ACT is a leading provider of Phase Change Material (PCM) heat sinks for military, aerospace and industrial thermal management applications
How Do Phase Change Material (PCM) Heat Sinks Work?

PCM Heat Sinks can absorb thermal energy (heat) with minimal temperature rise during the solid-to-liquid phase transition. During this phase transition, the latent heat (J/kg) is at least one (1) to two (2) orders of magnitude higher than the sensible energy that can be stored by the specific heat of a material in its solid or liquid phase. Figure 1 illustrates this phenomenon by plotting the temperature rise of a PCM over time with steady-state energy input.
In practice, a PCM is contained in a hermetically sealed enclosure and used to maintain the temperatures of critical heat-generating components over a given period of time.
Phase Change Material (PCM) Heat Sinks Applications
- Applications such as missiles that have finite mission life can utilize PCM energy storage to replace complex active thermal management solutions.
- PCM Modules are also used in systems having pulse mode operations by storing the heat during the “on” cycle and dissipating the heat (as the PCM refreezes) during the “off” cycle. Explore ACT’s Defense page.
- PCM is an emerging technology in the Spacecraft market for thermal control. PCM has the ability to store more thermal energy in a smaller package, with less mass when compared to some of the more traditional thermal solutions, and therefore is attractive to the booming space market.
Although the concept of storing heat by melting a phase change material is fairly simple, there are numerous practical challenges that must be addressed to obtain a volume or mass-optimized, fully functional and highly reliable PCM heat sink design. ACT has the expertise and experience in all areas from initial evaluation, through prototyping to full-volume production of PCM heat sinks.
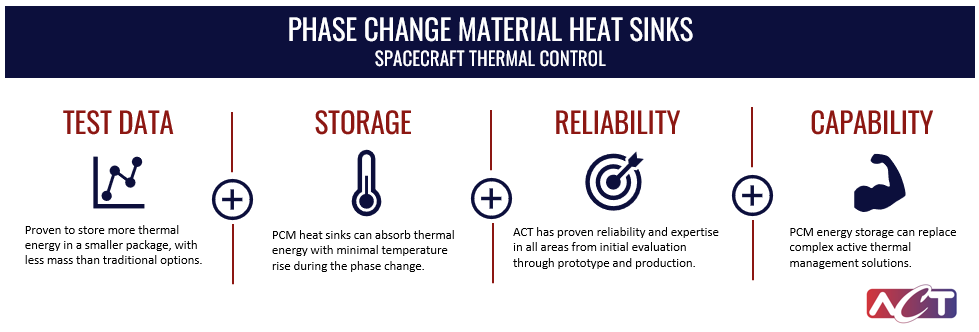
How do I select a Phase Change Material (PCM) for my heat sink?
The first consideration when designing a PCM heat sink should be the PCM’s melt temperature. Typically, the PCM is selected to provide a melting temperature that is several degrees lower than the maximum component temperature throughout the mission. Paraffin waxes are common because they are available with a wide range of melt temperatures. The second consideration is the energy that must be stored and the duration. The combination of these two factors, along with the thermal properties of the PCM, will ultimately determine the amount of PCM required in your system.
Read More on PCM Selection advice
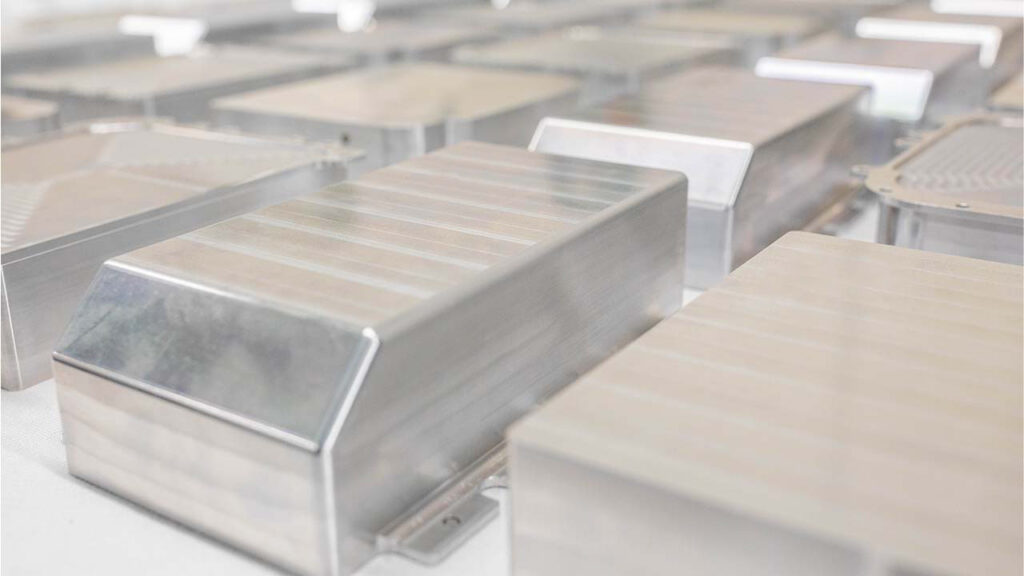
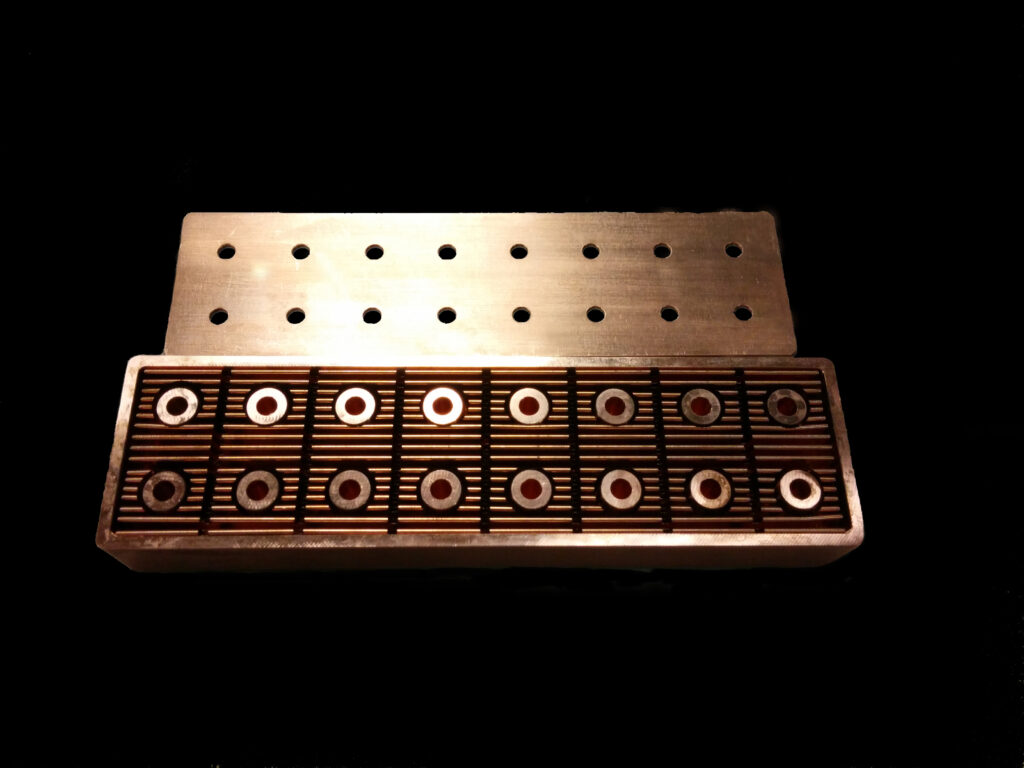
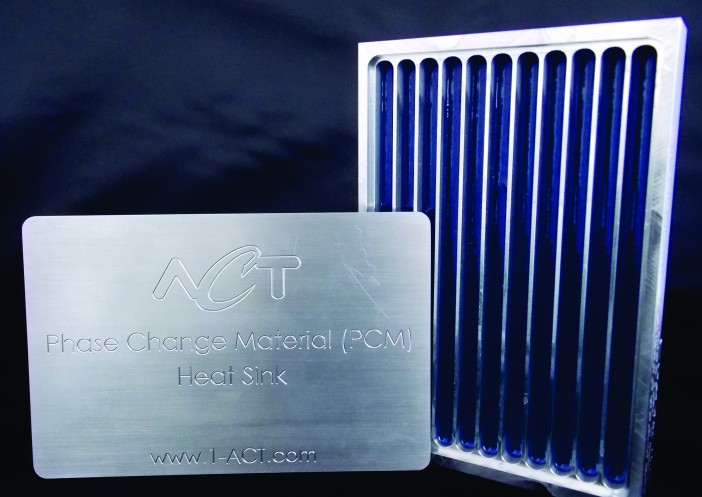
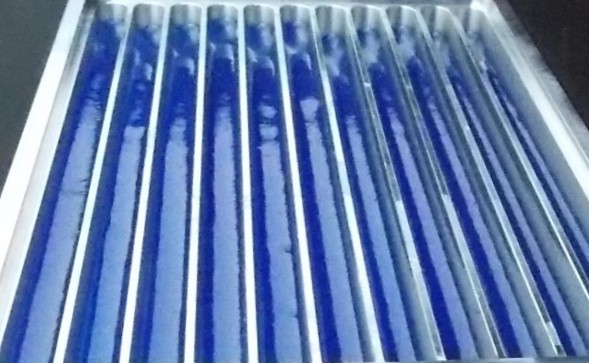
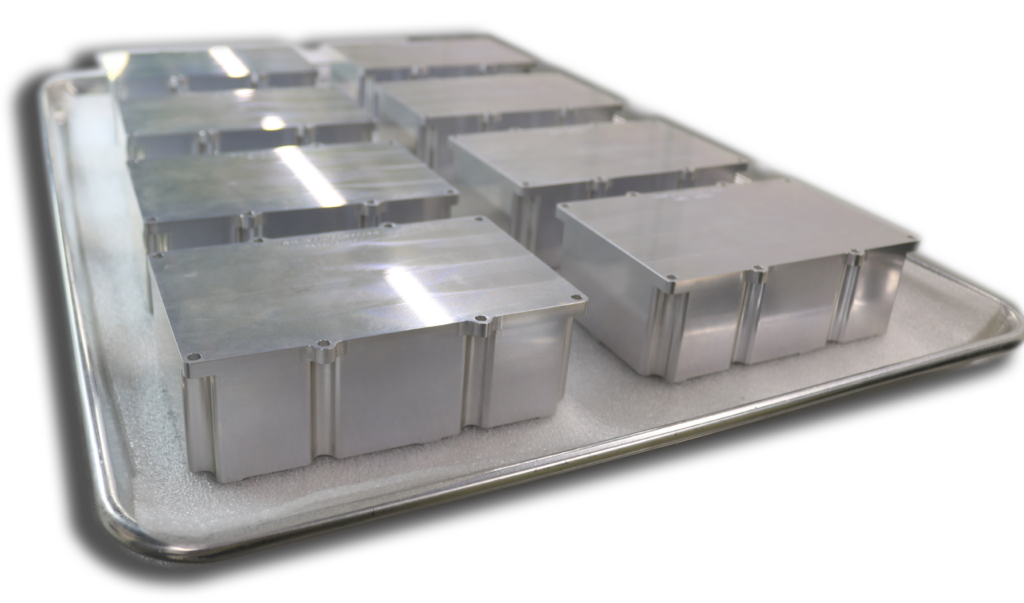
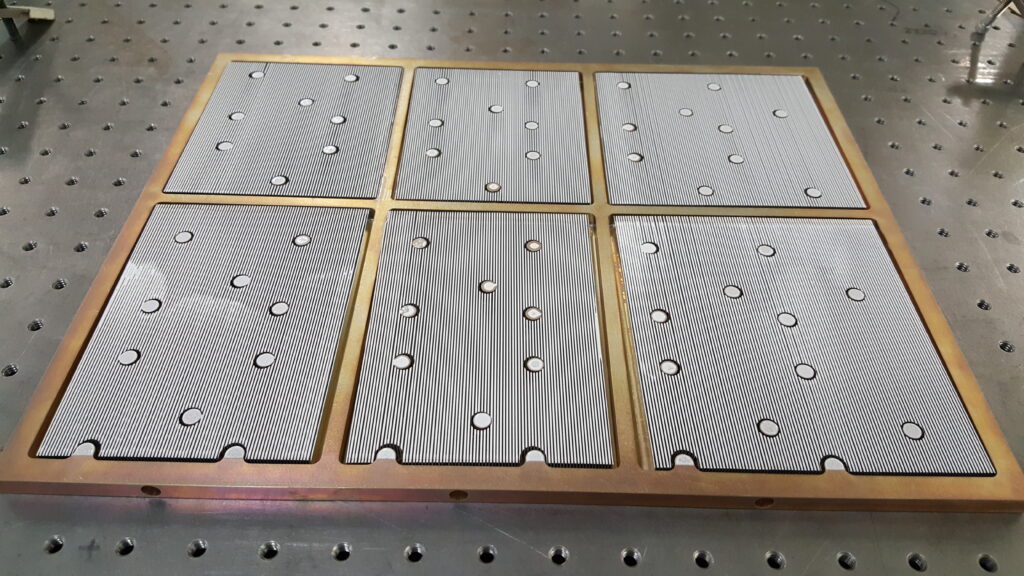
Phase Change Material (PCM) Heat Sink Design Considerations
The challenge with many PCM Heat Sink Designs is the poor thermal conductivity of the PCM. For example, paraffin waxes typically have thermal conductivities of less than 1 W/m-K. This is remedied by adding internal features to increase the overall effective thermal conductivity of the enclosure. ACT is experienced with fins, heat pipes and metal foams as options for these internal structures.
PCM heat sink design considerations
Thermal Simulations of Phase Change Material (PCM) Heat Sink Systems
ACT has expertise in analyzing PCM systems and accurately predicting transient responses. In-house analytical tools in combination with computational fluid dynamics (CFD) software are leveraged for thermal simulations involving PCM.
In most cases, a dynamic specific heat is created to capture effects during multiple stages.
ACT has developed a PCM heat sink calculator that provides a temperature profile as a function of time for up to three Phase Change Materials. It also estimates the mass and volume and volume for the PCM heat sink. *Note that this calculator assumes a general fin thickness. ACT develops custom solutions with the optimal fin thickness for each application’s unique requirements.
Critical Manufacturing of Phase Change Material Heat Sink Systems
Since 2015, ACT has been designing and manufacturing PCM Heat Sinks for some customers from the most high-profile defense suppliers, to innovative high-profile disrupters in the commercial sector (customers and project details confidential). Our depth of experience in not only the design but also the manufacturing of custom PCM Heat Sink solutions positions us to be your trusted partner of choice for PCM Heat Sinks.
ACT has developed the necessary manufacturing technologies required to produce high-quality, high-reliability PCM heat sinks. Some of these manufacturing technologies include
- PCM project evaluation and thermal design
- PCM heat sink prototyping and production
- Aluminum vacuum brazing
- Precision charging of PCM
- Safe and reliable sealing of the PCM assembly
- Pressure, leak and thermal testing
PHASE CHANGE MATERIAL (PCM) SELECTION
There are several factors that need to be considered when selecting a phase change material. An ideal PCM will have high heat of fusion, high thermal conductivity, high specific heat and density, long-term reliability during repeated cycling, and dependable freezing behavior. In Table 1 below, red indicates challenges. You can also reference our PCM Heat Sink Calculator to find the right material for your application.
There are several classes of phase change materials. Paraffin waxes are the most common PCM for electronics thermal management because they have a high heat of fusion per unit weight, have a large melting point selection, provide dependable cycling, are non-corrosive, and are chemically inert. According to our in-house PCM experts, when designing with paraffin PCM, void management is important due to the volume change from solid to liquid (see Figure 1). Paraffin PCMs also have a low thermal conductivity, so designing sufficient conduction paths is another key design consideration.
Hydrated salts are another category. These PCMs have a high heat of fusion per unit weight and volume, have a relatively high thermal conductivity for non-metals, and show small volume changes between solid and liquid phases. These are not commonly used for electronics heat sinks, since they are corrosive and long-term reliability (thousands of cycles) is uncertain. The most common application is for very large thermal storage applications (e.g., solar heating), where a much lower cost is very attractive.
Other PCM materials such as non-paraffin organics, and liquid-to-gas phase change materials are available but are not often used for electronics heat sinks. Metallic PCMs are generally used at high temperatures, where no suitable paraffin wax is available.
PCM Types Include Paraffin Waxes, Non-Paraffin Organics, Hydrated Salts, and Metallics.
pcm comparison table
Property or Characteristic | Paraffin Wax | Non-Paraffin Organics | Hydrated Salts | Metallics |
Heat of Fusion | High | High | High | Med. |
Thermal Conductivity | Very Low | Low | High | Very High |
Melt Temperature (°C) | -20 to 100+ | 5 to 120+ | 0 to 100+ | 150 to 800+ |
Latent Heat (kJ/kg) | 200 to 280 | 90 to 250 | 60 to 300 | 25 to 100 |
Corrosive | Non-Corrosive | Mildly Corrosive | Corrosive | Varies |
Economics | $$ | $$$ to $$$$ | $ | $$ to $$$ |
Thermal Cycling | Stable | Elevated Temperature Can Cause Decomposition | Unstable over Repeated Cycles | Stable |
Weight | Medium | Medium | Light | Heavy |
Paraffins are the most common PCM for electronics thermal management. They are chemically compatible with most metals. They have large latent heat and can be obtained over a wide temperature range.
Table 2 shows some high-purity paraffin waxes used in many electronics applications. Temperature ranges of 72-76°C, 66-70°C and 59-66°C are good to ensure the safe operation of many electronic devices. Many other PCM choices are also available, with melting points differing by a few degrees from -9°C to 90°C.
Table 2. Typical Paraffin Wax PCMs.
Examples of Paraffins | C36H74 | C32H66 | C30H62 |
Densitysolid (kg/m3) | 857 | 809 | 810 |
Latent Heat (kJ/kg) | 223 | 261 | 249 |
Tmelt (°C) | 72 to 76 | 66 to 70 | 59 to 66 |
To get started, tell us about your project.
- How Do Phase Change Material (PCM) Heat Sinks Work?
- Phase Change Material (PCM) Heat Sinks Applications
- How do I select a Phase Change Material (PCM) for my heat sink?
- Phase Change Material (PCM) Heat Sink Design Considerations
- Thermal Simulations of Phase Change Material (PCM) Heat Sink Systems
- Critical Manufacturing of Phase Change Material Heat Sink Systems
- PHASE CHANGE MATERIAL (PCM) SELECTION
- pcm comparison table