Constant Conductance Heat Pipes (CCHPs) have been a proven technology for spacecraft thermal control for more than 40 years. A CCHP transports heat over long distances (up to 3 m (10 feet) or more) from a heat source to a heat sink with a very small temperature difference. ACT currently has over 50 million hours in orbit for our CCHP product line (as of March 5th, 2018).
Future spacecraft and instruments developed for space science missions will involve highly integrated electronics, such as for CubeSat/SmallSat and high power laser diode arrays (LDAs). This high-density electronics packaging leads to substantial improvement in performance per unit mass, volume and power. However, it also requires sophisticated thermal control technology to dissipate the high heat flux generated by these electronics systems. For example, the current incident heat flux for laser diode applications is on the order of 5-10 W/cm2, although this is expected to increase towards 50 W/cm2. This is a severe limitation for the commonly employed axial groove aluminum/ammonia CCHPs. Hence, high flux heat acquisition and transport devices are required.
Typically, aluminum/ammonia CCHPs are used for transferring the thermal loads on-orbit due to their high wick permeability and associated low liquid pressure drop, resulting in the ability to transfer large amounts of power over long distances in micro-gravity. The maximum heat flux in a CCHP is set by the Boiling limit, where the working fluid within the evaporator wick structure starts to boil. If the heat flux is high enough, vapor bubbles will form and partially block the liquid return from the condenser to the evaporator, resulting in wick dryout. As the boiling limit is approached, the thermal resistance will continue to increase beyond the design parameters. In order to increase the heat flux limit to more than 50 W/cm2, Advanced Cooling Technologies, Inc. (ACT) developed a high heat flux heat pipes with a hybrid wick that contains screen mesh, metal foam, or sintered evaporator wicks, which can sustain high heat fluxes, for the evaporator region. The axial grooves in the adiabatic and condenser sections can transfer large amounts of power over long distances due to their high wick permeability and associated low liquid pressure drop as shown in Figure 1.
Heat spreaders are currently used in high heat flux applications to reduce the heat flux from the heat source to a level that can be accepted by the conventional axial grooves CCHP. This heat spreader adds weight, volume, thermal resistance, and cost to the system. ACT’s high heat flux CCHPs as shown in Figure 2 will eliminate the need of using these heat spreaders and will address a need for more demanding spacecraft thermal performance.
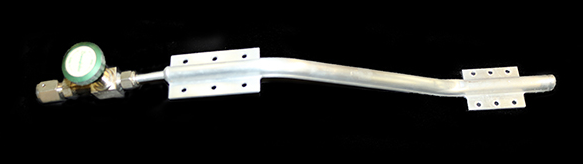
Figure 2. ACT’s High Heat Flux Heat Pipe Based on the Hybrid Wick Technology
The performance of the new high-heat-flux heat pipe was validated after testing at ACT and Lockheed Martin (LM) Coherent Technologies, Inc. Figure 3 shows the comparison of the thermal resistance at ACT an LM as a function of power for the high heat flux heat pipe at ~ 5º adverse tilt. The high-heat-flux aluminum/ammonia CCHP transported a heat load of > 300 Watts with heat flux input of > 50 W/cm2 and thermal resistance < 0.012 ºC/W. Note the differences in the thermal resistance for the two test are caused by minor differences in the test setup. This demonstrates an improvement in heat flux capability of more than 3 times over the standard axial groove aluminum-ammonia CCHP design, also shown in Figure 3.
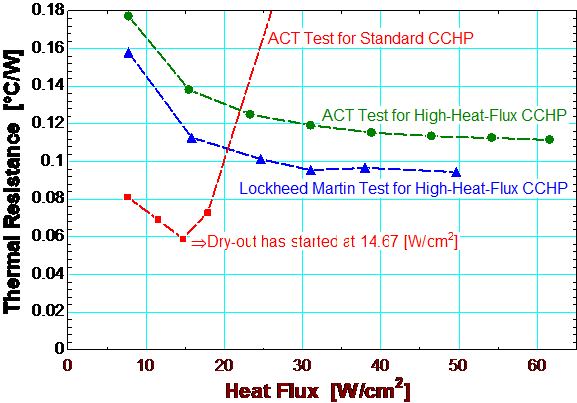
Figure 3. Thermal performance profile for the hybrid aluminum/ammonia high heat flux heat pipe and 10 °C condenser set point at 5° adverse elevation.
The testing results demonstrate that these new heat pipes perform efficiently, consistently and reliably and can adapt to many high heat flux applications. Accelerated life test show that the expected life for the hybrid high-heat-flux heat pipe exceeds 20 years.