The Importance of Thermal Management in Electric Vehicle Chargers
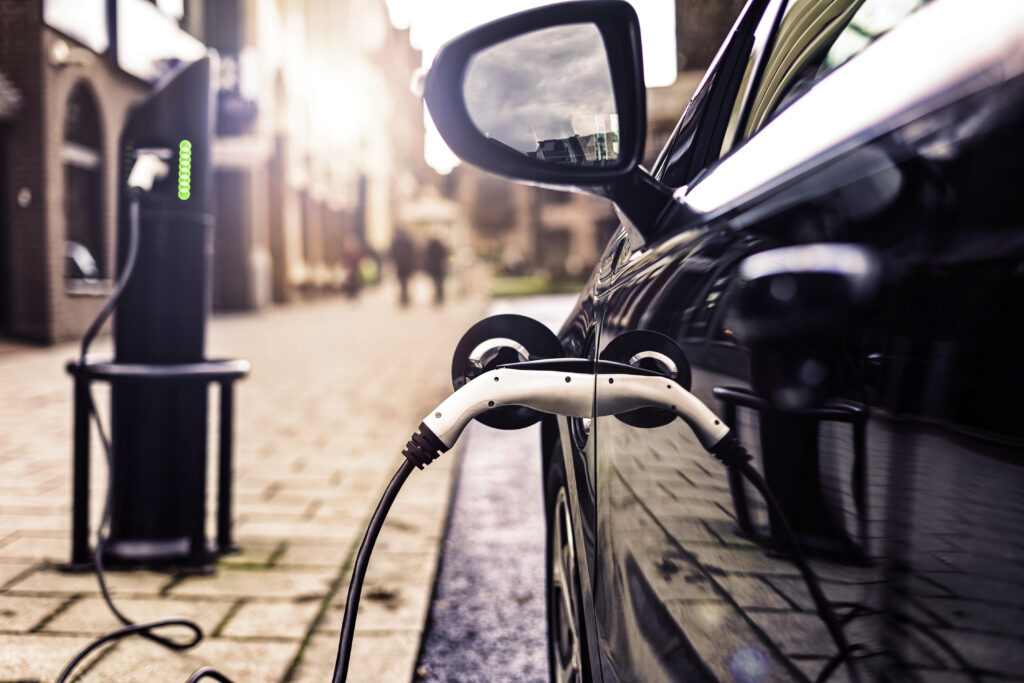
In 2023, the United States government took a decisive step towards shaping the future of electric vehicle (EV) infrastructure, emphasizing the necessity for rapid and dependable charging stations. Despite the growing interest in electric vehicles, their user base remains a minority, with charging speed and availability standing out as critical limiting factors. Recognizing the urgency of addressing this issue, the legislature has allocated significant funding to confront this global challenge head-on. However, amidst this progress, a series of consequential challenges persist, chief among them being thermal management.
As the demand for EV charging accelerates, so too does the generation of heat, posing a significant hurdle to overcome. Early models relied on conventional off-the-shelf air cooling strategies, yet the escalating heat densities and the diverse climates and conditions across the nation render such methods increasingly inadequate. Addressing the thermal management of charging infrastructure is imperative to ensure its resilience and effectiveness in meeting the demands of an evolving transportation landscape.
Why should the ev market care about thermal management?
As power electronics handle greater loads, the resistance in transferring heat from the electronics’ core (junction) to their external packaging (case), exemplified by components like Insulated Gate Bipolar Transistors (IGBTs), becomes more pronounced. With this rise in resistance, the thermal management solution faces the arduous task of dissipating the same amount of power while operating within a reduced thermal budget – the temperature difference between the electronics packaging and the surrounding ambient air. Consequently, as the demand for faster charging intensifies and the infrastructure evolves, the imperative for more efficient thermal management solutions becomes increasingly pressing.
Typical Thermal Management Challenges being discussed in the EV Market
There are significant discussions and collaboration between component providers, system integrators and vehicle manufacturers on a variety of issues, summarized below. This blog will talk through all the areas specific to the thermal management within the charging station itself and not specific to the vehicle.
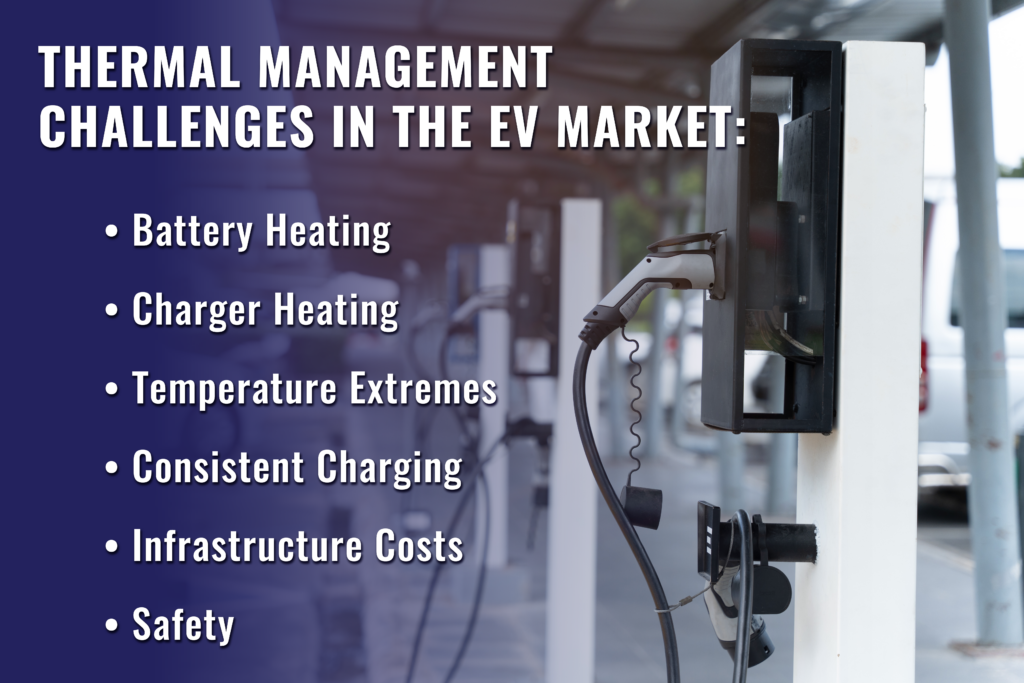
- Battery heating – Fast charging can cause a large temperature rise in the battery pack, which needs to be carefully controlled to avoid damage. The cooling system needs to dissipate a lot of heat in a short period of time, during fast charging.
- Charger heating – The power electronics in the charging station itself also generate significant waste heat that must be managed. Fast chargers require robust cooling systems for these components.
- Temperature extremes – EVs need to be able to charge quickly in very hot or extremely cold conditions, which makes thermal management more difficult compared to moderate temperatures. Battery performance and charging speed can degrade at temperature extremes.
- Consistent charging – The charging power may need to be reduced if the battery gets too hot, so thermal management is important to maintain consistent charging speeds and avoid interruptions.
- Infrastructure costs – Large cooling systems add cost and complexity to charging stations. Effective thermal management is needed to minimize the infrastructure requirements.
- Safety – Batteries can be damaged or even catch fire if overheated. Effective thermal management is critical for safety.
thermal management options for ev charging stations
Once you understand your challenges, waste heat loads and environment you can begin considering options:
- Sealed Enclosure Cooling: ACT’s enclosure cooling products effectively dissipate heat from inside the charging station using circulated air cooling. These are usually the first option since they are cost-effective and off-the-shelf designs. Unlike a traditional fan filter combination, ACT’s Enclosure Cooling Product Line all offer NEMA rated seals to not only cool the inside of the cabinet, but also keep it safe from dust, water, etc. There are several product SKUs available with various cooling capacities and above ambient vs air conditioning options. For best understanding of product fit for your application, please use our online calculator and reach out if you’d like additional engineering support. If the calculator doesn’t provide an option, don’t worry a custom approach can still solve your EV station thermal objectives…
- Loop Thermosyphon: This is another air-cooled offering; however, it locates the evaporator at the source component(s) to create a direct cooling approach and ultimately lower thermal resistance from the power electronics case to air. This is one of the hidden gems of the thermal management options because it is orientation dependent (requires gravity return of the liquid), making it unsuitable for most applications and the loop operation to increase capacity is not often considered. EV charging stations typically could locate the air-cooled condenser at the top of the cabinet, making this an ideal fit for this industry. With ample capacity (demonstrated > 50kW air cooled heat rejection), flexible packaging options and extremely low thermal resistance (< 0.005 W/C) it offers the highest capacity above ambient air-cooled option for EV charging stations. Even more important than thermal performance is the high reliability and low energy consumption (completely passive operation), making it a cost-effective option considering life time ownership and implementation costs.
- Liquid Cooling: The next logical progression is to alter your cooling strategy from passive air cooling to active liquid cooling. This requires higher energy consumption and pump maintenance but allows for a higher EV station power density (waste heat). EGW or other low freezing point water mixtures offer high heat transfer capabilities and are relatively well understood. They do offer some safety concerns when combining water with medium to high voltage applications, but strategic implementation and isolating the liquid loops from the power electronics is often utilized to mitigate risk.
- Pumped Two-Phase Cooling Systems: Two-phase liquid cooling systems utilize the latent heat of vaporization to efficiently remove heat from electronic components. Primarily refrigerant based, P2P offers similar cooling capabilities to single phase water solutions but a higher degree of intrinsic safety and lower energy consumption since the performance is based on the boiling effects and not the fluid velocity (fractional pump power required). While this technology is more emergent than mainstream, P2P is becoming a more popular technology in Power Electronics systems such as EV charging stations as well as other high power density racks such as data centers.
exploring act’s range of thermal management solutions
ACT’s comprehensive range of thermal management solutions provides options suitable for a wide range of power density requirements, from low to high. Whether it’s sealed enclosure cooling for moderate power densities or advanced Pumped Two-Phase cooling systems for high power density applications, ACT offers innovative solutions to address the thermal challenges faced by the EV charging industry.