of space
- Similar to the previous point, spaceflight hardware is typically accompanied by a very robust qualification test program. These programs are structured to force the systems to experience the harshest conditions that are expected during operation and takes the form of thermal cycling tests, pressure tests, thermal performance testing, and some dynamic testing. Copper water heat pipes have an added challenge since water freezes at 0°C, and expands when it does. ACT’s space copper water heat pipes have passed the rigors on multiple spaceflight qualification programs,
- Typical terrestrial copper water heat pipes do not face the same level of testing, and most applications do not see the continuous freeze-thaw cycles experienced in space applications.
- Hazardous material consideration
- Ammonia is hazardous, water is not (at least, not to us). As such, you need the appropriate infrastructure and controls in place to deal with hazardous material when fabricating CCHPs. Additionally, ammonia systems are shipped under a special provision that certifies all ammonia-carrying hardware has experienced a sufficient amount of testing and inspection to verify a failure will not occur under typical transit conditions.
Why are Constant Conductance Heat Pipe (CCHP) important to spacecraft thermal control?
Removing heat from a satellite can be tricky since there is no air or other medium around to simply cool it by convection. Instead, heat has to be removed via radiation from panels on the exterior of the craft; however, transporting the heat from the electronic components in the avionics box to the radiator panel requires a physical structure for conduction. Solid, thermally-conductive materials can be used, but transporting heat across the distances required incurs large delta T and weight penalties. Thermally, it’s critically important to minimize delta T; the goal is to find a balance in keeping the electronics within their operating temperature range, but having the radiators operate as hot as possible. If the radiator operates hotter, it can be designed for lower mass and physical size. So, while there is plenty of delta T available when sinking to the low temperature of deep space, it’s not desirable to utilize large conduction gradients when transporting heat to the radiator. Constant Conductance Heat Pipes (CCHP) provide a method to transport heat much more efficiently by utilizing the latent heat of a working fluid – via evaporation and condensation – as it passively circulates within the sealed vessel. In low gravity environments, CCHPs can transport thermal energy several meters and be bent into a wide variety of 2D and 3D configurations
In addition to collecting the heat from the payload and transporting it to the radiator panels of the vehicle, Constant Conductance Heat Pipes (CCHPs) are also often embedded in the radiator panels themselves. In this configuration, the CCHPs serve to distribute the heat across the panel, bringing the entire panel to a more uniform temperature, which greatly increases the efficiency of the radiator panel, allowing for significant size and weight reductions. This concept is very similar to isothermalizing the base of an air-cooled heat sink to improve fin efficiency and overall performance.
How do Constant Conductance Heat Pipes (CCHPs) mount and what are the size ranges?
In many cases, it’s known that heat transport via CCHPs will be required, but it’s not until the bus architecture and electronics layouts are finalized that development for the final CCHP network layout and drawing packages occur. In other cases, CCHPs may be an afterthought, but luckily, they can be added at any juncture in the design cycle.
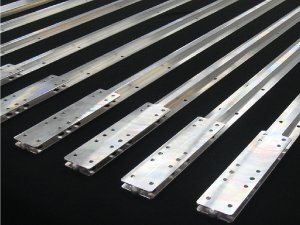
When working on design implementation, some useful information to note is that CCHPs are typically surface mounted directly to the radiator panels or embedded within them. They are designed with mounting surfaces (usually integral) and can be designed to any length that can be extruded- ACT has seen some designs upwards of 15’ long. The sizing for CCHPs depends on the location and footprint of components and radiators. Once this geometry is known, the heat pipe diameter and profile can be considered based on the transport power.
While there are many considerations for power capacity, the two most critical parameters are the diameter and length of the CCHP. In general, higher transport capacity can be achieved when shortening the transport length and/or growing the diameter of the pipe. There is also a choice between single and dual-bore versions, which depends on the amount of power, height profile, and safety factor required. As noted above, the length of the heat pipe is typically determined by the satellite architecture, therefore at this stage of the design, the diameter and number of pipes are usually determined based on the waste heat onboard.
Real Examples of Constant Conductance Heat Pipes (CCHPs)
ACT has CCHP programs on many satellites in orbit, but let’s look at 3 significant programs.
- As mentioned at the beginning of this post, ACT’s aerospace engineering team has recently been named as a key thermal management supplier for the Coronagraph instrument aboard the NGR space telescope. Due to the complex geometry of the coronagraph in relation to the radiator panels, CCHPs play an important role in ensuring the sensitive optical sensor can function at peak performance.
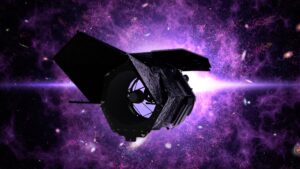
- U R Rao Satellite Centre (URSC), the lead division for building satellites and developing associated satellite technologies for the Indian Space Research Organisation contracted ACT to manufacture over 600 space flight Aluminum-Ammonia Constant Conductance Heat Pipes (CCHPs) from 2018 through 2021. This was the first large non-US contract in ACT’s history and is a significant step for the globalization of ACT’s space products.
- The Geostationary Operational Environmental Satellite-R Series (GOES-R) advanced geostationary weather satellite technology starting in 2016. They incorporated Harris Corporation (now L3Harris)’s new Advanced Baseline Imager (ABI). The ABI provided three times more data and color, four times better resolution, and five times faster speed than previous technologies. ACT’s aluminum/ammonia constant conductance heat pipes (CCHPs) were a key component to the successful thermal management system of the ABI. Each ABI utilized fourteen (14) unique heat pipe geometries to isothermalize mounting structures and transport excess heat from the ABI electronics to the thermal dissipation radiators. ACT’s CCHP manufacturing program benefitted greatly from the collaboration and experiences of the team at Harris and the NASA oversight, leveraging lessons learned in this program for all later CCHP development.
Constant Conductance Heat Pipes (CCHPs) as part of a thermal management system
CCHPs play an important role in moving the spacecraft markets forward as more start-ups and private companies seek access to qualified thermal solutions. Unfortunately, CCHPs are not a panacea for all thermal problems in space. CCHPs are unable to meet the challenge of unprecedented levels of waste heat at the board and box level that Satellite Designers are currently facing. With satellites launching almost weekly, there are scores of designers facing requirements to find a way to enable migrating more computer processing to the board level of the satellite rather than transmitting to ground stations.
ACT’s Space Copper-Water Heat Pipes are well-positioned to assist in meeting these new challenges for thermal loads as they are generally smaller than Constant Conductance Heat Pipes (CCHPs) and can work at higher working temperatures. These two heat pipe technologies can also work in conjunction with the SCWHPs removing heat from the box and then CCHPs carrying the heat to radiator panels. Check back for a closer look at Space Copper Water Heat Pipes (SCWHPs) in the next edition of this series on using Heat Pipes in Space.
Another technology often coupled with CCHPs is Phase Change Material (PCM) heat sinks. PCM can provide transient thermal absorption to provide spacecraft-level size and mass benefits for those vehicles operating with a duty cycle. Manipulating and transporting heat to and along the PCM is critical since PCM has low thermal conductivity, so CCHPs can provide additional thermal capabilities if PCM cannot be integrated local to the heat source(s)
About Advanced Cooling Technologies, Inc.
ACT has been providing CCHPs for critical spaceflight programs for over 10 years. Over this period, ACT has fine-tuned this product line by investing millions into the manufacturing tools, staff, and development of internal programs to build a world-class team of talent and capabilities.
If you’d like to learn more about custom thermal solutions for small satellites, download our ebook or visit our webpage for more information on all of the custom spacecraft products that ACT develops to specification.
Tell us about a project you’re working on that is facing thermal challenges: send us a contact form and get a discussion started with our engineers.
- Let’s turn back to our focus on system-level thermal management to answer the following:
- What is a Constant Conductance Heat Pipe (CCHP)?
- How are Constant Conductance Heat Pipes (CCHPs) different from traditional copper-water heat pipes?
- Why are Constant Conductance Heat Pipe (CCHP) important to spacecraft thermal control?
- How do Constant Conductance Heat Pipes (CCHPs) mount and what are the size ranges?
- Real Examples of Constant Conductance Heat Pipes (CCHPs)
- Constant Conductance Heat Pipes (CCHPs) as part of a thermal management system