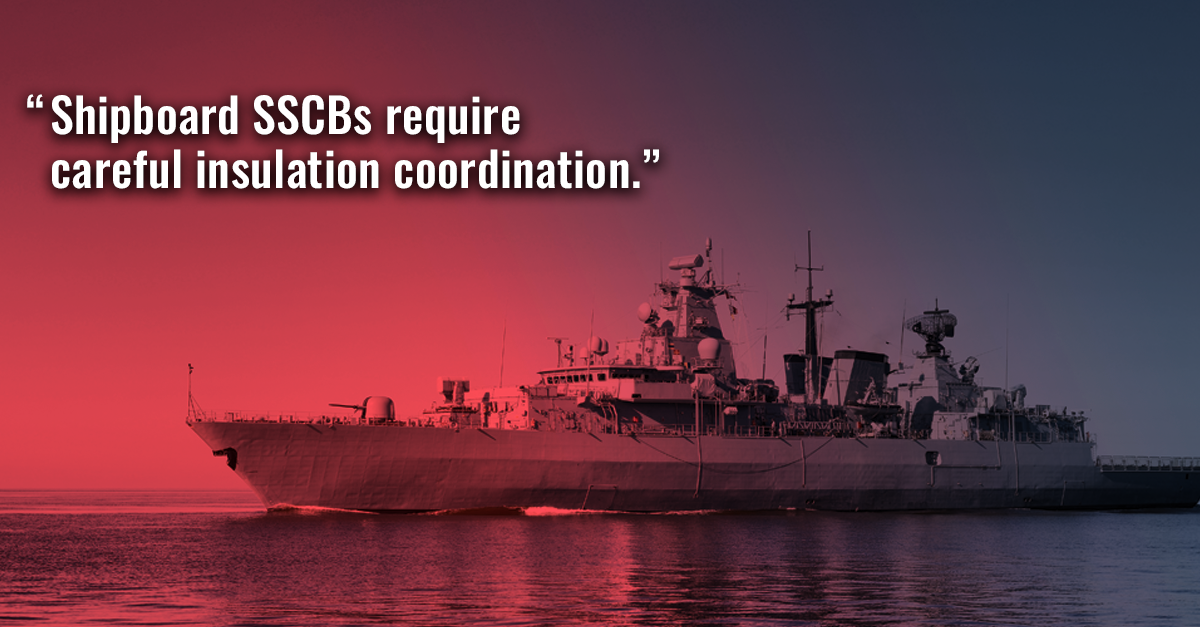
For a variety of environmental factors, marine vessels pose an interesting challenge for engineers when it comes to the technical logistics of shipboard operations. This is especially true of a vessel’s power system, where the strict requirements for efficiency and power density result in a preference for direct-current (DC) systems over alternating-current (AC) systems.
However, the implementation of such a system is complicated by the extremely fast total interruption time of DC power; so, a medium voltage, DC solid-state circuit breaker (SSCB) is needed to limit fault currents and interrupting faults. Due to the confined nature of marine vessels, limited space is available on shipboard systems, and SSCBs, therefore, need a very high volumetric power density, which requires careful insulation between the semiconductors and other components in the system. Likewise, the lack of semiconductors with sufficient voltage ratings in a given system necessitates that several semiconductors be connected in series within the SSCB, further complicating the feasibility of cooling these semiconductors.
Problem: Strict Efficiency and Operational Requirements
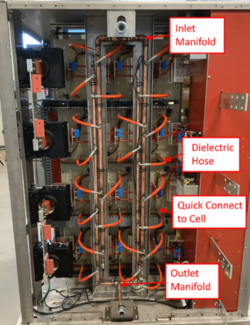
Recognizing the challenges that a shipboard power system faces, Eaton Research Labs asked ACT to partner with them on developing a novel cooling solution for their unique SSCB. The following requirements were given for the cooling solution:
- Ensure high efficiency and power density
- Maintain uniform temperatures across the arrays of semiconductors
- 40 kV voltage isolation between the cells in the modular architecture
Solution: Custom Pumped Two-Phase Enabler
Given the requirements, ACT’s engineers decided that a pumped two-phase (P2P) loop would be the most effective way to uniformly cool the cells. In this version of a P2P solution, the coolant is distributed to the cells in a parallel flow configuration, and the cooling plates in each cell are designed so that the coolant evaporates in the channels while remaining two-phase, ensuring maximum efficiency.
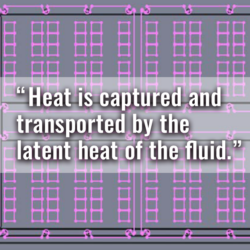
The temperature is kept constant by maintaining a low pressure drop in the cooling areas; since the fluid has both liquid and vapor phases together, the temperature and pressure are bound together by the fluid’s saturation curve. Heat is captured and transported by the latent heat of the fluid; this greatly reduces the flow rates required to maintain target temperatures as compared to a liquid cooling system, which would only utilize the sensible heating of the fluid.
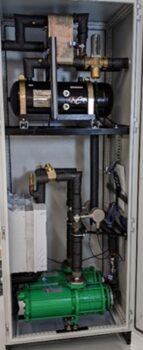
An important feature of this system is that the fluid used is a dielectric. Additionally, non-conductive hoses were used in the manifold to meet the required voltage isolation requirements.
In addition to a uniform flow distribution, an important feature of the manifolds is the low-loss, blind-mate, quick-disconnect terminals. These allow the cells to be plugged in and out—or replaced—without affecting the functionality of the system.
ACT and Eaton engineers published a joint paper describing the system in further detail:
Slippey, Schroedermeier, Folts, Pellicone, and Rockhill. “Pumped 2-Phase Cooling as an Enabler for a Modular, Medium-Voltage, Solid-State Circuit Breaker.” PCIM Europe, Digital Days. May 2021.