As the power density of electronic devices and lasers continue to increase, new cooling strategies such as pumped two-phase (P2P) cooling are needed to maintain their temperatures below maximum operating limits and provide a necessary high degree of isothermality to optimize performance and lifetime. ACT has developed bench-scale and standalone two-phase cooling systems that can handle several hundred Watts per square centimeter of thermal power and provide excellent temperature control and uniformity.
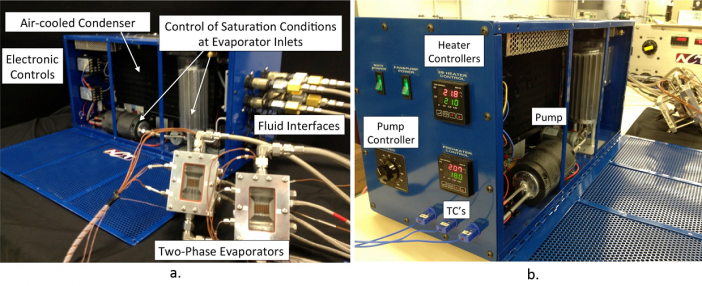
Figure 1 shows a stand-alone two-phase cooling system developed at Advanced Cooling Technologies, Inc. (ACT) that is capable of handling heat loads upwards of 300W/cm2 while maintaining tight temperature control and isothermality over the heat transfer area. In addition, the unit can handle multiple, separate, non-uniform and transient heat loads on the different evaporators. As noted, the unit is self-contained and simply has to be plugged in, setpoint temperatures input and thermal loads mounted to the two-phase evaporators. This apparatus has been used to test advanced two-phase evaporators, some of which are quite large and some of which include the use of microporous coatings to improve boiling performance.
In the design of the unit, particular attention has also been given to address flow maldistribution between multiple evaporators and flow and thermal instabilities internal to the evaporator and at the system level. Regarding flow maldistribution, it is important since adequate flow to and within each evaporator is essential to avoid local dry-out and overheating. In addition, internal controls automatically adjust the saturation conditions of the refrigerant prior to the evaporator inlet(s) such that the refrigerant boils as it enters the evaporators providing optimal cooling. A two-phase mixture of liquid and vapor exits each evaporator, which is eventually condensed onboard the unit.
For those unfamiliar with pumped two-phase cooling systems, it should be noted that the key components in the system include a pump, preheater, surge tank, condenser, accumulator and evaporator(s). The surge tank consists of vapor and liquid at saturation; by controlling the pressure in the tank, the saturation (boiling) temperature of the working fluid can be controlled. The preheater heats the subcooled liquid exiting the condenser prior to entry into the evaporator(s) to again adjust saturation conditions and achieve optimal cooling performance.