The traditional process for Loop Heat Pipe (LHP) evaporator fabrication is labor-intensive due to complex manual steps such as wick fabrication, vapor groove cutting, and wick-envelope integration. These steps contribute to high costs and extended lead times, particularly in the case of small evaporators for mini loop heat pipes, due to the added challenges posed by small-scale manual fabrication. An innovative 3D printed solution was therefore needed to significantly reduce the manufacturing costs of evaporators in order to make the system financially viable for use on SmallSats and in particular, CubeSats.
Problem
ACT has been conducting an R&D campaign aimed at creating 3D printed evaporators for Loop Heat Pipes (LHPs) funded through the NASA SBIR program. With 3D printing, the entire evaporator is fabricated in a single operation, complete with such features as the wick, solid envelope, and vapor grooves, thereby eliminating the need for complex manual steps in evaporator fabrication. This innovation amounts to over an order-of-magnitude manufacturing cost reduction and significant time savings as compared to the traditional fabrication process.
As one of the primary components of this R&D effort, the 3D printed evaporator build parameters are optimized to improve wick pore size and the associated capillary limit. A high capillary limit is, in turn, crucial to achieving the desired power limit of the LHP. The optimization process follows an iterative routine which has been successful so far in reducing the maximum pore radius from over 8.5 μm (Sample 1) to under 5 μm (Sample 4) in just four iterations, as shown in Figure 1.
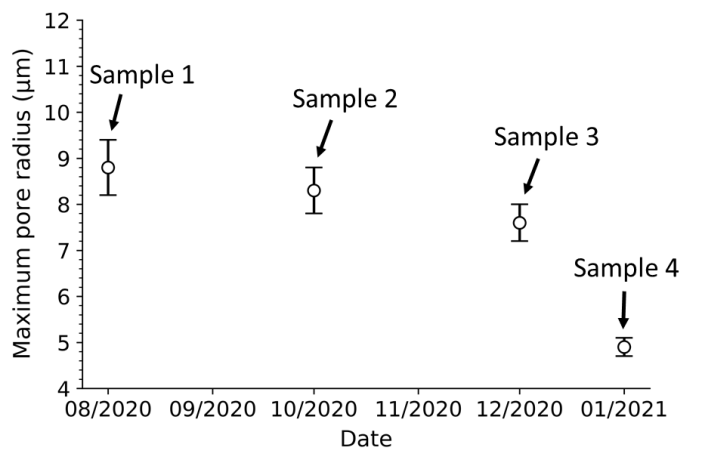
Solution
With the current best build parameters, several 3D printed evaporators of varying sizes were fabricated, shown in Figure 2, and tested across a range of input powers, condenser temperatures, and working fluids. A sample test data for a 4-inch-long evaporator is presented in Figure 3. In this test, the Loop Heat Pipe (LHP) was subjected to a maximum power of 350 W, which, as seen from Figure 3, is well within the power limit of the system. Additional testing is planned at higher input powers and even lower condenser temperatures. As a particularly noteworthy development, a full Loop Heat Pipe (LHP) architecture with a 3D printed evaporator was designed and fabricated to mission-specific demands for thermal management on NASA’s Volatiles Investigating Polar Exploration Rover (VIPER). The goal of this system was to effectively transfer heat from one or more of the scientific instruments to the radiators onboard the lunar rover. The system thus developed was tested successfully in reflux orientation in the laboratory to emulate the near-vertical operation in lunar gravity.
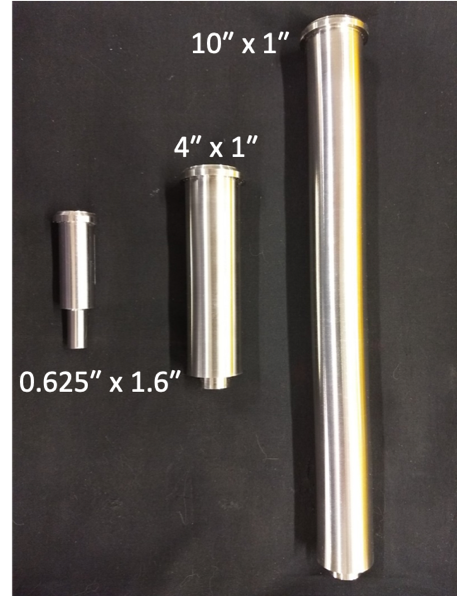
Current efforts are directed to the development of advanced wick structures that can go beyond the performance of traditional wicks and improvement of the overall thermal conductance of the system. Further details on the work completed so far can be found in the following reference:
Gupta, R., Chen, C-H., and Anderson, W.G., “Progress on 3D Printed Loop Heat Pipes.” Proceedings of the 50th International Conference on Environmental Systems, ICES-2021-154, 2021. (Technical Paper: Progress on 3D Printed Loop Heat Pipes)
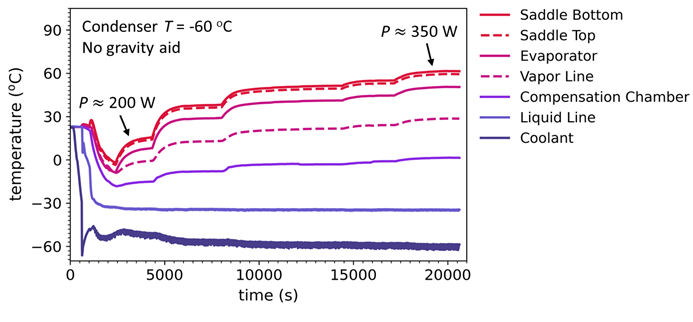
Customer Impact
Evaporator fabrication using 3D printing leads to lower manufacturing costs, with current estimates indicating an order-of-magnitude cost reduction as compared to the traditional fabrication process. 3D printed evaporators are also associated with a significantly smaller lead time as compared to a traditional evaporator.
What is the impact on the spacecraft industry?
3D printed evaporators enable the fabrication of low cost and low lead time mini loop heat pipes that are well-positioned to meet the thermal management demands of the ever-growing SmallSat industry, particularly CubeSats, that are used for both research and commercial purposes.