Vacuum Brazing in Thermal Management
what is vacuum brazing?
Vacuum brazing is an increasingly popular joining technique used by companies to manufacture high-quality thermal management products. The process involves joining materials in a controlled environment with low pressure and absence of air, ensuring a clean and contaminant-free bond. The key benefits of vacuum brazing include the ability to create strong, clean joints between dissimilar metals, minimize oxidation, and precisely control the brazing environment. By brazing in a vacuum, manufacturers can avoid flux contamination while still accessing the high temperatures needed to create robust brazed joints. The controlled atmosphere also allows for very even heating and minimizes the potential for defects. This results in components with enhanced mechanical strength, improved thermal conductivity, and excellent resistance to corrosion and oxidation.
industries benefiting from vacuum brazing
In the aerospace industry, for instance, vacuum brazing is employed to create robust components that can endure the rigorous conditions of high altitudes, rapid temperature changes, and extreme vibrations. Automotive manufacturers utilize this technique to produce heat exchangers and other thermal management components that enhance the efficiency of vehicle systems while withstanding demanding operating conditions.
In the defense sector, where equipment often operates in challenging environments, vacuum brazing ensures the production of ruggedized hardware capable of maintaining optimal performance even in harsh climates or during intense usage. Similarly, in the electronics industry, vacuum brazing is employed to create durable electronic assemblies with improved heat dissipation, ensuring the reliability of electronic devices under various operating conditions.
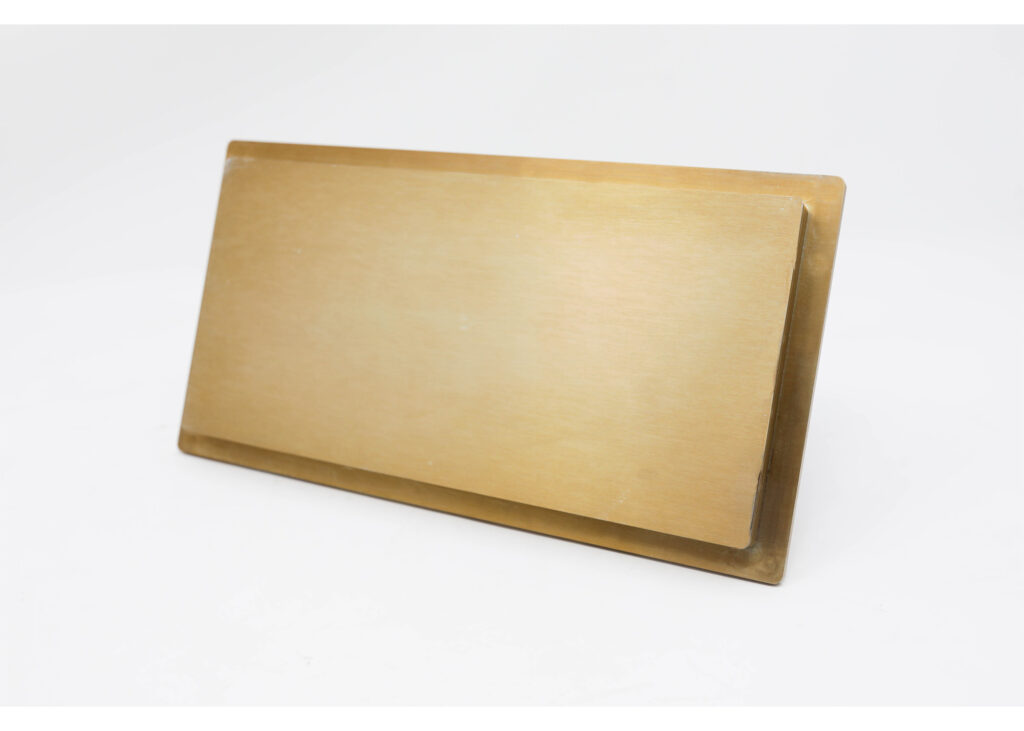
aluminum brazing vs. Other Metals
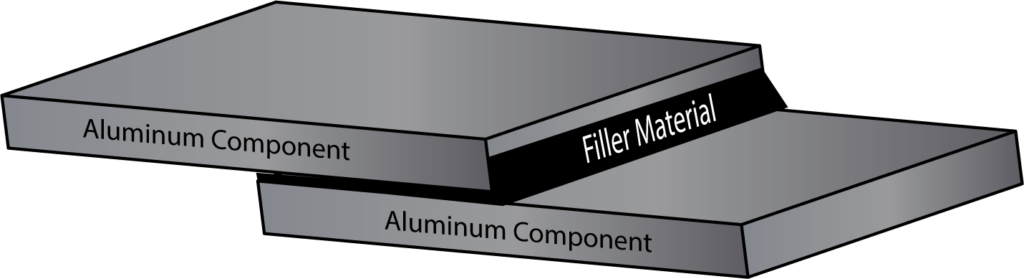
Vacuum brazing processes can be broken into two general categories; aluminum brazing, and other metals. Aluminum brazing is unique for a few reasons. First, the aluminum oxide layers form rapidly, even at room temperature, and the magnesium in most alloys of aluminum will vaporize at brazing temperatures, which will contaminate a furnace if it is used for other metals. Dip brazing or CAB brazing of aluminum uses a flux to break down the aluminum oxide on the parts, enabling wetting of the braze alloy. The use of flux is not preferred on parts with internal features as it is impossible to remove the flux once it is brazed.
vacuum brazing for joint strength and impermeability
Vacuum brazing produces exceptionally strong joints, which are hermetically sealed, meaning they are completely airtight and impermeable to gases or fluids. This is crucial in many applications, where the structural integrity and durability of components and assemblies are paramount, especially in extreme operating conditions and high-stress environments. It’s highly desirable for many different types of equipment, such as aerospace components, electronic enclosures, or specialized containers that require protection from external elements, such as moisture, corrosion, or contaminants.Vacuum brazing offers precision control over the brazing process, allowing for exact positioning and distribution of the filler material, resulting in uniform bonding across the entire joint face. This minimizes the formation of defects and weak spots and can be carefully optimized to achieve extremely tight tolerances.
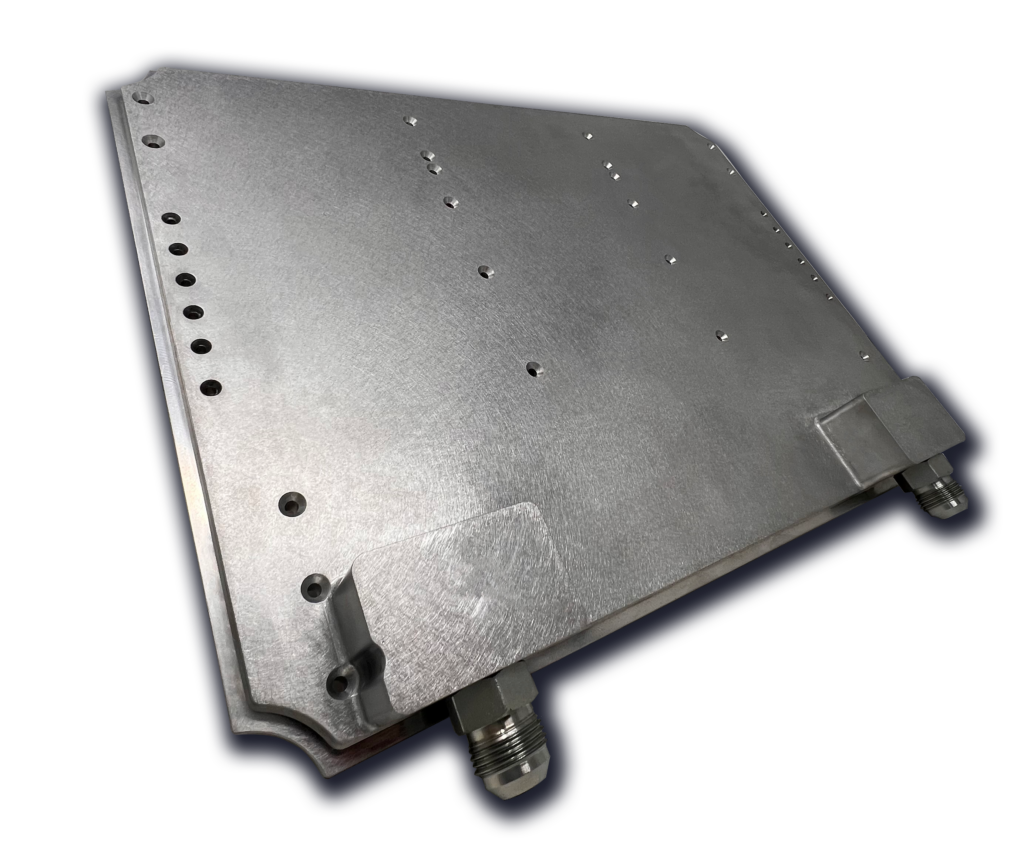
Design considerations for manufacturable and braze-able assemblies
There are a number of steps that must happen to make a successful vacuum brazed part. First, the assembly must be designed in a way that is manufacturable and braze-able. Since the brazing operation is a thermal process, part thickness, joint placement, and joint design must be taken into consideration to ensure the braze material melts and solidifies uniformly to create the desired join. The brazing process happens near the melting point of most aluminum alloys, which results in the parts being completely annealed, and soft, post-braze. To overcome this, the parts must then be quenched to bring them back up to sufficient mechanical properties. The quench rate corresponds to the mechanical properties, but also the stresses induced on the brazement. These stresses reveal themselves during the post-braze machining operations that are used to true-up surfaces and final part dimensions. If not done properly the part may cup, curl, or warp out of tolerance once removed from the machining vise.
precise control for optimal performance
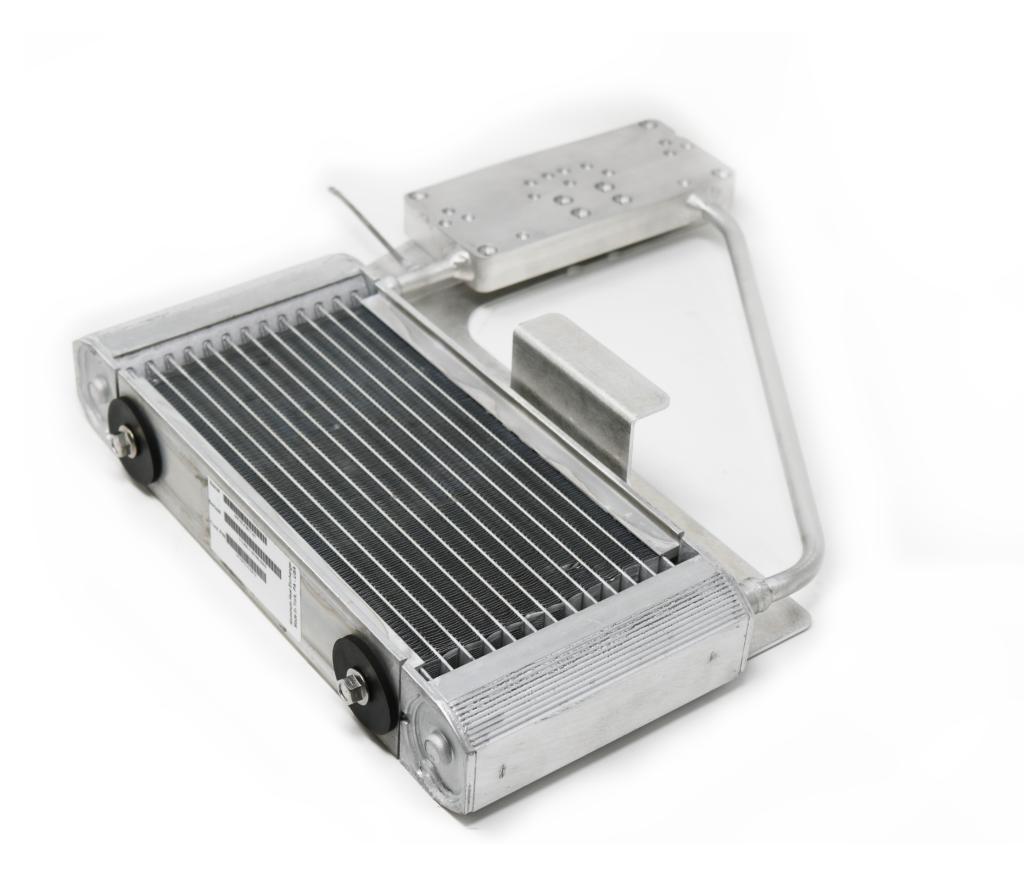
Vacuum brazing is an advanced joining technique that produces exceptionally strong, impermeable, and uniform joints for demanding applications across industries like aerospace, automotive, defense, and electronics. While the process requires careful design considerations and process controls, the result is high-performance components able to withstand extreme operating conditions. With its unique capabilities and precision control, vacuum brazing will continue growing in popularity as manufacturers seek innovative solutions to manufacture rugged and reliable products. The future looks bright for this versatile manufacturing process as more industries recognize its potential for creating robust and durable hardware