Typical spacecraft radiators use aluminum/ammonia heat pipes embedded in a radiator with aluminum face sheets, and operate at temperatures below 70°C. NASA was interested in developing a high temperature titanium/water heat pipe radiator, operating in the 27 to 280°C temperature range. Since minimizing mass is extremely important in spacecraft radiators, the first step in the radiator development was to conduct a radiator trade study.
Initially, a thorough component level study was completed to determine heat pipe operating properties over the temperature range, particularly at the high end where the Merit Number starts fall off. Heat pipe designs for different dimensions were developed, and the maximum heat pipe power was determined. A trade study was then conducted that calculated the radiator performance and mass while varying the independent variables:
- Temperature: 550, 500, 450, 400, 350, 300 K
- Fin Thermal Conductivity: 300, 600, 1000 W/m K
- Fin Thickness: 0.01 to 0.1 in. by 0.01 in. (0.254 mm to 2.54 mm by 0.254 mm).
- Overhanging Fin Width: 0.5 to 6.0 in. by 0.5 in. (1.27 cm to 15.2 cm by 1.27 cm).
- Heat Pipe O.D.: 3/8, 1/2, 3/4, and 1 inch O.D. (0.95, 1.22, 1.85, and 2.49 cm I.D.).
For each case, the system dimensions and masses were calculated. Next, the temperature drops through the system were calculated:
- Temperature drop from the secondary loop NaK to the outside of the heat pipe
- Temperature drop through the evaporator wall.
- Temperature drop through the evaporator wick.
- Temperature drop in the vapor.
- Temperature drop through the condenser wick.
- Temperature drop through the condenser wall.
- Temperature drop through the graphite saddle.
- Temperature drop into the middle of the fin.
- Temperature drop along the fin.
The radiated power and system mass were then used to find the specific power. The figure below shows how the specific power varies with fin width at 150°C.
The optimum radiator design was then calculated from all of the different possible radiator designs. Specific powers for the optimum design are shown below for three different fin conductivities.
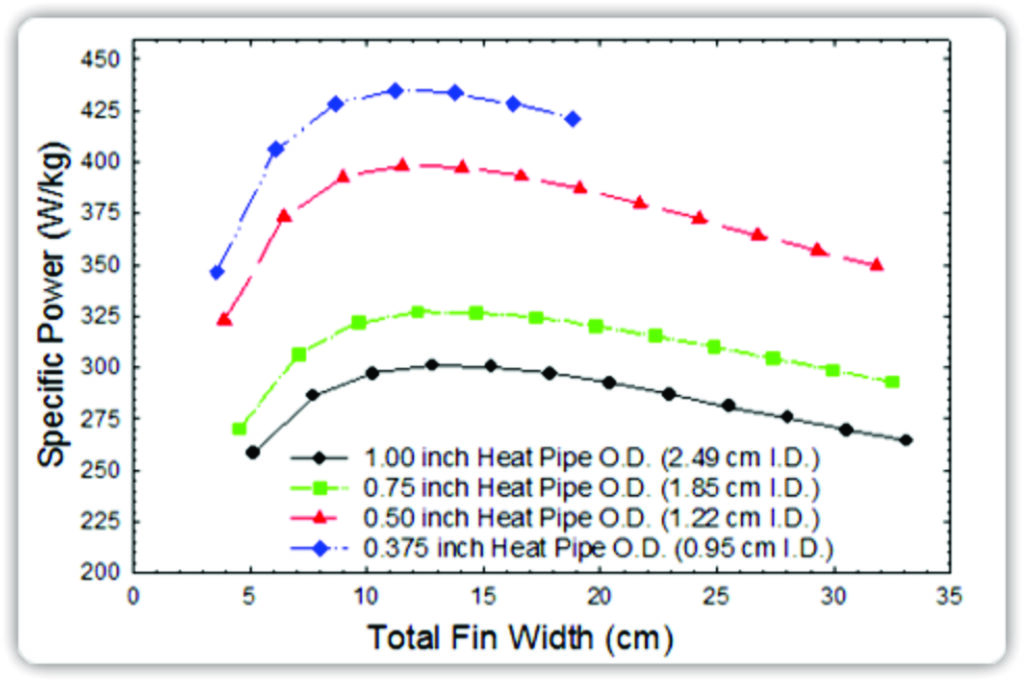
The optimum radiator design was then calculated from all of the different possible radiator designs. Specific powers for the optimum design are shown below for three different fin conductivities.
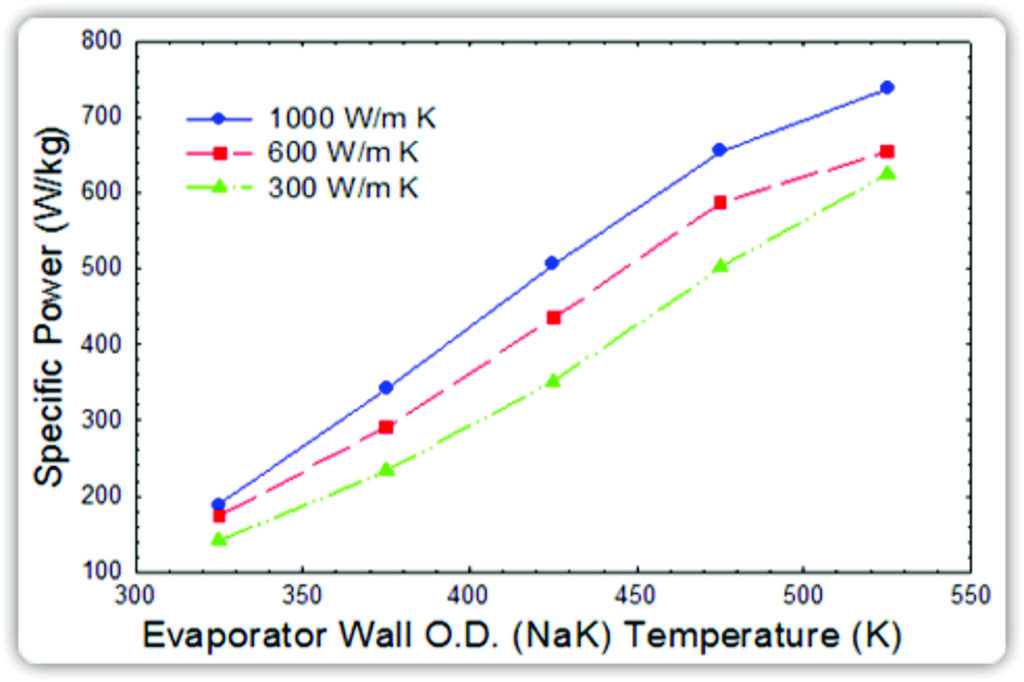