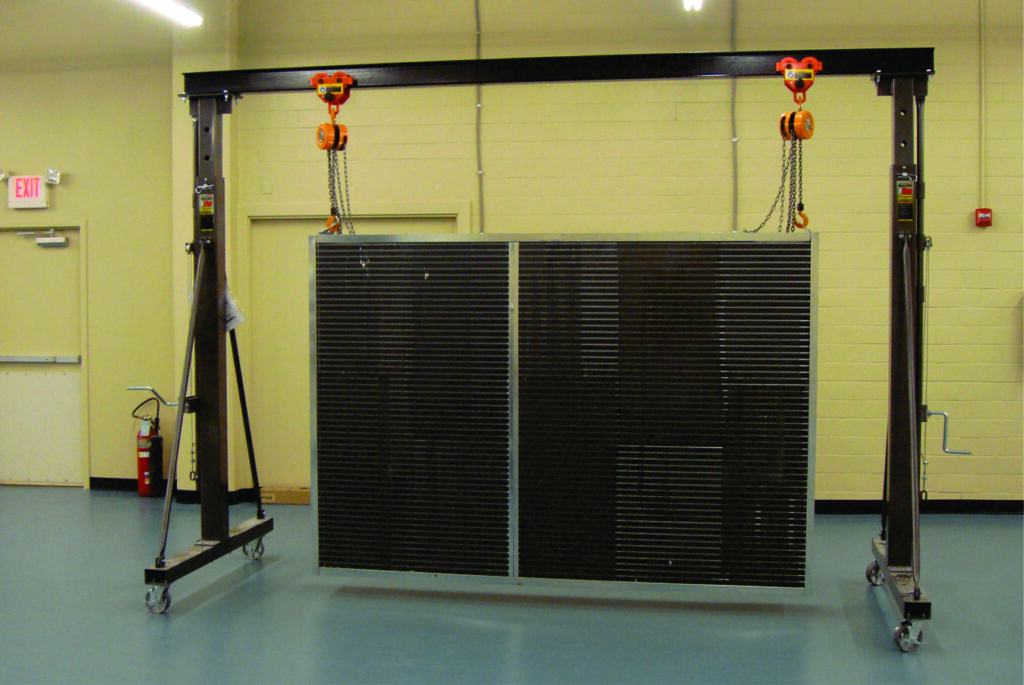
A well-established Asian air handling company wanted to provide cost saving energy recovery at a large KAL resort hotel. An air to air heat pipe heat exchanger (AAHX) was designed and built to pre-cool the incoming ventilation air with conditioned exhaust air. Up to 10,000 cfm of incoming outside air at 95°F was pre-cooled to 67.6⁰F prior to being processed by the active air conditioning system. The targeted temperature effectiveness was 80%. In other words, the AAHX was designed to transfer 80% of the temperature difference between the incoming air and the exhaust air streams.The overall size of the AAHX was approximately 6ft. wide x 8.5ft tall. ACT’s AAHX is installed vertically with the warm incoming airstream ducted through the lower section and the cooler exhaust airstream ducted through the upper section. The two airstreams are completely isolated, by a sealed partition, with no potential for cross contamination.
Energy Recovery: Based on the 80% sensible effectiveness, the incoming warm airstream can be pre-cooled from 95°F to 67.6°F. This reduction in entering air temperature generates a saving of over 295KBtu/hr at the system design point of 95° F. See the specific calculations below:
Effectiveness = 0.80 = 10,000 cfm * (95°F – X°F)/10,000 cfm * (95°F-60.8°F) X = 27.4° F
(warm stream ∆T) 95° – 27.4° = 67.6 °F
Sensible Air Cooling (Btu/hr) = 1.08*Flowrate (cfm)*∆T(°F) 1.08*10,000 cfm*27.4°F = 295,920 Btu/hr
Savings Potential:
Let’s convert the 295,920 Btu/hr energy savings to dollars. The hotel is located in a major metropolitan area, with an estimated cost of electricity at $0.15/kWh. At the design point, energy recovery savings are approximately $104.40/day. A 24 hour/day system operation daily savings calculation is shown below.
295,920 Btu/hr = Energy Savings 295,920 Btu/hr *.2931 W/Btu/hr / 3 (COP of active cooling system) ≈ 29 kW x 24hours/day *$0.15/kWh = $104.40/day
The estimated payback period for the AAHX heat pipe heat exchanger, depending on probable hours of operation, is under one (1) year.
Meeting the Design Specification:
ACT performed a prototype study to meet the design requirement of 80% temperature effectiveness. The physical dimensions of the heat exchanger, airflow rates, entering and exiting temperatures, and the maximum allowable pressure drop were provided by the customer. Parametric studies were run to determine the effectiveness as a function of number of rows, fins per inch, and fin type. Based on the analysis, a final design was selected that best met the customer requirements.
Additionally, a full scale demonstration heat pipe was built and tested to determine the optimum fluid charge for the heat pipe heat exchanger. The power transfer capacity and the associated heat pipe ∆T are a strong function of the fluid charge in long, vertically oriented heat pipes. The test pipe was charged with various amounts of R-134a refrigerant and the optimum charge was determined to achieve the highest level of energy transfer at the lowest ΔT.
Air The final design was an AAHX that contained 540 individual heat pipes, ten (10) rows deep, with aluminum corrugated fins spaced at 14 fins per inch. The pressure drop of the air through the heat pipe heat exchanger was approximately 1.0 inch of water. The ACT AAHX was delivered in August 2013.