Introduction
Pumping stations and their associated control stations are integral to a functioning municipal water system, therefore it is important that all control systems are designed to minimize downtime.
Many municipal water authorities utilize booster pump stations to deliver properly pressurized water to homes, businesses, and factories. The pumping stations typically draw water from a remote reservoir or aquifer and monitoring enables correctly regulated water pressures. These booster pump stations are fitted with industrial programmable logic controllers (PLCs), pumps, and drives. An important feature of these stations is that they are connected to wireless internet networks, which allows technicians quick access to system performance information to provide faster servicing when a unit becomes inoperable. While being able to identify issues across large networks of booster pump stations is important, adding in redundancy and minimizing the risk of failure on equipment is critical in preventing unnecessary downtime.
Challenges
- Internal Enclosure Temperatures: The original booster pump enclosures were not insulated, so any heat generated by the internal components was conducted through the interior of the enclosure to the outside metal surface of the enclosure. Depending upon outside temperatures the conductance of the metal enclosure to reject the internal heat load was not enough to keep the internal temperatures within operating range.
- Debris: These booster pump stations were located in residential areas, the enclosures were prone to mold due to weed whacking, leaf blowing, and grass cutting around the stations; these activities increase the number of particles in the surrounding air, and these particles can ultimately be drawn into nearby pump station enclosures. Without an enclosure cooling product that offers a NEMA-rated seal, the likelihood of mold and organic particles entering the pump station greatly increases. A sealed solution was necessary to neutralize the threat of contamination.
Solution
The solution for keeping the stations cool and sealed was offered by a CSIA-certified system integrator. The internal heat loads from the equipment were calculated along with the possible ambient outside seasonal temperatures. After utilizing ACT’s enclosure cooling selection tool, the integrator chose ACT’s HSC-45 above-ambient heat exchanger, which produces up to 900 watts of sealed cooling. The HSC-45 is thermostatically controlled by the PLC and only functions when needed to cool the station. Diagram 1 shows the HSC-45’s cooling method via fins that are thermally bonded to the center plate. Fans circulate air through the fins, thus providing the efficient heat transfer and cooling that the station’s interior required.
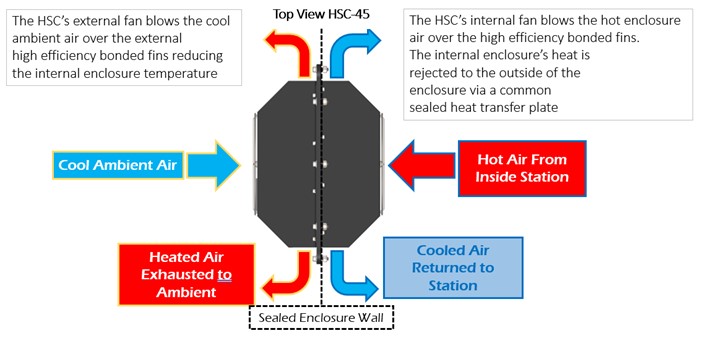
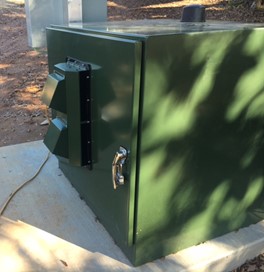
To avoid drawing unnecessary attention to the side-mounted unit, a requirement called for the ACT-HSC-45 to match the color of the station. Additionally, special tamper-proof mounting screws and rain hoods further protect and conceal the cooling unit. The ACT-HSC-45 heat exchanger fins and mounting plate are ElectroFin® corrosion-resistant powder-coated, and the housing is constructed of 316 stainless steel. These features environmentally rate the system for NEMA-4X installations. In total, these design elements provided the booster pump stations with a better-performing and more secure enclosure solution.
Testing
The system integrator made the recommendation for ACT’s HSC series of units based on a self-conducted summertime rooftop test. Multiple enclosures by finish and color were included in the test. Each enclosure was internally monitored for temperature. The ACT-HSC unit had the best test results based on internal enclosure temperature.
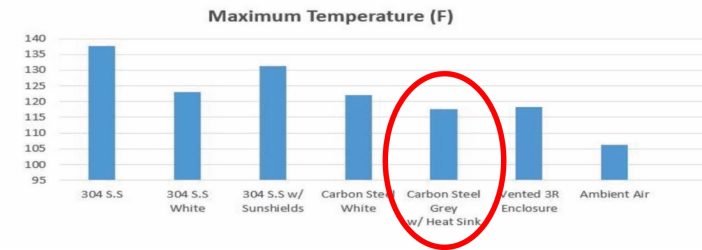
Graph 1: Roof Top Test Results
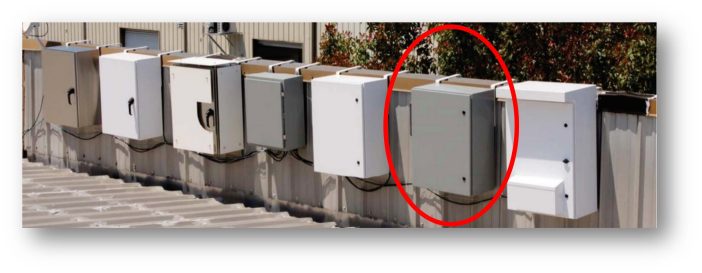
Photo 1: Multiple enclosure test stand
Photo 2: ACT-HSC-22 shown mounted for testing
Click here for more information about ACT’s cooling systems and customization options.