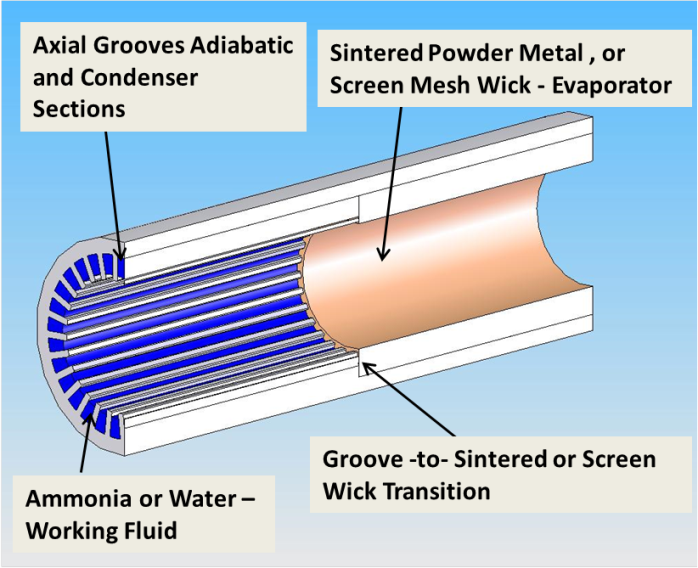
Grooved Constant Conductance Heat Pipes (CCHPs) transport heat from a heat source to a heat sink with a very small temperature difference. Aluminum/ammonia CCHPs are used for transferring the thermal loads on-orbit due to their high wick permeability and associated low liquid pressure drop, resulting in the ability to transfer large amounts of power over long distances in a micro-g environment. The maximum heat flux into a CCHP is set by the boiling limit, which is roughly 5 to 15 W/cm2 for typical grooves.
In order to increase the heat flux limit to more than 50 W/cm2, ACT developed heat pipes with a hybrid wick that contains screen mesh, metal foam, or sintered evaporator wicks for the evaporator region, which can sustain high heat fluxes, where the axial grooves in the adiabatic and condenser sections can transfer large amounts of power over long distances due to their high wick permeability and associated low liquid pressure drop as shown in the figure to the right.
- For 0.5” OD aluminum/ammonia hybrid heat pipe, boiling and capillary limits are shown in the chart to the right as a function of the evaporator’s sintered wick thickness in the CCHPs performance.
- The boiling limit can be improved by minimizing the wick thickness in the evaporator, but the capillary limit will be reduced. As the boiling limit is more sensitive and important than the capillary limit in hybrid CCHPs, the 0.06 in. (1.5 mm) wick should be selected
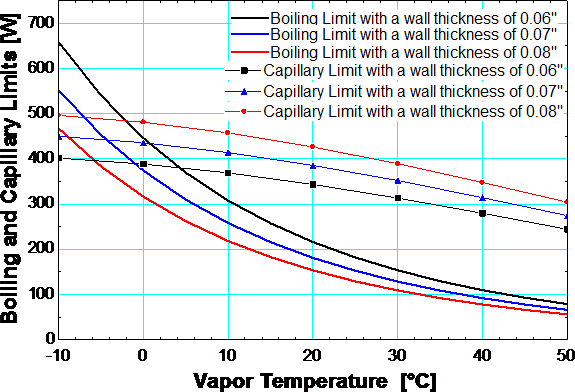