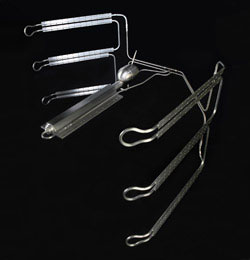
LOOP HEAT PIPE (LHP) PRODUCTS
Loop Heat Pipes (LHPs) made by ACT can transport larger amounts of heat over longer distances than traditional copper/water heat pipes. Loop Heat Pipes (LHPs) are often used in conjunction with Constant Conductance Heat Pipes (CCHPs) and Variable Conductance Heat Pipes (VCHPs) to transfer waste heat from spacecraft payloads to radiators. Ammonia is the most commonly used working fluid for temperatures between -40° and 70°C. Propylene and ethane fluids are used for lower temperature applications. ACT has also developed titanium/water Loop Heat Pipes (LHPs) for temperatures between 70° and 250°C.
Unlike some of our competitors, all of our Loop Heat Pipe parts, including the primary and secondary wicks, are quality made here in the United States at ACT under strict AS9100 quality controls. When you contact us about Loop Heat Pipes (LHPs), you’ll be speaking to the people that engineer and manufacture them.
Loop Heat Pipe (LHP) APPLICATIONS
- Payload thermal management
- Heat transport
- Radiator panel enhancement
- Avionics cooling
- Aircraft anti-icing
Loop Heat Pipe (LHP) Manufacturing
Throughout the Loop Heat Pipes (LHPs) manufacturing process, parts are continually checked to verify that they meet the performance requirements. For example, the LHP primary wick is characterized to determine its porosity, pore radius, permeability, and thermal conductivity.
The Loop Heat Pipes (LHPs) secondary wick performs the critical function of hydraulically linking the primary wick and the reservoir. ACT has the facilities and processes to fully characterize the performances of Loop Heat Pipe (LHP) secondary wicks at various power and body force conditions. ACT also has a Loop Heat Pipe (LHP) evaporator/reservoir characterization apparatus for quick and accurate assessment of the performance of an LHP evaporator/reservoir assembly, prior to installing it into the overall transport line and condenser assembly.
Loop Heat Pipe (LHP) Testing
These tests typically include:
- Start-up
- Transient power
- High power
- Shut-down
- Unbalanced condenser heat removal (in case of multiple condensers)
At times it is desirable for the LHP to stop transferring heat to maintain the temperature of the payload and minimize the magnitude of the temperature swing through an orbit. The figure below demonstrates the ability to shut down a LHP almost immediately and with a very small heater power. With a small heat input of approximately 10 Watts to the reservoir, the condenser temperature dropped quickly to match the environment, while the evaporator stays nearly constant in temperature.
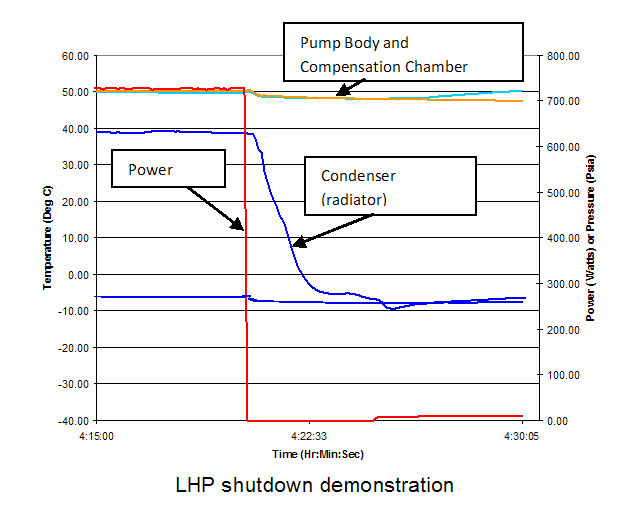
A Comparison of Different of Manufacturing Methods for Loop Heat Pipes
Loop Heat Pipe Type | Wick Structure | Pore Radius | Vapor Seal | Pros | Cons |
---|---|---|---|---|---|
Traditional | Sintered Nickel | ~1µm | Knife Edge Seal | -Heritage – Smallest pore radius for highest thermal performance – Design could use low thermal conductivity wicks for even higher thermal performance | – Complex manufacturing sequence |
Hybrid | Sintered Nickel | ~1µm | Deposited (Additive Manufacturing) | – Maintains traditional LHP pros from above – Knife-edge seal eliminated | – Complex manufacturing sequence – TRL 3 |
3D Printed | 3D Printed | ~8-10µm | Integral to 3D Print | – Simplified manufacturing sequence -short fabrication process | – Lower heat transport capacity – AM process may trigger additional qualification – TRL 6 |
3-D Printed Loop Heat Pipes
Loop Heat Pipes (LHPs) are commonly used in spacecraft applications, as they can transport larger amounts of heat over longer distances compared to conventional heat pipes. Due to the intricate geometry of the evaporator and compensation chamber, conventional machining methods can take an extended time and come at a high cost. To meet current industry needs, additive manufacturing (3D-Printing) allows for rapid design and fabrication of LHPs. ACT’s has mastered the control of porous prints, allowing for the wicked structure within the evaporator to be printed alongside the solid envelope, rapidly creating a seamless printed component.
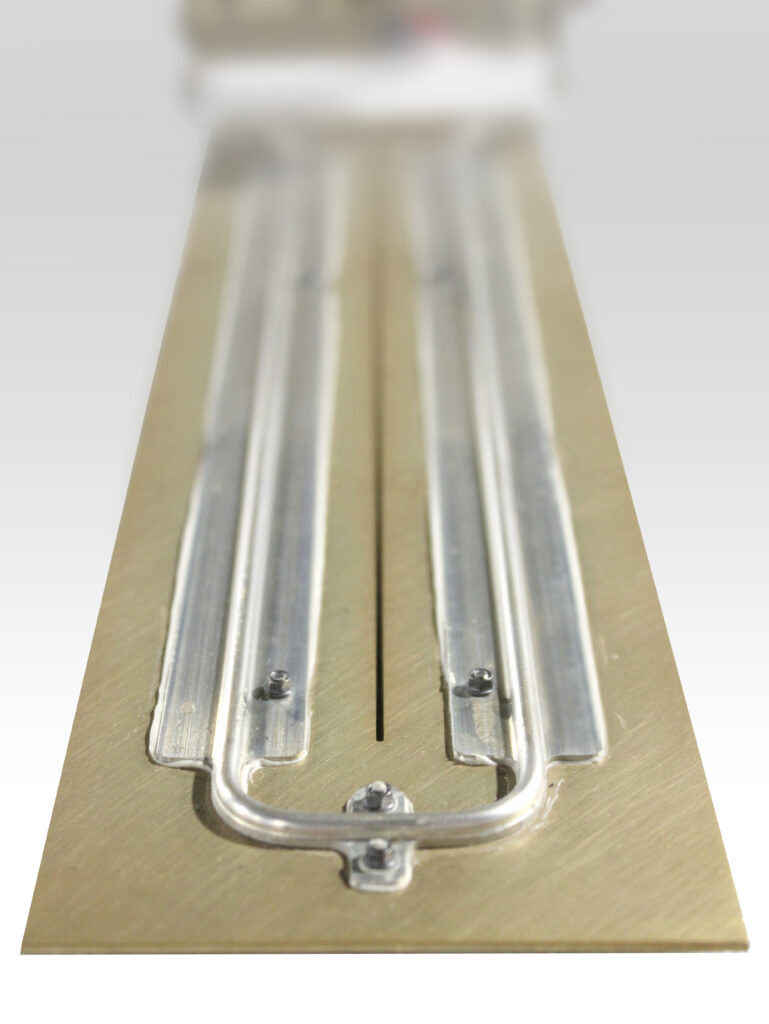
Publications:
- Gupta, R., Chen, C-H., and Anderson, W.G., “3D Printed Wicks for Loop Heat Pipes,” 52nd International Conference on Environmental Systems, ICES Paper 2023-158, 2023.
- Gupta, R., Chen, C-H., and Anderson, W.G., “Experiments on a Loop Heat Pipe with a 3D Printed Evaporator,” 51st International Conference on Environmental Systems, ICES Paper 2022-357, 2022.
- Gupta, R., Chen, C-H., and Anderson, W.G., “Progress on 3D Printed Loop Heat Pipes,” 50th International Conference on Environmental Systems, ICES Paper 2021-154, 2021.