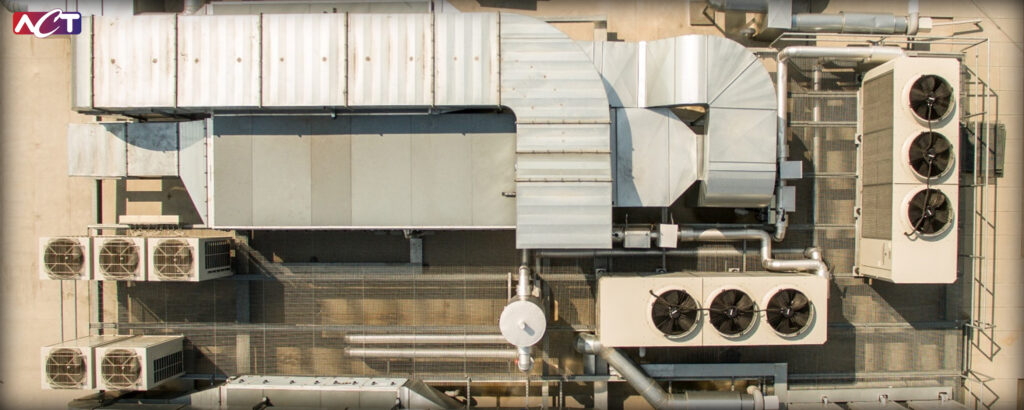
Cleanroom challenges
3M Korea designs state-of-the-art microscopic chips, which are integrated circuits made of semiconductors. Semiconductors are the fundamental component of smartphones, TVs, autonomous vehicles, and many other electronic devices. 3M’s processing plant encountered costly cleanroom issues due to inconsistent cooling and humidity levels. In some instances, the air conditioner’s chilled water system could not keep up with the heat load being produced during semiconductor manufacturing. Semiconductor processing requires a precise, climate-controlled manufacturing environment to produce a consistent quality for the microchips. Two types of cooling systems were present: DX and chilled-water systems. The cleanroom air handling units (AHUs) required expensive electric reheat to bring dry, neutral air to the cleanroom space. 3M was also concerned with reducing energy costs to lower their carbon emissions, and was looking for some form of HVAC energy recovery system.
HVAC Energy REcovery: The Wrap-around solutioN
ACT’s Korean HVAC Representative, HPE Engineering, evaluated an approach to enhance the cleanroom’s low-performing air conditioning system.
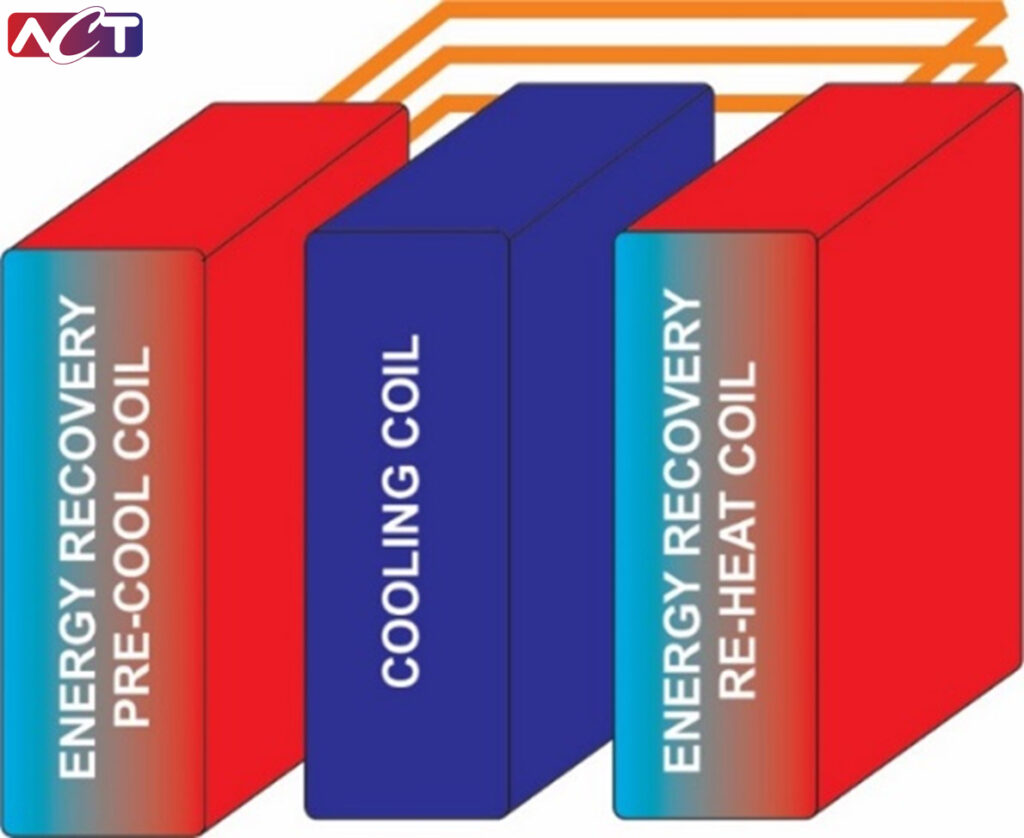
The decision was made to install multiple ACT Wrap-Around Heat Pipe Heat Exchangers (WAHX) configured for both DX and chiller-water systems. The WAHX HVAC energy recovery system (made up of a precool coil and a reheat coil) wraps around the chilled water coil and operates passively, with heat transfer being accomplished via gravity-aided thermosyphons. The precool coil (evaporator) is designed to reduce the incoming air temperature by 4.4°C (7.9°F) at standard operating conditions. The second WAHX reheat coil (condenser) adds 4.4°C (7.9°F) of reheat to deliver dry, neutral air to the cleanroom.
The WAHX’s passive heat-transfer method has virtually zero thermal resistance, as heat pipes are over a thousand times more thermally conductive than copper.
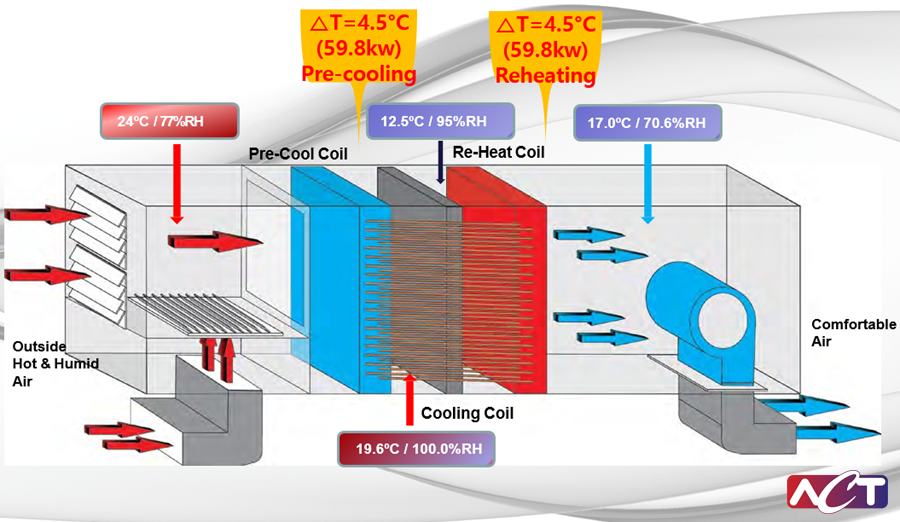
The AHUs’ reheat coils were previously performing the heat transfer process. Since installation of the ACT WAHX HVAC energy recovery systems, the reheat coils are rarely activated, and the passive heat transfer process of the WAHXs has resulted in thousands of dollars of energy savings. The project consisted of nine AHUs ranging in size from 8.6 m3/s (18,220 CFM) to 22.3 m3/s (47,250 CFM). The above graphic shows the precooling and reheat savings expressed in Kilowatts. The total power savings per unit was 119.6 kW, which is the combination of the precool and reheat power savings. Assuming full-load operation, each system saved around 1,050,000 kWh of energy per year. The WAHX energy recovery systems reduce humidity in the manufacturing space and deliver dry, neutral air to the process. The WAHX cleanroom AHU energy recovery systems also increase the capacity of the AHUs by requiring less chilled water to maintain stable manufacturing temperature conditions.
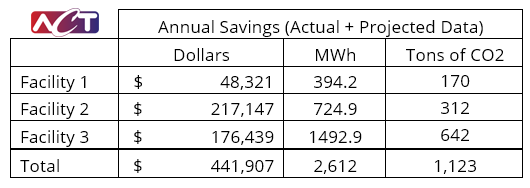
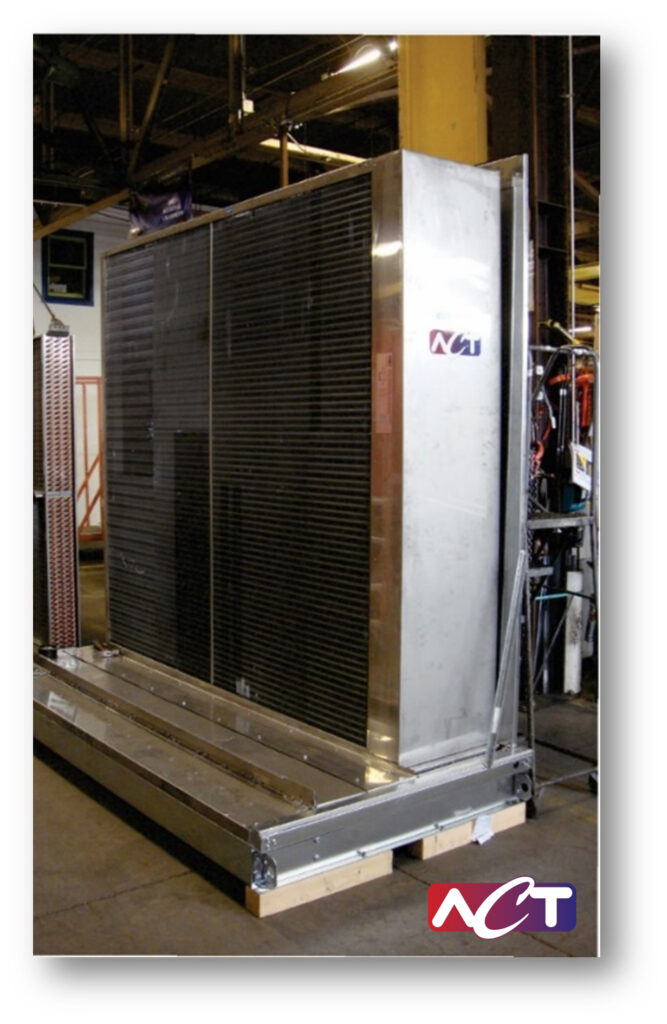
Positive Results Lead to Future Endeavors in HVAC Energy Recovery
Based on 3M’s post-installation data, the ACT WAHX energy recovery systems returned approximately $320,000 in 2023. Since 2023 was not a full year of operation, 3M is anticipating a total saving of $440,000 for all of 2024. The total payback period (including installation cost) is projected to be under two years for this cleanroom AHU energy recovery system.
Through the implementation of these wrap around heat exchangers, the production facilities reduced the load on their heating and cooling system by 35% and saved over 2.6 million kWh in one year of operation. 3M was also able to reduce their carbon footprint by over 1,100 metric tons, opening the door to more efficient and environmentally friendly energy usage. Based on the positive installation results, 3M is now considering additional ACT-WAHX installations for plants located in Japan, China, Taiwan, USA, and the EU.
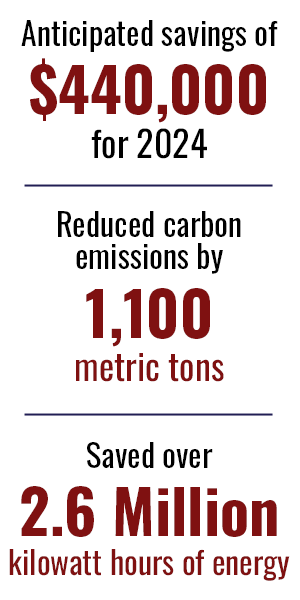
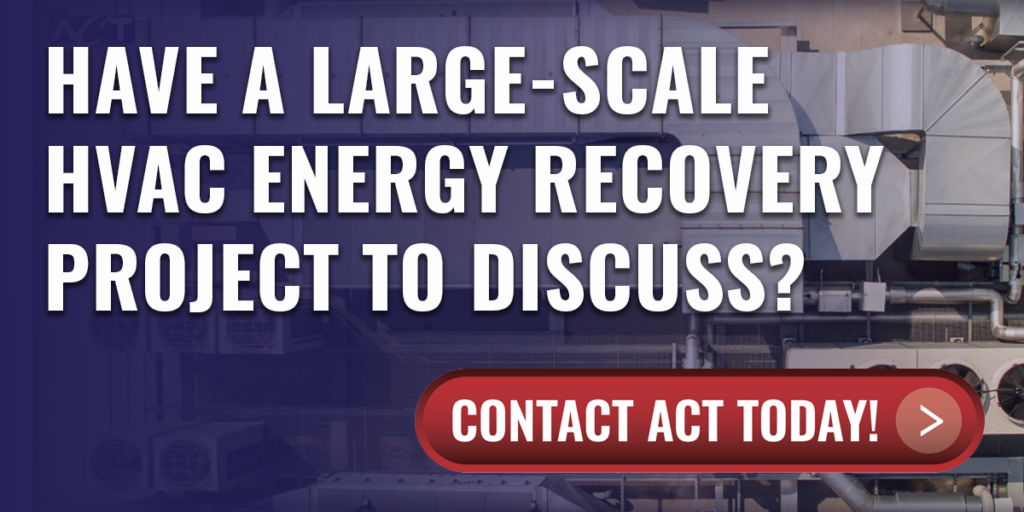