Understanding Heat Pipe Combinations-Materials, Fluids, and Operating Ranges
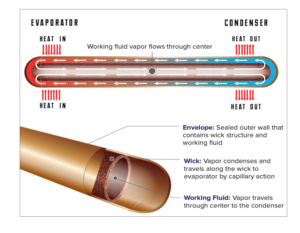
One of ACT’s most popular and long-standing videos on YouTube is “Heat Pipe Basics and Demonstration,” originally posted in 2021. While the video is a few years old, the content remains a valuable high-level overview of heat pipe operation. It’s an ideal starting point for engineers and thermal designers interested in learning more about heat pipe technology.
A common follow-up question from viewers is: “What working fluid and wick material combinations are typically used in heat pipes?”
This is a great question, and one that gets to the heart of heat pipe design. The answer depends on several factors, but the key is material compatibility—the working fluid must be chemically stable with both the envelope (outer casing) and the wick structure inside the heat pipe.
There are many possible heat pipe material combinations, each optimized for specific temperature ranges and applications. For example:
- Helium and stainless steel for cryogenic applications down to -271°C
- Water and copper for electronics cooling around 30°C to 150°C
- Lithium and stainless steel or refractory metals for high-temperature applications above 1000°C
When selecting the best heat pipe combination, the first step is determining your required operating temperature range. For a heat pipe to function properly, it must maintain saturated conditions—that is, it must contain both liquid and vapor phases. This means the selected working fluid must operate between its triple point (where it freezes) and its critical point (where liquid and vapor become indistinguishable).
While there are countless potential fluid-envelope-wick combinations, here are a few of the most common and proven options used in the field: Click to View the Heat Pipe Compatibility Chart