Exploring Nuclear Energy Thermal Management Solutions
Nuclear energy is the leading source of emission-free electricity in the United States; the second largest across the globe. Like its green energy counterparts, it produces zero carbon emissions for power conversion.
In 2021 alone, nuclear energy saved over 470 million metric tons of carbon from polluting the atmosphere. That’s the equivalent of removing 100 million cars from the road!
Yet, it comes with its own set of safety concerns. Through nuclear energy thermal management solutions, engineers are making strides in harnessing nuclear energy in a safer, more efficient manner.
How Nuclear Energy Works
Nuclear energy is created through the splitting or joining of atoms called fission or fusion. Fusion happens when 2 small atoms merge to form a single, heavier atom; fission occurs when a small “incident neutron” excites a larger atom, splitting it into 2.
The most common isotopes for fission are Uranium-235 and Plutonium-239.
When atoms split during fission, the result is additional incident neutrons, which continue splitting other atoms. The chain reaction of fission releases energy in the form of heat and nuclear radiation.
Nuclear power plants can retrieve the heat created from nuclear fission to generate electricity to power homes, businesses, schools, hospitals, large machinery, and more.
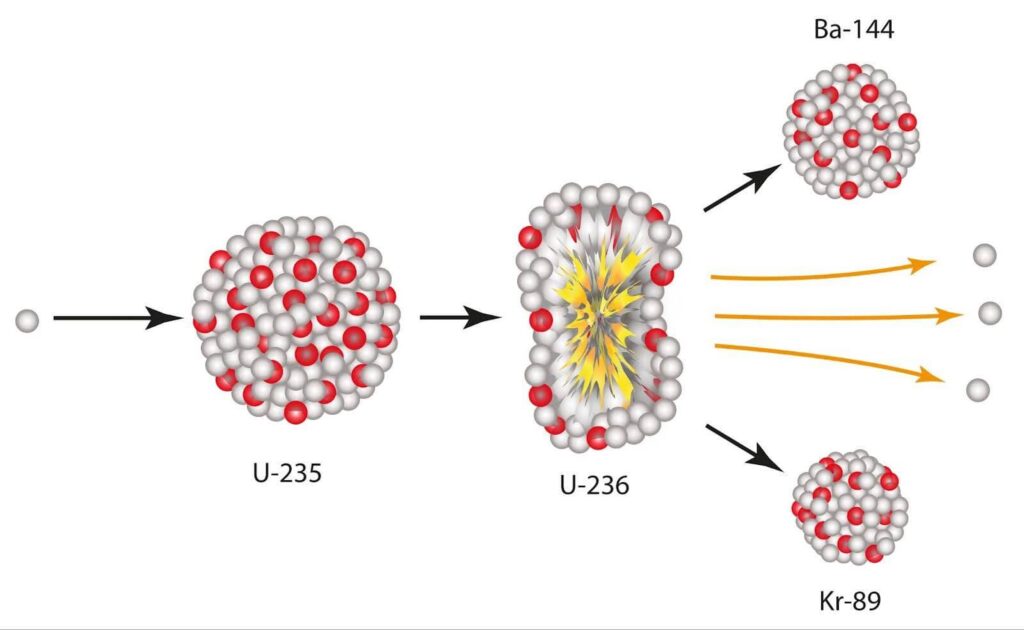
Thermal Management in Nuclear Energy
Though it’s considered to be a reliable source of electricity generation, nuclear energy thermal management is critical for safe heat recovery in power plants. The first challenge is controlling the rate of nuclear fission.
When the starter neutron splits the Uranium atom into 2, it releases 3 neutrons, which ignites a chain reaction of atoms splitting. Fission produces heat. If that heat isn’t controlled, the primary coolant can boil off, causing a string of subsequent disasters.
To avoid a meltdown, control rods, which are fabricated with materials to absorb neutrons but bypass fission, are inserted into the core to maintain the reactor’s internal temperature.
Traditional nuclear energy thermal management solutions, like Pressurized Water Reactors (PWRs), use active thermal technology to control the heat levels around the nuclear reactor. This means they rely on electricity for the system to function.
In the event the nuclear power plant’s source of electricity is cut off and/or the backup generators fail, the system can no longer transport heat away from the reactor core. Since the rate of fission can’t be controlled, the reactor will need to be taken offline to stop the reactor core from overheating, and eliminate the chances of a radioactive explosion.
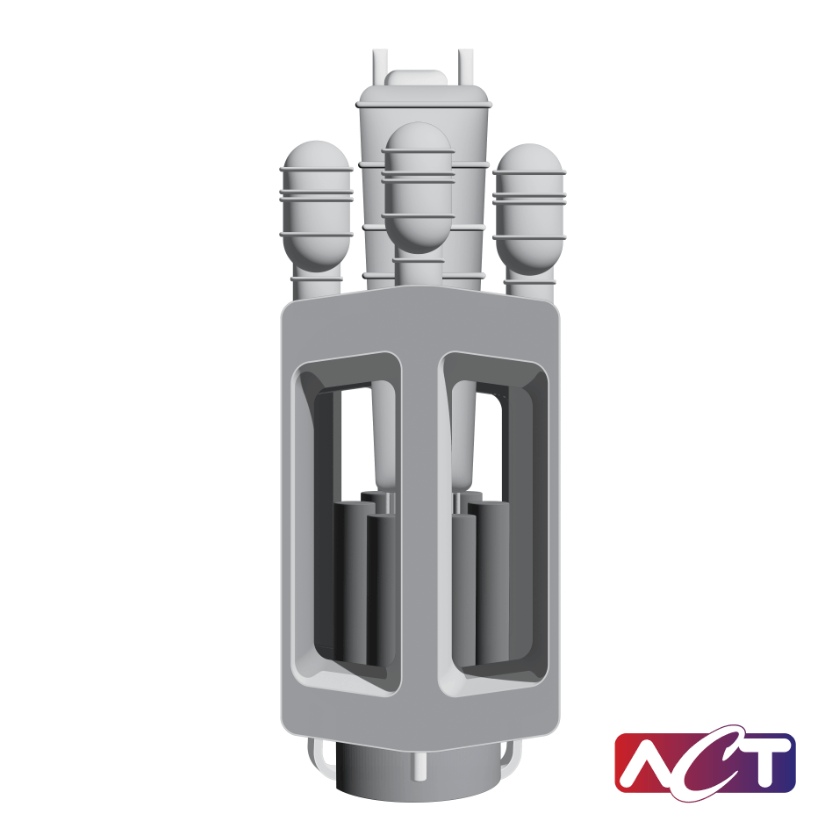
Advancements in Nuclear Energy Thermal Management: Small Modular Reactors (SMRs) / Microreactors
Small Modular Reactors (SMRs) were developed as an alternative to traditional nuclear reactor designs. Unlike PWRs, which require the use of an external cooling system or heat pump, SMRs can use passive heat solutions to pull heat away from the reactor core.
Here’s how they work: SMRs rely on the same principles as traditional nuclear reactors, but convert heat from nuclear fission to energy using heat pipe technology.
Heat Pipe Reactors
Heat pipes are devices that utilize the latent heat of vaporization to transfer heat. A heat pipe will begin operation once a temperature difference occurs between the evaporator and the condenser. This means that at any point the heat-producing source is hotter than the heat rejection sink, a heat pipe will move heat away. Most operate in temperatures from 20-150℃, which aren’t practical in the context of nuclear energy thermal management.
High-temperature heat pipes, on the other hand, can operate in temperatures ranging from 400-1100°C. The combination of Alkali Metal working fluid and stainless steel envelope makes them a more suitable solution for passive heat control in SMRs.
When high-temperature heat pipes are used in nuclear reactors, heat transfer from the reactor core to the heat exchanger becomes autonomous, which boosts safety and operation efficiency.
Heat Pipe Integration
The heat pipe is integrated directly into the reactor core then couples on the condenser with a variety of higher-level assemblies; including Brayton, Stirling generators or liquid loops.
In most SMRs the heat rejection takes place above the reactor which allows the heat pipe to operate with the assistance of gravity. This gives a greater flexibility on the overall length of the heat pipe and the reactor design. Newer heat pipe reactors have leveraged wicked heat pipes that allow operation in any orientation.
Benefits of SMRs
There are three primary benefits of SMRs: size, simplicity, and safety. As their name suggests, SMRs and microreactors are designed to be smaller. Their small-scale physical footprint allows them to be applied in remote or isolated locations where larger reactors are impractical.
Using passive heat exchange technology, SMR’s overall operation is simpler because they require no moving parts. That, paired with their smaller design allows for the product to be mass produced.
SMRs can be made in a factory and shipped directly to the installation location, helping to reduce production time and costs that would otherwise be required of traditional nuclear energy thermal management solutions.
All of these factors help reduce the risk of nuclear accidents. Active thermal solutions require human intervention, but passive solutions can regulate themselves. Therefore, the use of high-temperature heat pipes in SMRs can eliminate the threat of releasing radioactive materials into the environment for a safer, more efficient operation.
Find a Better Solution
ACT has over a decade of experience in developing nuclear energy thermal management solutions.