Advanced Cooling Technologies, Inc. (ACT) designs, develops and fabricates custom hardware for testing and experimental purposes. One unique apparatus was developed for the Air Force to evaluate the thermal behavior of fabrics subject to convective and radiative heat loads as well as open flames. The hardware provides an automated capability in which the user simply inserts test samples, which themselves are instrumented with temperature sensors woven into the fabrics, inputs testing conditions (radiant heat flux, convective heating, combined radiative and convective heating, open flame exposure) and starts the test. Spatio-temporal temperature and flow measurements are then acquired and displayed in real-time. Also important is that the hardware was developed to allow for testing against established test standards, which in this application were ISO 17492, ASTM D 4108-82, ASTM F 1939-99a. With this testing capability, the military can now accelerate the evaluation and deployment of high-performance fabrics and reduce lead times and costs. Other applications of the hardware include its use for the development of personal protective equipment (PPE) for firefighters and first responders, airbag fabric design and development, personal cooling garments and a tool for thermal injury assessment and analysis. A picture of the test hardware developed at ACT is shown in Figure 1.
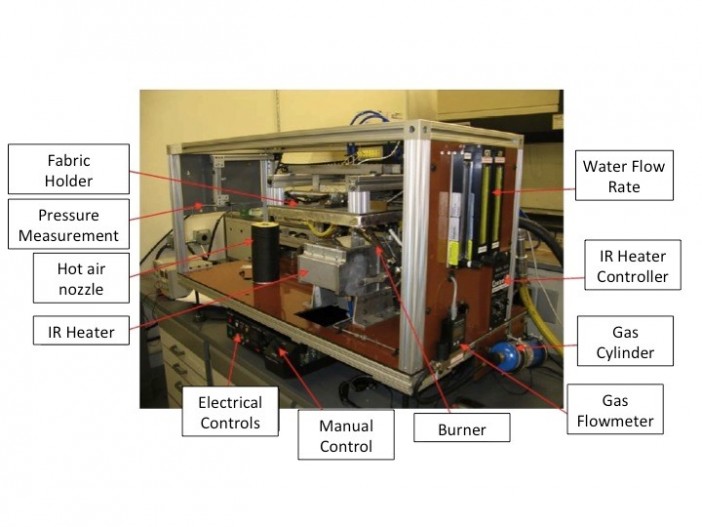
To supplement the hardware, a detailed finite volume based fabric model was also developed to compute the transient thermal profile within the porous fabric subject to hot gas impingement, radiative heat loads and other thermal input conditions. The model includes the thermal input, flow and thermal transport within and through the fabric (incorporating fabric material properties, permeability, etc.) and coupling to a burn injury model developed by the military to compute the extent of burn injury based on empirical correlations. A separate test apparatus was also developed at ACT for experimental determination of the fabric permeability as a function of temperature and flow conditions. A top-level schematic of the model is shown in Figure 2.
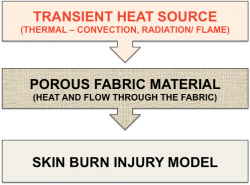
Transient measurements of the temperature and flow speed were acquired and heat transfer rates computed. The detailed model was compared and validated against the experimental results. Moreover, both experiment and model were extended to multi-layer fabrics and the inclusion of water/ vapor transport through the fabric has received recent attention to improving model predictions.