Reaching for the Stars – Advanced Cooling Technologies Wins 4 NASA Phase II SBIR Programs
ACT has a history of success through NASA’s SBIR Program (Small Business Innovative Research), developing many technologies in orbit today or being developed for future Lunar, Martian and deep space missions. ACT’s engineering and manufacturing pedigree has led to a track record in the space industry of increasing the Technology Readiness Level for both passive and active thermal management and control systems. ACT will look to replicate this success on the programs outlined below, all critical to future NASA missions.
Passive Two-Phase Thermal Management System for Hall Thruster
In the first project, “Passive Two-Phase Thermal Management System for Hall Thruster”, ACT will collaborate with the University of Michigan to develop a lightweight, compact cooling system using alkali metal heat pipes and advanced radiators. This will enable efficient thermal management of next-generation high-power density Hall thrusters needed for NASA’s deep space missions.
Phase II funding of $730,000 over 2 years allows the team to mature the technology for a high-power Hall thruster application. This is an extremely competitive NASA program, so winning a Phase II contract is a real testament to the hard work and innovation of the ACT team.
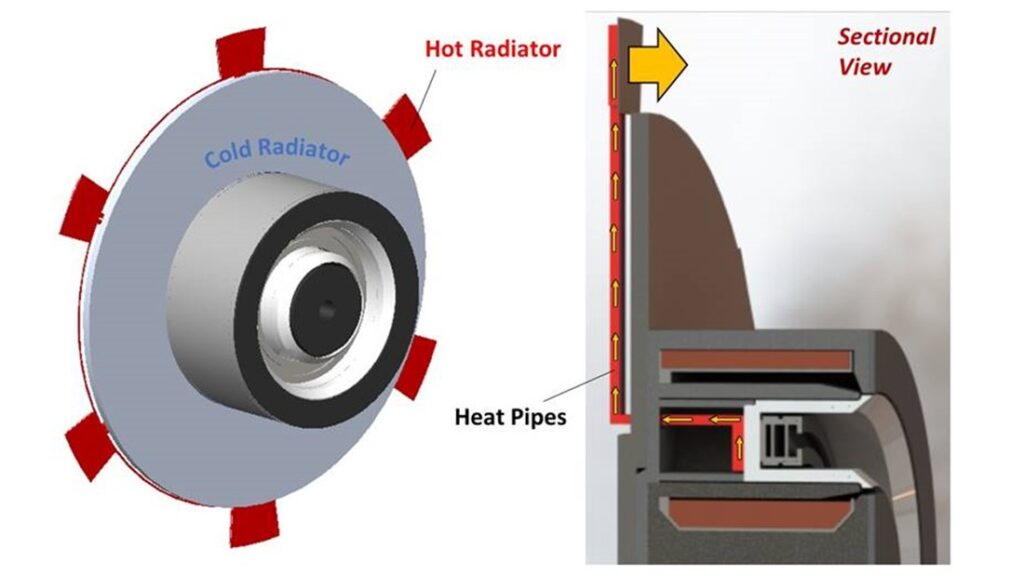
Hot End Thermal Management for Nuclear Electric Propulsion
The second project, “Hot End Thermal Management for Nuclear Electric Propulsion” will see ACT teaming up with Ultra Safe Nuclear Corp to develop a highly reliable heat pipe-based thermal management system to transport thermal energy at megawatt scale, between the nuclear reactor and the hot end of the power conversion system, for nuclear electric spacecraft propulsion.
The team at ACT will build upon their Phase I work, enabling long-duration deep space exploration. The goal is to provide reliable, passive heat transfer that can operate at the high temperature and power levels needed for nuclear electric spacecraft. Some key features of the design include:
- High-power sodium heat pipes to extract and transport thermal energy from the reactor
- Modular heat exchangers that transfer heat to the propulsion system
- A startup loop to help initialize heat pipe operation from a frozen state
- A shield to minimize heat losses during operation
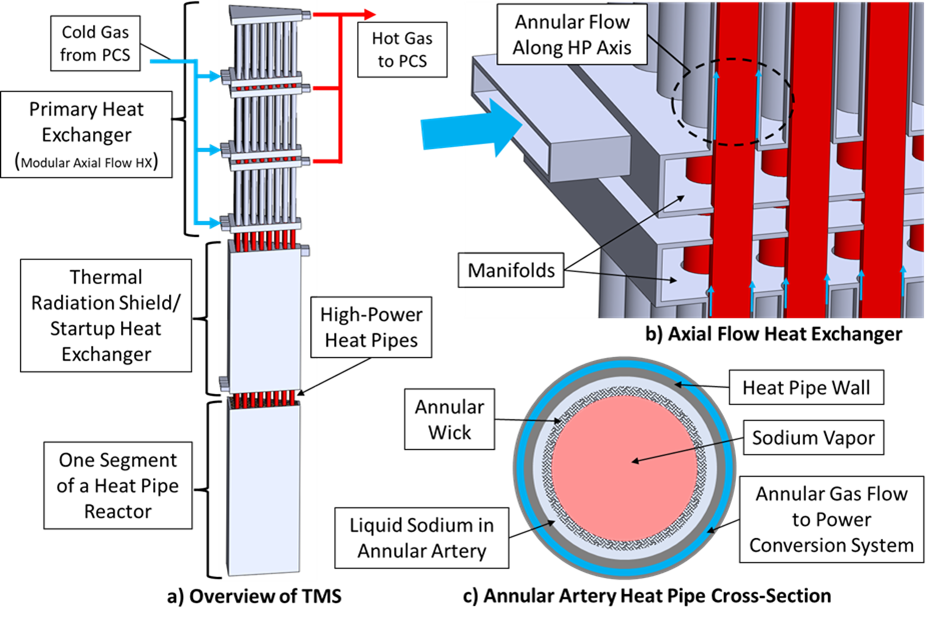
Hybrid Manufacturing Process of Loop Heat Pipe Evaporator
For the third project, “Hybrid Manufacturing Process of Loop Heat Pipe Evaporator”, ACT’s goal is to eliminate the fragile knife-edge seal component used in conventional loop heat pipe production. Instead, ACT will use a combination of additive manufacturing and traditional methods to create a robust integrated sealing structure.
By using direct metal deposition additive manufacturing techniques, ACT can rapidly prototype and manufacture loop heat pipe evaporators without labor-intensive and risky seal assembly. This improves reliability and reduces lead time and cost.
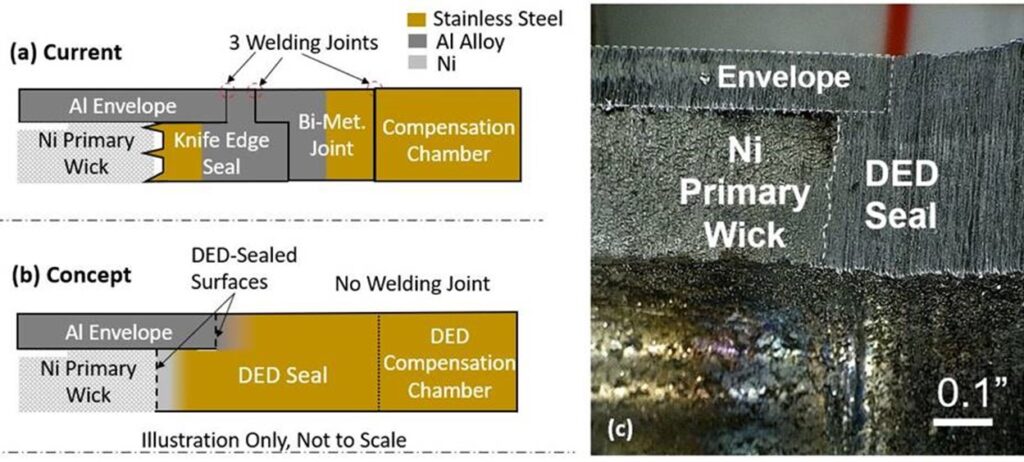
Novel Vapor Chambers for Advanced Sorption Systems
Lastly, the fourth project “Novel Vapor Chambers for Advanced Sorption Systems”, sees ACT developing novel vapor chamber technology for the International Space Station’s carbon dioxide removal system. The current CO2 removal system for the ISS has been operating for over 30 years but suffers from issues like high power consumption, dust contamination, and non-uniform temperatures.
ACT’s vapor chamber concept aims to address each problem:
- Combining heating and cooling functions reduces power needs
- Direct integration with a 3D printed sorbent bed prevents dust
- Isothermal vapor chamber fins improve temperature uniformity
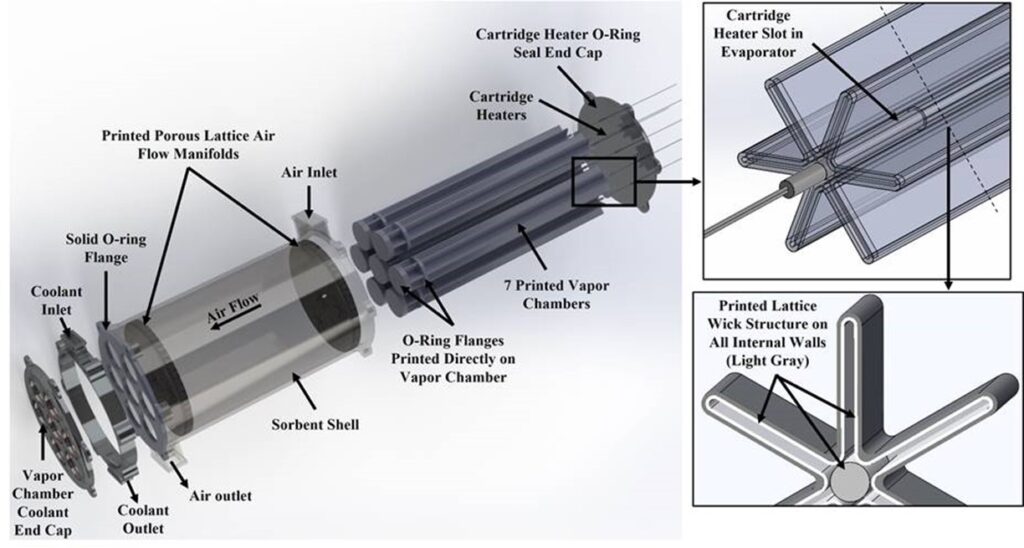
Learn more about ACT’s Spacecraft Thermal Control products and visit our Research & Development section to see what we’re working on now.