5 THINGS YOU NEED TO KNOW ABOUT HEAT PIPES IN SPACE
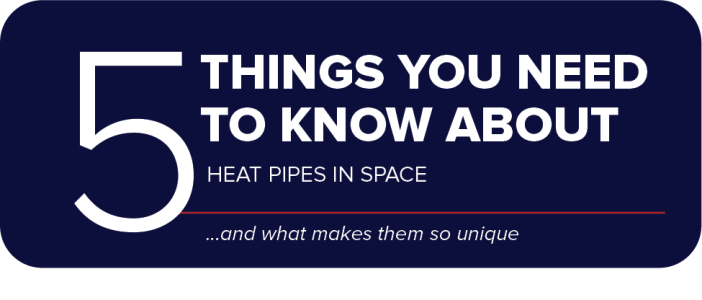
- HEAT PIPE WORKING FLUIDS AND WICK STRUCTURES: Axial groove aluminum-ammonia heat pipes have been the long-standing workhorse of the space industry, but other heat pipe configurations have flight legacy as well and can better service certain applications. In particular, high heat fluxes preclude axially groove wick aluminum-ammonia heat pipes because they can only support moderate heat fluxes (5-15 W/cm2). Another attribute precluding ammonia is the limited transport capability above 70°C. There are many other heat pipe working fluids that have spaceflight validation. Water and liquid metals can be used for applications that are warmer than ammonia’s operational limits, and methane and propylene can be used for operations down to cryogenic temperatures. Other wick structures that have been flown include sinter metal powder wicks and metal screen wicks. Resource: Working Fluid and Envelope Compatibility Table
- TEST LIKE YOU FLY: Gravity has always presented a hurdle for testing space-grade heat pipes when trying to test the heat pipes as close to flight conditions as possible. Testing in a horizontal or a very slight (~0.1”) adverse gravity orientation has become the preferred method, but still presents a challenge for non-planar heat pipes (three-dimensional bends). Another aspect of space heat pipe testing that can be overlooked is that of secondary conduction paths. While not as critical for steady-state testing, transient tests (e.g., freeze-thaw/temperature cycling) may not show accurate dynamic responses if the source mass, sink mass, and secondary paths are not accounted for in testing.
- COMBINING THERMAL TECHNOLOGIES: Heat pipes are an ideal solution to thermal challenges due to their passive nature, simple construction, and ease of customization. From a system-level design perspective, heat pipes can be easily implemented to solve the thermal challenge of transporting heat from a satellite bus to a radiator panel. Furthermore, heat pipes can be used at the bus level to efficiently move and spread heat from the heat sources to convenient contact surfaces for transfer to the radiator panels. One alternate application for heat pipes is to use the heat pipes in conjunction with a phase change material (PCM) heat sink. PCM heat sinks are primarily used in spacecraft to reduce radiator size for a pulsed power application by sizing the radiator for the time-averaged heat load rather than the maximum instantaneous heat load. In this application, heat pipes can be used to spread heat planarly across the PCM heat sink input surface and/or spread the heat into the PCM thickness to overcome the low thermal conductivity of common phase change materials.
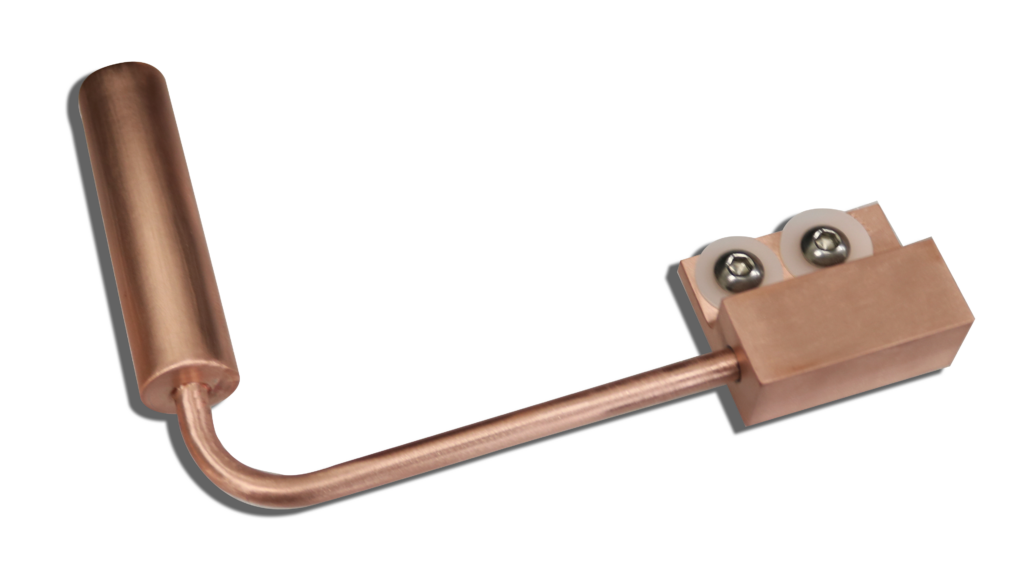
- WATER IN SPACE: Despite its effectiveness in small, high-heat flux applications, the use of water as a heat pipe working fluid for space has been avoided due to concerns with freezing. Fortunately, proper design and application in the past several years has led to its qualification in the form of copper-water heat pipes. ACT has developed and refined the design, manufacturing, and part filtering processes required to yield a spaceflight-worthy copper-water heat pipe product that can withstand harsh space environments. Special attention must be paid to both fluid inventory and wick construction, among other critical items to assure survivability through the maximum number of freeze-thaw cycles required for a particular mission. While test data has shown limitations to the maximum number of freeze-thaw cycles a SCWHP can withstand, ACT has shown success in a variety of qualification programs with over 1,000 freeze-thaw cycles.
- OTHER HEAT PIPES: There are a lot of heat pipe options available to help you control the thermal response of your system and meet system requirements. Aluminum-ammonia CCHPs are a great tool when it comes to satellite and spacecraft thermal control, but they do have their limitations. Alternative heat pipe options include Space Copper Water Heat Pipes (SCWHPs), Variable Conductance Heat Pipes (VCHPs), Diode Heat Pipes, and Loop Heat Pipes (LHPs), each with its own specific application. You can find out more about each heat pipe detailed here and other options for spacecraft thermal management – including options for higher or lower (cryogenic) temperature ranges – here on our website. Discover more technologies to support your mission.
Top
Page Index