What is a Rotating Heat Pipe?
A Rotating Heat Pipe (RHP) is a two-phase heat transfer device that is designed to cool machinery by removing heat through a rotating shaft. As shown in Figure 1 below, heat input to the evaporator vaporizes the working fluid. As in a normal heat pipe, the vapor travels down the heat pipe to the condenser, where heat is removed as the vapor condenses. While a normal heat pipe uses a wick to return the condensate, a rotating heat pipe uses centrifugal forces. The inside of the heat pipe is a conical frustum, with the evaporator inside diameter (I.D.) larger than the condenser I.D. A portion of the centrifugal force is directed along the heat pipe wall, due to the slight taper. A copper-methanol rotating heat pipe is shown in Figure 2.
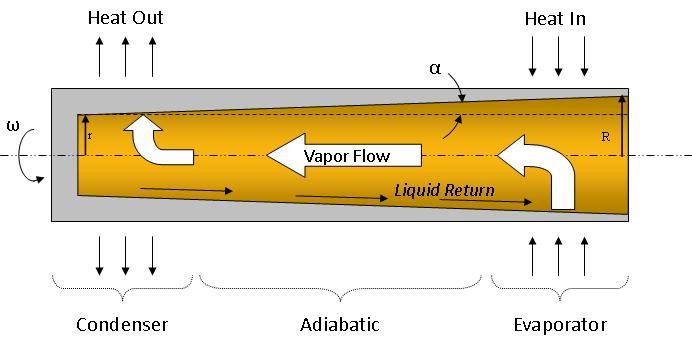
Figure 1. Rotating Heat Pipe Schematic.
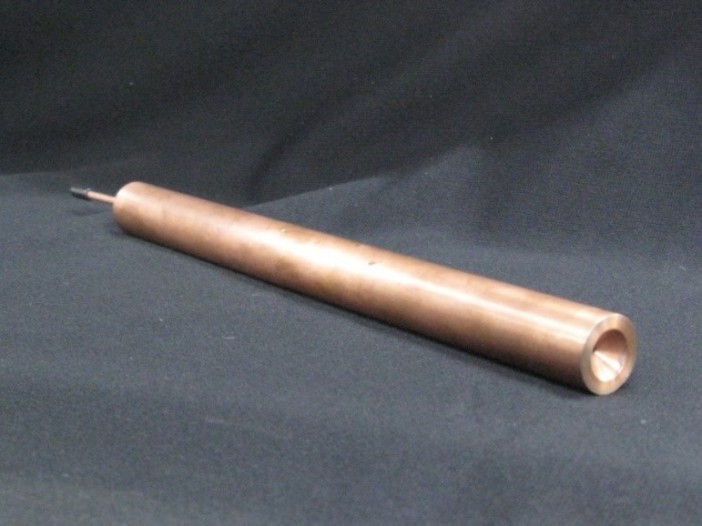
Figure 2. Copper-Methanol Rotating Heat Pipe.
When are Rotating Heat Pipes Used?
Rotating Heat Pipes can be used to remove heat generated in motors and other rotating machinery, e.g., electric motor/stator heat build-up, gear heat loads, bearing heat generation, etc. Most shafts are made of steel or stainless steel and have poor thermal conductivity. By implementing heat pipes into the shaft, the effective thermal conductivity can be increased with little strength/weight penalty. Figure 3 and Figure 4 show a rotating heat pipe test apparatus developed by ACT. It is capable of testing at rotational speeds up to 10,000 RPM, with an IR heater capable of 4kW supplying heat to the evaporator, and a liquid-cooled condenser. RTD temperature sensors and a high-speed slip ring are used with a Keithley DAQ system to provide real-time data readings.
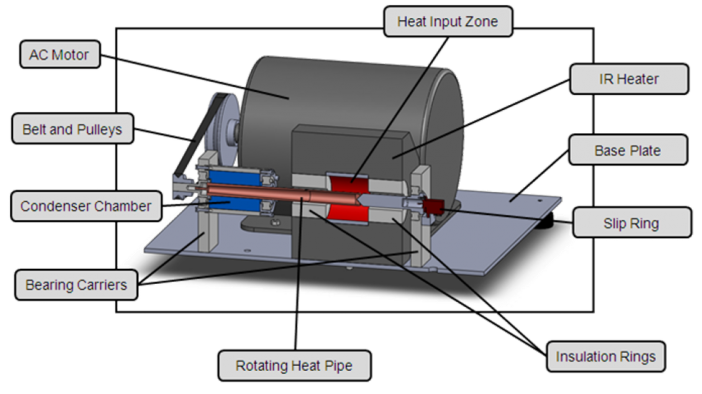
Figure 3. Cross-Section of the Rotating Heat Pipe Test Apparatus.
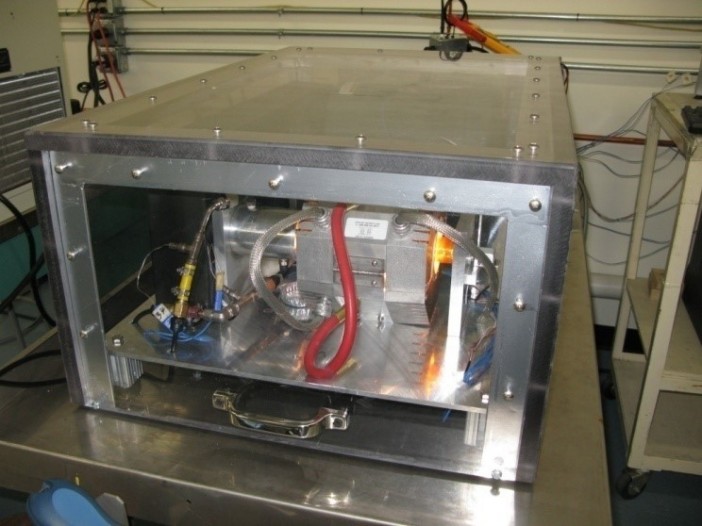
Figure 4. Rotating Heat Pipe Test Apparatus during RHP testing (the glow is from the IR lamps supplying heat to the heat pipe).
How are Rotating Heat Pipes and Rotating HiK™ Shafts Different?
The rotating HiK™ shaft is a less expensive, higher-performance alternative to a rotating heat pipe. As shown in Figure 4 and Figure 5, a series of freeze-tolerant copper/water heat pipes are embedded in the shaft that requires cooling. The heat pipes are angled so that centrifugal forces help return condensation from the condenser to the evaporator. The major difference between a rotating HiK™ shaft and a rotating heat pipe is that wicked heat pipes can be used in the HiK™ shaft. This wick can be designed so that the heat pipe can withstand numerous freeze/thaw cycles. Performance is improved compared with a methanol rotating heat pipe since water is one of the best heat pipe working fluids.
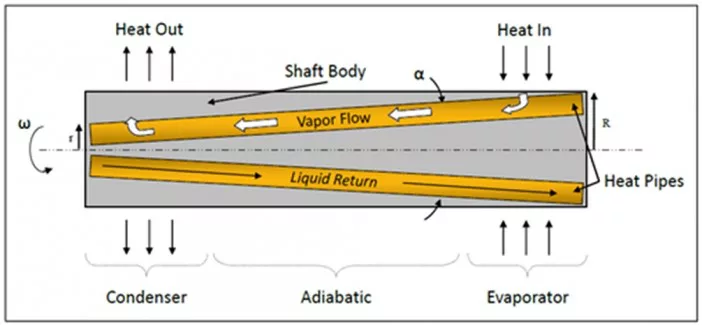
Figure 5. The rotating HiK™ shaft has a series of embedded heat pipes that are tilted so that centrifugal forces help return the condensate.
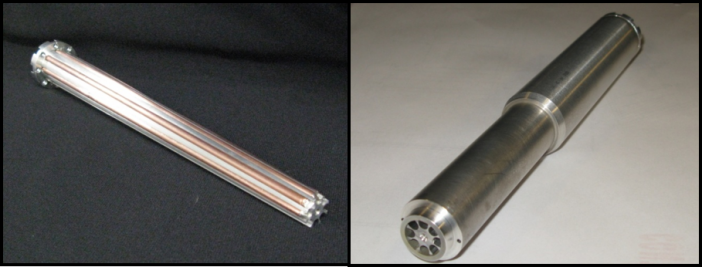
Figure 6. Rotating HiK™ Shaft with embedded, freeze-tolerant copper-water heat pipes.
Benefits of Rotating HiK™ Shafts
The benefits of the rotating HiK™ shaft for rotor cooling are shown in Figure 7. In a conventional system, the heat generated by the rotor needs to be transferred through air gaps, leading to high temperatures in the rotor. In contrast, heat is removed more directly and efficiently with a rotating HiK™ shaft versus a rotating heat pipe.
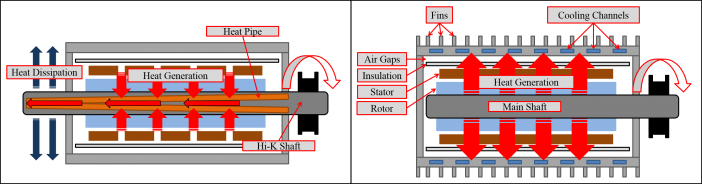
Figure 7. Conventional rotor cooling is inefficient since it relies on conduction across a shaft. In contrast, HiK™ shafts take the heat outside of the motor to provide thermal management
Rotating HiK™ Shafts Testing
Rotating HiK™ shafts were tested in ACT’s rotating heat pipe test apparatus, shown in Figure 4 (above). Tests were conducted at 1000, 2000, 3000, 4000, and 6000 RPM. Good agreement with theoretical limits was obtained at RPMs under 3000 RPM, see Figure 8. At higher speeds, the operating limit exceeded the capabilities of the IR Heater, and dry out could not be reached.
Rotating HiK™ Shaft Benefits
- Improved Performance, with reduced thermal resistance
- Improved reliability – multiple heat pipe design provides redundancy
- Reduced cost, since standard copper/water heat pipes can be used
- Potential Weight Savings
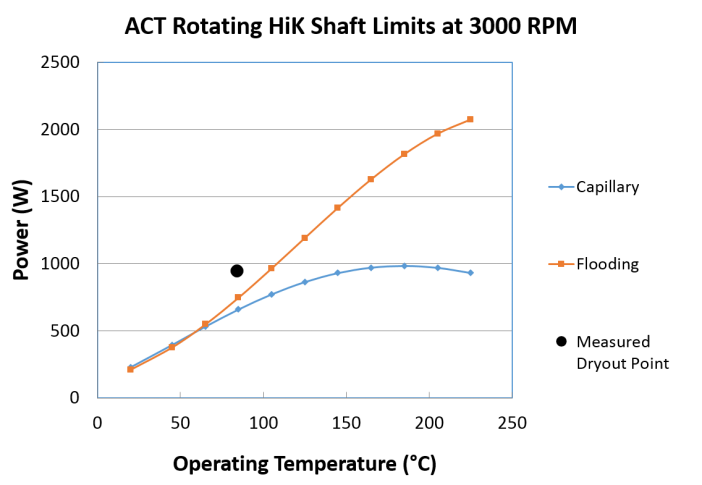
Figure 8. Predicted and Measured Dryout for a Rotating HiK™ Shaft. At speeds above 3000 RPM, the operating limit exceeded the capabilities of the IR Heater, and dry-out could not be reached.