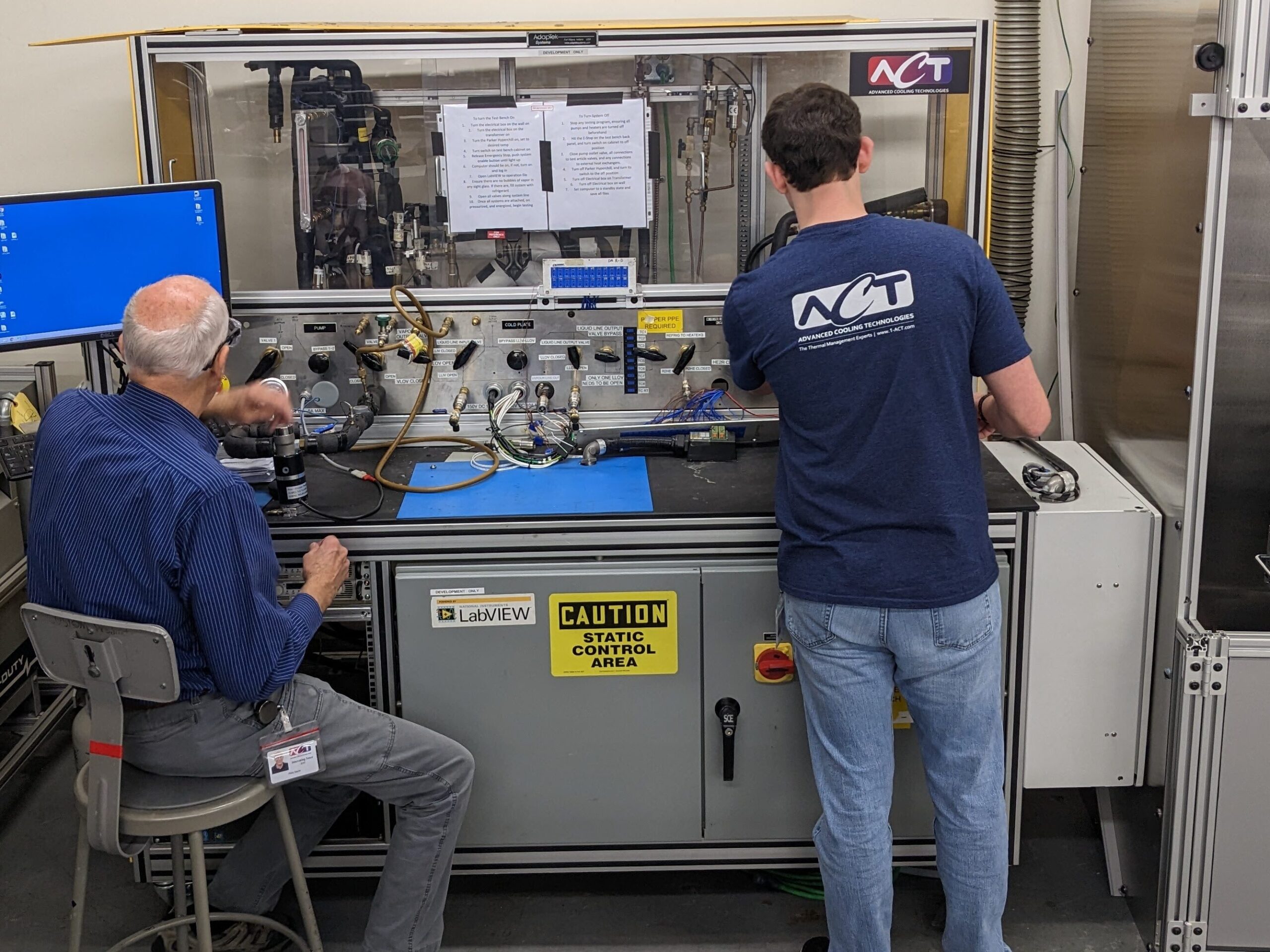
ACT was approached by a customer to develop custom two-phase cold plates for a pumped two-phase (P2P) thermal management system to be used in a high power directed energy weapons application. Under this program, ACT designed, built, and tested two large cold plates to cool and isothermalize a large array of high-power density electronics. To qualify the cold plate design, ACT also designed, built, and delivered a custom test system with a full P2P loop that interfaced with an external chiller.
The two-phase isothermal cooling test system contained a full P2P loop consisting of the custom cold plates, a condenser heat exchanger for heat rejection to an external chiller loop, a reservoir, and a pump. A control system was developed for the P2P loop for maintaining the cold plate inlet temperature and system pressure. This control system included a temperature-actuated flow control valve for inlet temperature control, and heating and cooling of the two-phase reservoir to maintain saturation pressure. The heat load on the cold plates were mimicked by heaters epoxied to the surface in the electronics footprint. The two-phase isothermal cooling test system was fully instrumented to monitor fluid temperature and pressure at multiple locations, cold plate temperature, and coolant flow rates. The final delivered test system, shown below in Figure 3, was equipped with a control panel and data acquisition system and was contained on a movable cart.

The pumped two-phase isothermal cooling test system was used to evaluate the performance of the cold plates, which had strict temperature uniformity (isothermality) requirements. The customer required that the temperature of the cold plates be maintained within ±2°C of a target temperature, and vary by less than 3°C over the entire cold plate. Figure 4 shows the cold plate temperatures along the length of a channel on each plate, which satisfactorily met the customer requirements.